铝及铝合金阳极氧化膜的绿色封闭工艺研究进展
铝及铝合金阳极氧化膜的绿色封闭工艺研究进展
李利
(中国船舶重工集团公司第七二五研究所,河南洛阳471023)
(中国船舶重工集团公司第七二五研究所,河南洛阳471023)
摘要:本文概述了铝及铝合金阳极氧化膜的新型封闭方法,着重介绍了稀土盐封闭、溶胶封闭和微波水合封闭三种新型绿色封闭的工艺及发展,并对其封闭机理作了简要概述,指出更多绿色、高效且易于工业化生产的铝及其合金阳极氧化膜封闭工艺将被开发。
铝及其合金的阳极氧化膜具有硬度高、绝缘性好、耐磨性优、耐蚀性良、结合力强等优点,故在建筑业、航空航天业、交通运输业、膜分离领域及许多高尖端领域得到了广泛应用。铝及铝合金阳极氧化膜属于多孔型氧化膜,由阻挡层和多孔层两部分组成。在腐蚀性介质中,氧化膜的外部多孔层很容易从外界吸收水和侵蚀性离子,而侵蚀性离子很容易穿过非常薄的阻挡层,因此铝及其合金的阳极氧化膜极易发生腐蚀,必须进行封闭处理。
铝及铝合金阳极氧化膜的封闭工艺有沸纯水封闭、高温水蒸汽封闭、以氟化镍为主体的冷封闭、以重铬酸盐和镍盐为主体的中温封闭、以丙烯酸系为主体的电泳涂装等。沸纯水封闭和高温水蒸汽封闭是借助于水在微孔中的缔合作用,生成水合离子封孔,虽简便实用,封闭质量高,但能耗高、工作环境较差,对水质要求严格,且封孔后的氧化膜容易吸附空气中的CO2,尤其是吸附沿海气候中的NaCl,造成微孔腐蚀,使得封孔工件的使用寿命短。冷封闭和中温封闭都是利用金属离子的水合和沉积作用对氧化膜孔进行填充封闭,但由于镍离子和铬离子对人体健康的危害很大,对环境的污染也较严重,故镍盐和铬盐封闭一直受到抑制。丙烯酸系电泳涂装不同于常规的封闭工艺,因丙烯酸树脂的粒径约为阳极氧化膜孔径的两倍,故丙烯酸树脂不能进入微孔之中,只能沉积在多孔层的表面将微孔覆盖。丙烯酸系电泳涂装工艺较为成熟,但涂装后的氧化膜与基体结合得不太紧密,且耐高温性也较差,使其发展受到了限制。从未来发展考虑,必须寻求无镍、无铬、无氟、工艺稳定、能耗低且对环境无污染的新型绿色封闭剂和封闭方法。
国内外许多学者寻求新型绿色冷封闭剂和中温封闭剂替代镍盐和重铬酸盐。新型绿色冷封闭剂有:钛和锆的化合物、硅酸盐和硫脲的水溶液、GYS-3封闭剂、氟锆酸盐和氟化钠的水溶液、ZHM-0612型无镍冷封闭剂等,新型绿色中温封孔剂有碱金属无机碱或盐类与强氧化性高价锰(碘)酸盐无机过氧化物的水溶液、MS-05A型中温封闭剂等。这些新型封闭剂能使封闭质量达到ISO·3210标准,但仍沿用传统的封闭工艺,仅改变了封闭剂的成分。还有许多学者不局限于传统的冷封闭工艺和中温封闭工艺,开发了不少新型封闭工艺,如:稀土盐封闭、溶胶封闭、微波水合封闭。本文重点介绍这三种新型封闭工艺的发展及研究现状。
1 稀土盐封闭
