铝阳极氧化膜不同封孔方法的耐腐蚀性能研究
铝阳极氧化膜不同封孔方法的耐腐蚀性能研究
余祖孝 郝世雄 王莹 左由兵 易伟
(四川理工学院材料与化学工程系,四川自贡643000)
(四川理工学院材料与化学工程系,四川自贡643000)
摘要:用电化学法、磷-铬酸质量检测法和金相电子显微镜,研究了6种封孔方法对铝阳极氧化膜耐腐蚀性能的影响。结果表明,都在最佳工艺条件下,硬脂酸封孔后的氧化膜是最耐腐蚀的,依次是硫酸镍封孔后的,重铬酸钾封孔后的,沸水封孔后的,醋酸镍封孔后的,耐蚀性能最差的是氟化镍常温冷封孔后的。
铝是活泼金属,又是易钝化金属,铝在空气中能自然形成一层Al2O3·H2O或Al2O3氧化膜,该氧化膜可达0.01 μm~0.10 μm厚,这层天然氧化膜为非晶态,薄而多孔,力学强度也低,可以保护铝基质在中性和弱酸性溶液中不再进一步被腐蚀,起到一定的防护作用,但是远远满足不了人们对铝及其合金在防护性、装饰应用等方面的要求。为提高铝及铝合金的抗腐蚀性,常用铝阳极氧化的方法,表面形成厚而致密的氧化膜,同时必须进行封孔处理,才能改善铝及铝合金的耐蚀性、硬度和耐磨性能。目前,常用封孔方法有沸水封孔、重铬酸钾封孔、硫酸镍封孔、醋酸镍封孔、硬脂酸封孔和常温氟化镍冷封孔等。本文研究了在最佳工艺条件下,铝阳极氧化膜不同封孔方法对其耐腐蚀性能的影响。
1 试验
1.1 主要材料及仪器
1060工业纯铝板w(Al)=99.6%,尺寸为50 mm×25 mm×1mm。K2Cr2O7,硬脂酸,NiSO4·6H2O,HNO3,H3PO4,CrO3,丙酮等药品均为分析纯。电化学综合测试系统(LK98C,天津生产),金相电子显微镜(NiKon,日本生产),分析天平(TG328A),稳压稳流电源(YB1731 3A)。
1.2 工艺流程
铝板打磨(2000#金相砂纸)→冷水洗→丙酮除油→热水洗→冷水洗→碱蚀(50 g/L NaOH,45℃,2min) →热水洗→冷水洗→化学出光(78%H3PO4+11%H2SO4+11%HNO3,3min~5min) →冷水洗→阳极氧化(15%H2SO4,20 V,0.9 A/dm2~1.3 A/dm2,30mim,25℃) →封孔→老化→耐蚀性能检测。
1.3 耐蚀性能测定
(1)磷-铬酸质量检测方法。封孔后的氧化膜试样老化24 h,称重为m1,再浸入硝酸溶液(50%HNO3,10 min),用蒸馏水、酒精清洗,干燥,称重为m2,然后浸入磷-铬酸溶液(20 g/L CrO3+35 ml/L H3PO4,(38±1)℃,15 min),蒸馏水、酒精清洗,干燥,称重为m3。则试样单位面积S上的平均失重为:△m1,2=(m1-m2)/S(mg/dm2);△m1,3=(ml-m3)/S(mg/dm2);其失重越小(特别是△m1,3小),表明耐腐蚀性能越强,该封孔方法效果越好。