澳大利亚航空研究室材料科学部的Hinton等人首次报道了稀土盐对铝合金的缓蚀作用,将稀土盐作为抑制腐蚀剂,研究其抑制腐蚀的效果,证实了稀土盐可以有效抑制铝合金的腐蚀,提出用稀土盐代替传统的铝合金铬酸盐表面处理的可能性。之后美国南加利福尼亚大学的Mansfeld等人将稀土盐表面处理用于铝合金阳极氧化膜的封闭,研究了2024、6061和7075三种铝合金经硼酸-硫酸阳极氧化后采用不同铈盐和钇盐封闭的效果,结果发现硝酸铈和硫酸钇的封闭效果最好,且经两者封闭后的试样在0.5 mol/L NaCl溶液中的腐蚀阻抗与铬酸盐封闭的效果相当。之后,国内外的许多学者都开展了铝合金阳极氧化膜的稀土盐封闭研究。
稀土盐封闭是指通过化学方法或电化学方法在阳极氧化膜表面形成一层含稀土元素的转化膜。在阳极氧化膜上形成含稀土的转化膜的工艺主要有浸泡、阴极直流电沉积、外加脉冲电压沉积、交流电沉积和浸泡-电化学处理5种。
1.1 浸泡
Mansfeld等人将铝合金阳极氧化膜放入单一稀土盐中浸泡较长时间,才可在氧化膜表面形成含稀土的转化膜。后来,北京科技大学的李久青等人和中科院物理所的于兴文、曹楚南等人在稀土盐溶液中加入强氧化剂,大大缩短了浸泡时间。处理工艺为:Ce(NO3),3.0~10.0 g/L,氧化剂H2O2:0.2~0.9 g/L,缓冲剂A:0.01~0.07%,pH值:3.0~5.5,温度:10~50℃,处理时间:2 h。用该工艺处理后的铝合金阳极氧化膜的耐蚀性能与传统重铬酸钾封闭的效果相当。南方冶金学院的颜建辉等将处理液中铈盐的浓度提升到40 g/L,氧化剂H2O2的浓度提升到130 ml/L,处理时间可进一步缩短到25 min,封闭效果与氟化镍冷封闭效果相当。封闭机理可能是一方面氧化膜与水发生水合反应生成勃姆体的水合氧化铝AlO(OH),另一方面溶入氧化膜溶解生成OH-离子,使局部pH值升高,铈离子与OH-离子反应生成Ce(OH)3沉淀,水合氧化铝和铈的氢氧化物沉淀共同填充铝合金阳极氧化膜的微孔。
重庆大学的李凌杰等人将稀土盐处理液加热到95~98℃,再将铝合金阳极氧化膜放入其中浸泡,只需30 min就可在氧化膜表面形成一层含稀土的转化膜。还将铈盐、镧盐和钇盐封闭的效果进行了比较,结果发现:铈盐封闭的阳极氧化膜耐蚀性能最好,与传统的氟化镍封闭和铬酸盐封闭的阳极氧化膜具有可比性。
李凌杰等在研究中还发现单一的铈盐、锂盐封闭效果低于两者混合封闭,由此推断铈、锂盐封闭具有某种协同作用。铈、锂盐封闭工艺为:0.1%CeCl3和1%LiNO3(质量分数)的水溶液,pH值:5.0~5.5,温度:95~98℃,时间:30min。其封闭机理与单一稀土盐浸泡封闭的机理相似,由于锂离子的半径非常小,扩散速度较快,故在Ce(OH)3、AlO(OH)凝胶析出过程中Li+也夹杂在其中。另外,Ce(OH)3在空气中被逐渐氧化成Ce(OH)4,故氧化膜中的铈主要以四价形式存在,因此铈、锂盐封闭时微孔内的填充物有水合氧化铝及铈、锂的混合氢氧化物。铈、锂的混合氢氧化物具有更好的机械隔离作用,因此能更有效地提高膜的耐蚀性能。浸泡封闭的效果虽好,但能耗大、过程不易控制,故不适宜工业化大生产。
1.2 阴极直流电沉积
在稀土盐处理液中加入强氧化剂后虽能大大缩短浸泡处理的时间,但仅局限于化学方法,Stoffer开发了电化学(通直流电)成膜工艺,在铝合金基体表面直接沉积含铈转化膜。北京科技大学李国强、北京航空航天大学的彭明霞、李荻等首先将阴极直流电解沉积方法用于铝合金阳极氧化膜的封闭,将LY12铝合金阳极氧化膜放入添加铈盐的硫酸溶液中进行恒电流阴极极化处理,在氧化膜表面得到含铈转化膜。优化工艺为:1.5 ml/L硫酸和1.0 g/L铈盐的水溶液;电流密度:10
mA/dm2;温度:(25±2)℃,时间:30 min,
mA/dm2;温度:(25±2)℃,时间:30 min,
后经对比研究发现,用硫酸和铈盐阴极直流电解处理后的铝合金阳极氧化膜的耐蚀性能不如用氯化铈和双氧水阴极直流电解处理的。后者的工艺为:1 g/L CeCl3与10 ml/L H2O2的水溶液,pH:3.1,电流密度:5 mA/cm2,温度:室温,时间:1 h。阴极直流电沉积后的铝合金阳极氧化膜的耐蚀性与未沉积时的氧化膜相比显著提高,与传统封闭后的铝合金阳极氧化膜相比,耐蚀性如何却未见报道。有报道称在铝合金表面用阴极直流电沉积的稀土铈转化膜层结构疏松,耐蚀性能差,由此推测阴极直流电沉积后的铝合金阳极氧化膜耐蚀性也不好。
李国强、李荻等认为富铈转化膜的生成可能包括两个过程:(1)溶液中H2O2和溶解O2在阴极的电解还原(主要是H2O2的还原)引起阴极表面附近溶液pH值的局部升高;(2)当阴极附近溶液的局部pH值增加到大于8时,阳极氧化膜的化学溶解和四价铈盐的电还原这两个相互影响的过程开始发生,并最终导致胶态Ce(OH)3在多孔阳极氧化膜上的沉积。又在氧化膜的外层,Ce3+易被氧化成Ce4+,故铝合金阳极氧化膜孔内的封闭产物主要有含结晶水的氧化铝、Ce3+与Ce4+的氢氧化物(Ce(OH)3和Ce(OH)4)和氧化物(Ce2O3和CeO2)。
1.3 外加脉冲电压沉积
北京化工大学的赵景茂等人在阴极直流电沉积的基础上,开发了外加脉冲电压封闭。用铝盐水溶液作封闭液,把需进行封闭处理的铝及铝合金阳极氧化膜作为负电极浸入到封闭液中,且置于两块正电极(铅板)之间,正负电极通过电极与脉冲电源连接,控制脉冲电源的电压为0.2~1.5V,脉冲频率为50~800 Hz,保持正向工作比小于负向工作比,铝盐溶液中铝离子的浓度为0.5~5 g/L,室温下封闭20~40 min即可。脉冲电压封闭处理后的阳极氧化膜耐蚀性能远高于恒压封闭处理的,又含稀土铈的转化膜耐蚀性能与传统的氟化镍冷封闭膜和铬酸盐封闭膜的耐蚀性能相当,故赵景茂等用稀土铈盐溶液替代铝盐溶液对铝合金阳极氧化膜进行封闭处理。逐一研究了封闭液主盐、稳定剂、铈盐浓度对外加脉冲电压封闭效果的影响,得到最佳封闭工艺,即主盐:Ce(NO3)3,Ce3+浓度:1.5 g/L,稳定剂:丙三醇,脉冲电压:1.0 V,脉冲频率:50Hz,正向、负向工作比为1:1,正负向占空比为60%:35%,温度:30℃,封闭时间:30 min。用该工艺封闭的铝合金阳极氧化膜的耐蚀性能优于传统的重铬酸钾封闭和沸水封闭,有望替代重铬酸钾封闭。