(2)电化学方法。工作电极:铝阳极封孔氧化膜(暴露面积1cm2,其余用环氧树脂密封);辅助电极:铂片;参比电极:饱和甘汞电极。用LK98C电化学综合测试系统测定氧化膜在1 mol/L NaCl溶液中的Tafel极化曲线(1 mV/s,25℃)。得到腐蚀电位和极化极限电流密度两个参数,如果腐蚀电位越大,极限极化电流密度越小,则该封孔氧化膜的耐腐蚀性能就越强。
2 结果与讨论
2.1 陈化对铝阳极氧化膜电化学性能的影响
铝板阳极氧化之后,未经过陈化与陈化24 h的试样,所测阳极极化曲线如图1。陈化时间对氧化膜腐蚀电位的影响不大。但是未陈化氧化膜的阳极极化电流密度急剧增大,最终极化电流密度达到最大值(即极化极限电流密度),发生明显的腐蚀现象。而陈化24 h的氧化膜,开始时极化电流也增大,但是极化极限电流密度相对较小,腐蚀有所降低。由此可见,陈化有利于提高铝阳极氧化膜的耐蚀性能。因此,本次试验的所有试样都是经过陈化24 h以后,再检测其耐蚀性能。
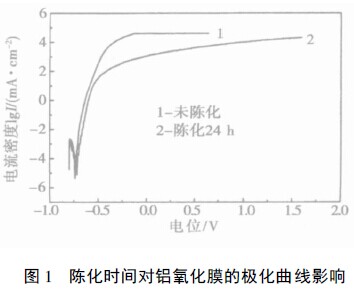
铝是活泼金属,又是易钝化金属,铝在空气中能自然形成一层Al2O3·H2O或Al2O3氧化膜,该氧化膜可达0.01 μm~0.10 μm厚,这层天然氧化膜为非晶态,薄而多孔,力学强度也低,可以保护铝基质在中性和弱酸性溶液中不再进一步被腐蚀,起到一定的防护作用,但是远远满足不了人们对铝及其合金在防护性、装饰应用等方面的要求。为提高铝及铝合金的抗腐蚀性,常用铝阳极氧化的方法,表面形成厚而致密的氧化膜,同时必须进行封孔处理,才能改善铝及铝合金的耐蚀性、硬度和耐磨性能。目前,常用封孔方法有沸水封孔、重铬酸钾封孔、硫酸镍封孔、醋酸镍封孔、硬脂酸封孔和常温氟化镍冷封孔等。本文研究了在最佳工艺条件下,铝阳极氧化膜不同封孔方法对其耐腐蚀性能的影响。
1 试验
1.1 主要材料及仪器
1060工业纯铝板w(Al)=99.6%,尺寸为50 mm×25 mm×1mm。K2Cr2O7,硬脂酸,NiSO4·6H2O,HNO3,H3PO4,CrO3,丙酮等药品均为分析纯。电化学综合测试系统(LK98C,天津生产),金相电子显微镜(NiKon,日本生产),分析天平(TG328A),稳压稳流电源(YB1731 3A)。
1.2 工艺流程
铝板打磨(2000#金相砂纸)→冷水洗→丙酮除油→热水洗→冷水洗→碱蚀(50 g/L NaOH,45℃,2min) →热水洗→冷水洗→化学出光(78%H3PO4+11%H2SO4+11%HNO3,3min~5min) →冷水洗→阳极氧化(15%H2SO4,20 V,0.9 A/dm2~1.3 A/dm2,30mim,25℃) →封孔→老化→耐蚀性能检测。
1.3 耐蚀性能测定
(1)磷-铬酸质量检测方法。封孔后的氧化膜试样老化24 h,称重为m1,再浸入硝酸溶液(50%HNO3,10 min),用蒸馏水、酒精清洗,干燥,称重为m2,然后浸入磷-铬酸溶液(20 g/L CrO3+35 ml/L H3PO4,(38±1)℃,15 min),蒸馏水、酒精清洗,干燥,称重为m3。则试样单位面积S上的平均失重为:△m1,2=(m1-m2)/S(mg/dm2);△m1,3=(ml-m3)/S(mg/dm2);其失重越小(特别是△m1,3小),表明耐腐蚀性能越强,该封孔方法效果越好。