陈爽等人还用硫酸钇溶液作封闭液外加脉冲电压封闭纯铝阳极氧化膜。与沸水封闭相比,硫酸钇封闭后的氧化膜表层更加致密,显微硬度和耐腐蚀性能均明显提高。Mansfeld用交流阻抗法研究了多种稀土盐封闭对氧化铝膜耐蚀性能的影响,发现硝酸铈和硫酸钇封闭的氧化膜耐蚀性能最好。两者中哪个封闭效果更好,目前仍未见报道。
外加脉冲电压的封闭机理可能是:当通入负向电流时,促使溶液中的氧与水分子发生如下反应:2H2O+O2+4e→4OH-,使多孔膜内呈现碱性环境,同时负向电压还有利于溶液中的Ce3+向阳极氧化膜内迁移,并与OH-发生反应形成沉淀封孔。当通以正向电流时,改变了阳极氧化膜多孔层界面电性能,从而更有利于负向电流过程中生成的OH-进入多孔层,使得多孔层内溶液的pH值增大,与孔内的Ce3+作用形成Ce(OH)3沉淀,填充多孔层而达到封孔的目的。氧化膜微孔内的填充物与阴极直流电沉积时的相同,主要有水合氧化铝、Ce3+与Ce4+的氢氧化物和氧化物。
1.4 正弦交流电沉积
阴极直流电沉积的时间较长,约1小时,而且膜层不均匀,大连理工大学的梁成浩等人发明了一种新的在铝及其合金阳极氧化膜内沉积含铈转化膜的新方法——正弦交流电沉积法。处理液为Ce(NO3)3、CeCl3和Ce(SO4)2中的一种或其混合物,若单独使用某一种铈盐,其含量为0.5~5 g/L;若选用混合铈盐,铈盐的总含量不超过6 g/L。处理液中添加少量氧化剂H2O2,含量为2~8 ml/L,浓度为35%。交流电沉积所用电源为50Hz的正弦交流电,电压:5~20 V,温度优选:18~30℃,时间优选:3~12 min。工作电极与对电极的面积比不得大于4:1。
大连理工大学的梁坤、梁成浩等经过进一步研究发现:当氧化膜的厚度大于5 μm才能形成转化膜,只有大于6.8 μm才能得到连续均匀的复合膜;且铈元素均匀分布在多孔氧化膜表层1.5 μm内。成膜机理与阴极直流电沉积封闭的成膜机理相似,不同的是采用交流电沉积时,可施加的电压较大,沉积速度快。氧化膜作为阴极的半周期内,离子在氧化膜内发生还原反应,并产生部分缺陷;作为阳极的半周期内,氧化膜发生氧化反应,并对阻挡层的缺陷进行修复。当交流电不断发生的还原反应与阻挡层被修复的过程中,使电子更易发生流动,促进阳离子在氧化膜内发生还原反应,富铈转化膜沉积得较快。
氧化膜微孔内的填充物与阴极直流电沉积的相同,主要有水合氧化铝、Ce3+和Ce4+的氢氧化物和氧化物。用该方法封闭铝合金阳极氧化膜时,与阴极直流电沉积类似,稀土铈元素在氧化膜上沉积的不均匀,耐蚀性也不如传统重铬酸盐封闭。因此,交流电沉积不适用于阳极氧化膜的封闭,常用于形成功能性纳米线阵列、纳米管等。
1.5 浸泡-电化学处理