(2)电化学方法。工作电极:铝阳极封孔氧化膜(暴露面积1cm2,其余用环氧树脂密封);辅助电极:铂片;参比电极:饱和甘汞电极。用LK98C电化学综合测试系统测定氧化膜在1 mol/L NaCl溶液中的Tafel极化曲线(1 mV/s,25℃)。得到腐蚀电位和极化极限电流密度两个参数,如果腐蚀电位越大,极限极化电流密度越小,则该封孔氧化膜的耐腐蚀性能就越强。
2 结果与讨论
2.1 陈化对铝阳极氧化膜电化学性能的影响
铝板阳极氧化之后,未经过陈化与陈化24 h的试样,所测阳极极化曲线如图1。陈化时间对氧化膜腐蚀电位的影响不大。但是未陈化氧化膜的阳极极化电流密度急剧增大,最终极化电流密度达到最大值(即极化极限电流密度),发生明显的腐蚀现象。而陈化24 h的氧化膜,开始时极化电流也增大,但是极化极限电流密度相对较小,腐蚀有所降低。由此可见,陈化有利于提高铝阳极氧化膜的耐蚀性能。因此,本次试验的所有试样都是经过陈化24 h以后,再检测其耐蚀性能。
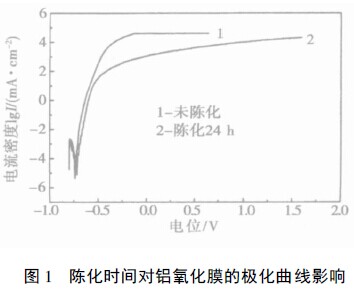
2.2 磷-铬酸法
作者根据腐蚀电位越大(即腐蚀倾向越小)、极化极限电流密度越小(即腐蚀速度越小)的原则,首先确定各种封孔方法的合理工艺条件:常温冷封孔的合理工艺条件,4.5 g/L~5.0 g/L NiF2,30min;醋酸镍封孔,5 g/L,85℃以上,45min;沸水封孔,pH5.5~6.5,20 min~30 min;重铬酸钾封孔,50 g/L,100℃,35min~40 min;硫酸镍封孔,8 g/L,90℃以上,40min;硬脂酸封孔,将氧化膜浸入100%且熔融状的高温硬脂酸中进行封孔,100℃,30 min~40 min。然后,在上述工艺下,得到6种封孔方法的铝阳极氧化膜,分别通过磷-铬酸质量检测。其氧化膜的失重结果如表1,表明6种封孔方法氧化膜的△m1,2变化不是很大,但是膜失重的规律与△m1,3相似,失重量△m1,3更能够体现氧化膜的耐腐蚀性。由表1看出,硬脂酸封孔效果最好。各种封孔方法的试样失重都远远小于未封孔的空白试样的。
作者根据腐蚀电位越大(即腐蚀倾向越小)、极化极限电流密度越小(即腐蚀速度越小)的原则,首先确定各种封孔方法的合理工艺条件:常温冷封孔的合理工艺条件,4.5 g/L~5.0 g/L NiF2,30min;醋酸镍封孔,5 g/L,85℃以上,45min;沸水封孔,pH5.5~6.5,20 min~30 min;重铬酸钾封孔,50 g/L,100℃,35min~40 min;硫酸镍封孔,8 g/L,90℃以上,40min;硬脂酸封孔,将氧化膜浸入100%且熔融状的高温硬脂酸中进行封孔,100℃,30 min~40 min。然后,在上述工艺下,得到6种封孔方法的铝阳极氧化膜,分别通过磷-铬酸质量检测。其氧化膜的失重结果如表1,表明6种封孔方法氧化膜的△m1,2变化不是很大,但是膜失重的规律与△m1,3相似,失重量△m1,3更能够体现氧化膜的耐腐蚀性。由表1看出,硬脂酸封孔效果最好。各种封孔方法的试样失重都远远小于未封孔的空白试样的。