Mansfeld将高温浸泡和电化学方法相结合,开发了Ce-Mo盐处理工艺,即将铝合金先后在100℃的Ce(NO3)3溶液和CeCl3溶液中浸泡2h,再在Na2MoO4溶液中恒电位极化(+500mV vs SCE)30 min,可在铝合金基体表面获得含铈和钼的转化膜。清华大学的田连朋等将Ce-Mo处理工艺用于铝合金阳极氧化膜的封闭,处理工艺:先在40℃的Ce(NO3)3溶液(10 mmol/L)中保持30 min,再在40℃的CeCl,溶液(5 mmol/L)中保持30 min,最后室温在Na2MoO4溶液(0.1 mmol/L)中恒电位极化(+500mV vs SCE)30 min。经EMA能谱分析发现:Ce和Mo存在于整个阳极氧化膜层。用动电位极化法研究发现:铈-钼盐封闭得到的铝合金阳极氧化膜的耐蚀性能优于传统的氟化镍封闭和重铬酸钾封闭。
铈-钼盐封闭的机理可能是:Ce(NO3)3溶液和CeCl3溶液首先对阳极氧化膜层进行表面改性,然后铈盐沉淀封闭多孔层;在电化学处理中,进入膜层中的MoO2-4起到和Cr6+类似的作用,抑制腐蚀发生。铈盐和钼盐协同作用,减小了局部腐蚀的敏感性,提高了阳极氧化膜的耐蚀性。
浙江海洋学院的王春涛等和合肥工业大学的孙衍乐等直接在铝合金阳极氧化电解槽液中加入铈盐和镧盐,发现氧化膜的硬度增强、阻挡层厚度增加、耐蚀性能提高。可能是由于稀土金属离子具有较高的价态和较正的标准氧化还原电位,在阳极氧化过程中对某些中间反应起到类似于催化剂的作用。
经稀土盐封闭的铝及其合金阳极氧化膜可认为由三部分构成:封闭层、多孔层和阻挡层。其中封闭层和多孔层的孔洞内部的填充物成分相同,都主要由封闭产物即含结晶水的氧化铝及稀土氢氧化物或氧化物组成,而多孔层的孔壁和阻挡层则主要由致密的Al2O3组成。
总之,稀土盐封闭工艺的发展经历了漫长而复杂的历程。在单一稀土盐溶液封闭的基础上开发了混合稀土盐封闭,从仅有化学反应的浸泡处理发展到有电化学反应的阴极直流电解沉积、外加脉冲电压沉积、交流电沉积,再发展到浸泡与电化学处理相结合的铈-钼盐封闭处理。其中,封闭效果优于传统封闭,能耗低,最有发展前途的应该是外加脉冲电压沉积和浸泡-电化学处理工艺。然而外加脉冲电压封闭和浸泡-电化学处理的工艺较复杂,过程不易控制,耐高温性能较差,因此要步入工业化生产,仍需进一步的研究。
2 溶胶封闭
溶胶封闭是利用物理吸附作用使溶胶胶粒渗入到孔隙中,并覆盖住微孔在阳极氧化膜表面形成一层溶胶膜,溶胶膜经凝胶化及干燥处理后得到干凝胶膜,最后在一定的温度下烧结即得到溶胶封闭膜。目前用于阳极氧化膜封闭的溶胶有二氧化硅溶胶和铝溶胶两种。
溶胶的涂覆方式有:浸涂、喷雾涂、流动涂、自旋涂、辊涂等。其中,应用最广泛的是浸涂中的浸渍-提拉法。浸渍-提拉法就是把氧化膜浸入溶胶中,在一定的温度和气氛中以一定的提拉速度提拉。溶胶的黏度越大,提拉速度越快,氧化膜表面形成的溶胶膜越厚,而溶胶膜太厚或太薄都会直接影响封闭的质量,因此须严格控制溶胶的黏度和提拉速度。大型工件的提拉速度不易控制,故溶胶封闭不适用于大型铝及铝合金工件。
2.1 二氧化硅(SiO2)溶胶封闭
SiO2溶胶是纳米二氧化硅微粒在水中或有机溶剂中均匀扩散形成的胶体溶液。SiO2溶剂的颗粒均匀、比表面积大、成型和成膜力强,已被广泛用于化学机械抛光、催化剂载体、耐火陶瓷材料、复合涂料等工业领域。
溶胶-凝胶法是常用的制备SiO2溶胶的方法,根据机理的不同,又可细分为有机醇盐水解法,无机盐水解法、熔融-淬冷法和离子交换法四种。其中,最常用的是有机醇盐水解法,也即将正硅酸乙脂、无水乙醇和蒸馏水按一定的体积比4:3:1.28混合,加入适量的催化剂盐酸,用磁力搅拌机搅拌2h,最终得到均匀的、无色透明的SiO2溶胶。为提高SiO2溶胶的稳定性并降低SiO2溶胶的黏度,需向其中加入十二烷基苯磺酸钠作为表面活性剂。
Kamada等在SiO2溶胶水溶液中用溶胶-凝胶电泳沉积技术在铝基阳极氧化膜的纳米孔隙中沉积了SiO2纳米颗粒,结果发现:无需施加电场,悬浮液中的SiO2颗粒也能进入膜孔,SiO2溶胶应该能对铝基阳极氧化膜起到封闭作用。国内许多学者开展了SiO2溶胶对铝基阳极氧化膜的封闭研究。李澄等将铝阳极氧化膜浸入SiO2溶胶中用浸渍提拉法对氧化膜进行封闭,通过控制反应条件可改变溶胶中胶粒的尺寸。当SiO2溶胶颗粒与氧化膜骨架尺寸匹配时可获得很好的封闭效果,并指出SiO2溶胶是通过填充膜孔的方式来实现封闭的。
张金涛等采用浸渍提拉法将γ-环氧丙氧丙基三甲氧基硅烷(GPTMS)/正硅酸乙酯(TEOS)杂化溶胶(简称硅烷杂化溶胶)用于LY12铝合金阳极氧化膜的封闭。硅烷杂化膜是一种以SiO2无机网络为基础的有机-无机杂化材料,故该溶胶封闭可认为是SiO2溶胶封闭的延伸和发展。张金涛等发现用硅烷杂化溶胶对LY12铝阳极氧化膜进行封闭处理时,如向溶胶中加入Ce(NO3)3作为缓蚀剂,可增强氧化膜的致密性,提高氧化膜的长效耐蚀性。另缓蚀剂Ce(NO3)3的添加方式也会影响铝合金基体的耐蚀长效性,将LY12铝阳极氧化膜先浸入Ce(NO3)3乙醇溶液中,取出吹干后再浸入硅烷杂化溶胶中封闭,得到的阳极氧化膜的耐蚀长效性远高于直接将其浸入掺杂Ce(NO3)3的硅烷杂化溶胶中封闭。原因可能是铈盐的缓蚀作用和硅烷杂化溶胶的封闭作用有协同效应,有效阻碍了O2在溶液与金属基体界面上自由扩散和迁移,腐蚀的动力被有效控制,使腐蚀过程减慢。
2.2 铝溶胶封闭
铝溶胶又称勃姆石溶胶、氧化铝溶胶或氢氧化铝(AlOOH)溶胶,是带正电荷的水合氧化铝胶粒分散在水中的胶体溶液。广泛用于石油化工表面活性剂、硅酸铝纤维和陶瓷等耐高温材料的成型粘结剂、纺织物及纤维品处理的成膜剂和抗静电剂等。铝溶胶常用溶胶-凝胶法制备,根据制备原料的不同,铝溶胶的制备方法可分为有机盐原料法、无机盐原料法和粉体分散法三种。分别介绍如下:
(1)有机盐原料法一般用异丙醇为原料制备铝溶胶,优化工艺为将异丙醇铝和去离子水以100:1的摩尔比在80℃下混合,剧烈搅拌2h,再加入HNO3调节pH值至4.6,最后在84℃下回流陈化24 h。有机盐原料法可制得的铝溶胶纯度高、粒度分布均匀,但也有一些缺点。如原料价格昂贵,原料易燃、有毒,制备过程复杂,不易控制,不易保存。