2.3 电化学方法
对铝阳极氧化膜经过不同方法封孔后的极化曲线进行比较,如图2所示。从腐蚀速度来看(即极化极限电流密度),硬脂酸的极化极限电流密度是最小的。因此,硬脂酸封孔后氧化膜的耐蚀性能比其余几种封孔方法的好,其次是硫酸镍封孔的,重铬酸钾封孔的,沸水封孔的,醋酸镍封孔的和常温冷封孔的。这与用磷-铬酸质量检测法所得结果是一致的(见表1)。从腐蚀倾向来看(即腐蚀电位),硬脂酸、硫酸镍和重铬酸钾的腐蚀电位较大,醋酸镍、沸水和冷封孔的腐蚀电位较小(并且有点反常),未封孔的腐蚀电位最小。因此腐蚀倾向与用磷.铬酸质量检测所得结果基本上是一致的。
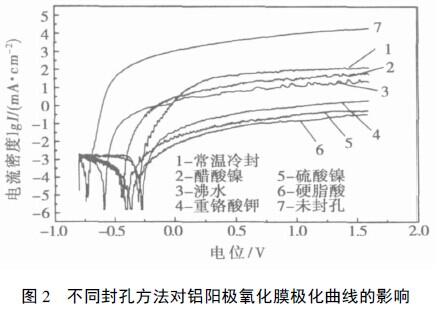
2.4 形貌
图3是用表面金相电子显微镜所观测的铝阳极表面氧化膜的表面形貌。从图3a、3b的形貌可知,NiF2冷封孔后的试样表面孔隙较多,相对于未封孔的试样表面要略少一些。可见,效果还不是很理想。这是因为在封孔过程中,F-消耗要比Ni2+的快得多,Ni2+和F-容易产生失调,则封孔度不足。而硬脂酸封孔后的试样表面孔隙很少,而且比较平整光滑(图3a、3c)。
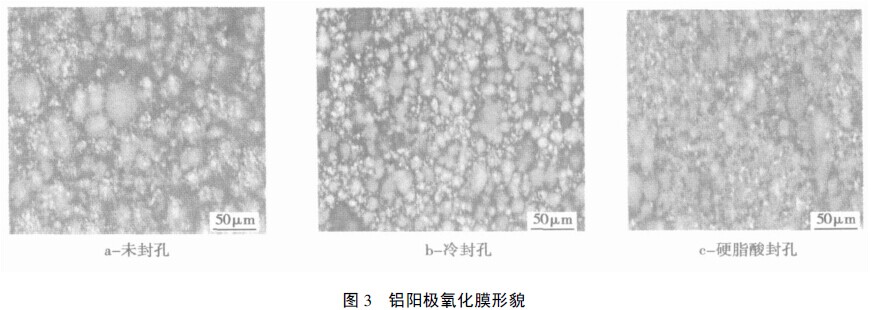
图3是用表面金相电子显微镜所观测的铝阳极表面氧化膜的表面形貌。从图3a、3b的形貌可知,NiF2冷封孔后的试样表面孔隙较多,相对于未封孔的试样表面要略少一些。可见,效果还不是很理想。这是因为在封孔过程中,F-消耗要比Ni2+的快得多,Ni2+和F-容易产生失调,则封孔度不足。而硬脂酸封孔后的试样表面孔隙很少,而且比较平整光滑(图3a、3c)。
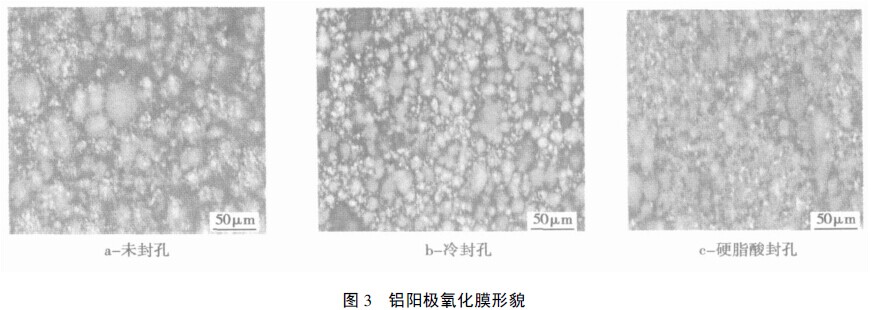
3 结论
通过对铝阳极氧化膜用不同方法封孔后的耐蚀性能进行比较和分析,都在最佳工艺条件下,其耐蚀性能由高到低的封孔方法排列顺序是:硬脂酸、硫酸镍、重铬酸钾、沸水、醋酸镍、常温冷封孔(氟化镍)。虽然常温冷封孔的耐腐蚀性能较差,但与未封孔相比,还是有一定的封闭效果,更重要的是不消耗能源。重铬酸钾、硫酸镍封孔效果好,但温度要求较高,重铬酸钾有毒;硬脂酸封孔效果最好,但温度要求较高,而加入异丙醇作溶剂后,温度有所改变。
通过对铝阳极氧化膜用不同方法封孔后的耐蚀性能进行比较和分析,都在最佳工艺条件下,其耐蚀性能由高到低的封孔方法排列顺序是:硬脂酸、硫酸镍、重铬酸钾、沸水、醋酸镍、常温冷封孔(氟化镍)。虽然常温冷封孔的耐腐蚀性能较差,但与未封孔相比,还是有一定的封闭效果,更重要的是不消耗能源。重铬酸钾、硫酸镍封孔效果好,但温度要求较高,重铬酸钾有毒;硬脂酸封孔效果最好,但温度要求较高,而加入异丙醇作溶剂后,温度有所改变。
下一篇: 铝阳极氧化膜常温封闭工艺的研究