(2)无机盐原料法一般用硝酸铝为原料制备铝溶胶,优化工艺为将氨水滴加到Al(NO3)3溶液中调节pH值至4.0,在80-90℃下剧烈搅拌24 h。国内谢五喜等人通过单因素分析的实验研究,找到了无机盐原料法制备稳定透明的铝溶胶的优化工艺参数:水解温度85℃,n (H+)/n (Al3+) =0.14:1,n(H2O)/n (Al3+)=140:1,蒸发时间3h,老化温度90℃,老化时间4h。无机盐原料法原料价格低廉、过程简单易控,但制得的铝溶胶纯度相对较低,还需加入添加剂以保持稳定性和增大胶粒的比表面积。
(3)粉体分散法是将拟薄水铝石粉(SB粉)或氧化铝粉与蒸馏水混合成一定浓度的悬浊液,加热到85℃后激烈搅拌,再加入一定量的HNO3,再激烈搅拌和85℃回流一定时间。粉体分散法原料价格便宜,过程简单易控,易于储存,但制得的铝溶胶纯度也较低。因为SB粉中常含杂质,而SB粉的纯度直接影响铝溶胶的纯度。
Zemanova M等首先将铝溶胶用于铝合金阳极氧化膜的封闭,发现溶胶封闭膜的耐蚀性可与热水封闭的相当。东北大学的周琦等对异丙醇铝溶胶和硝酸铝溶胶封闭铝合金阳极氧化膜的工艺进行细致的研究,得出:(1)异丙醇铝溶胶(pH=4.6)封闭铝合金阳极氧化膜的优化参数为浸渍时间:40 min,溶胶浓度:0.37 mol/L,烘干温度:80℃,烘干时间:6 h;(2)硝酸铝直接水解得到的溶胶(pH=4)封闭铝合金阳极氧化膜的优化方案为浸渍时间:50 min,溶胶浓度:0.60mol/L,烘干温度:60℃,烘干时间:2 h。将这两种较优方案的封闭效果相比,发现异丙醇铝溶胶的封闭膜性能略优于硝酸铝溶胶的封闭膜。
周琦等还将铝溶胶封闭的氧化膜膜的耐蚀性与重铬酸钠封闭、硝酸铈溶液封闭、Ni2+—F-—Zn2+盐封闭、Ni2+—Co2+盐高温水解封闭和Co2+—三乙醇胺常温封闭的氧化膜的耐蚀性进行对比,发现铝溶胶封孔膜各方面的性能都较好,具有继续开发研究的前景。
总之,溶胶封闭剂以SiO2和Al2O3为主体向着多元化方向发展,使铝阳极氧化膜的硬度、绝缘性、耐高温性、耐磨性等都得到了提高。在溶胶的制备方面还存在一些问题,需寻求一种新的制备工艺,能制备出原料价格低廉、过程简单易控、纯度高、稳定性好且黏度低的溶胶。
3 微波水合封闭
高温水蒸汽封闭虽然在工业上获得了广泛应用,但能耗高、封闭时间长、工作环境差。为克服这些缺点,开发了冷封闭,但冷封闭后的氧化膜质量却不如高温水蒸汽封闭。因此,需开发一种新的封闭方法既能保留高温水蒸汽封闭的质量又能大幅度降低能耗、缩短处理时间并改善劳动条件。热封闭能耗之所以高,就是因为消耗的热不仅仅用于加热氧化膜,而是大多数热用于把整个铝材或铝制品都加热到处理温度。如果只加热湿的氧化膜层而不加热铝制品就可将高温水蒸汽封闭的能耗降低到冷封闭的能耗值。
Pozzoli开发了微波水合封闭法,即采用微波对氧化膜层及氧化膜层上的水膜进行加热,发生水合反应,从而完成对阳极氧化膜的封闭。微波水合封闭的机理与高温水溶液封闭相同。用该方法对铝及铝合金阳极氧化膜封闭时,微波只需要加热湿的铝合金阳极氧化膜和膜前0.010mm厚的水膜即可,因此,在整个封闭过程中氧化膜表面必须始终保持一层薄薄的水膜,否则氧化膜会反射微波,达不到水合封孔的目的。该封闭工艺可大大节约能量,将封闭时间缩短至0.5~0.8
min/μm,封闭膜的耐蚀性可达到ISO·3210的要求。但缺点是被封闭的工件形状不能太复杂,否则微波对材料的凹陷曲折面的辐射量小,达不到封孔质量要求。这严重限制了其应用范围,要想实现工业化大生产,还需要进行更深入的研究,尽量克服它的缺点。国内学者对微波水合封闭关注的很少,以后应加强这方面的研究。
min/μm,封闭膜的耐蚀性可达到ISO·3210的要求。但缺点是被封闭的工件形状不能太复杂,否则微波对材料的凹陷曲折面的辐射量小,达不到封孔质量要求。这严重限制了其应用范围,要想实现工业化大生产,还需要进行更深入的研究,尽量克服它的缺点。国内学者对微波水合封闭关注的很少,以后应加强这方面的研究。
4 3种绿色封闭工艺的优缺点
稀土盐封闭采用化学或电化学方法将稀土元素引入到氧化膜微孔内,主要通过稀土金属离子与溶液中的OH-发生反应生成稀土的氢氧化物沉淀来填充和覆盖微孔的,并在氧化膜上形成一层含稀土的转化膜;溶胶法主要利用物理吸附作用,将适当尺寸的溶胶胶粒渗入并覆盖氧化膜的微孔,并在氧化膜上形成一层溶胶层;微波水合封闭保留传统高温水溶液封闭的封闭机理,克服了高温水溶液封闭的缺点,改变了加热形式和水分子与氧化膜的接触方式。这3种绿色封闭工艺的优缺点如表1所示。
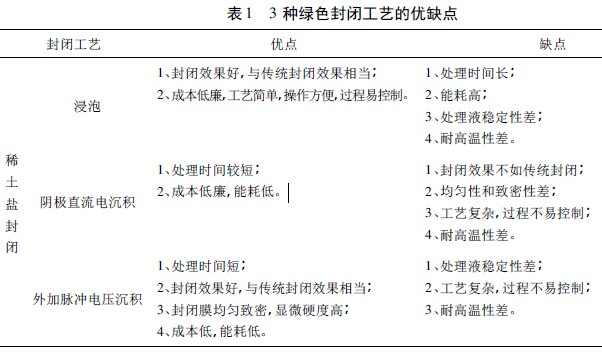
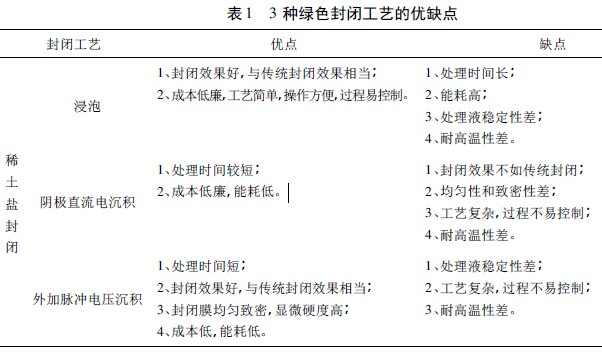
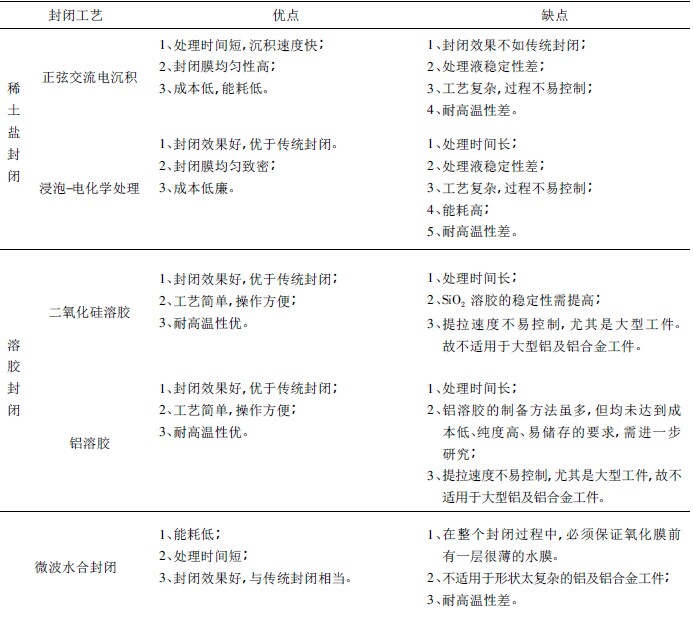
稀土盐封闭后的铝及铝合金阳极氧化膜的耐高温性能较差,适合常温工况;与之相反,溶胶封闭后的铝及铝合金阳极氧化膜的耐高温性能很好,更适合高温工况。溶胶封闭不适用于大型工件;微波水合封闭不适用于形状复杂的工件。这些缺点严重阻碍溶胶封闭和微波水合封闭工艺的应用和发展,还需要更深入的研究来克服。
5 总结与展望
本文概述了稀土盐封闭、溶胶封闭和微波水合封闭这3种绿色封闭工艺的发展、机理及现状,并将其优缺点进行了对比。结果发现:稀土盐封闭适合常温工况、溶胶封闭更适合高温工况;稀土盐封闭中效果优于传统封闭且能耗低、最有发展前途的外加脉冲电压沉积和浸泡-电化学处理工艺工艺复杂,过程不易控制;溶胶封闭不适用于大型工件,微波水合封闭不适用于形状复杂的工件。每种封闭工艺均需继续改进,才能满足工业化生产的需要。
目前国内关于铝及铝合金阳极氧化膜的新型绿色封闭方法的研究主要集中在新型冷封闭剂和稀土盐封闭上,对溶胶封闭和微波水合封闭的研究较少,因此,需要有更多学者关注并参与这些方面的研究。最近又出现了二次封闭工艺,如铝合金阳极氧化膜经稀土盐封闭后继续进行沸纯水或高温水蒸汽封闭;在单层稀土转化膜上再沉积一层其它稀土转化膜;铝合金阳极氧化膜经SiO2溶胶封闭后继续用有机树脂封闭等。铝及其合金阳极氧化膜的新型绿色封闭处理方法呈现多样化发展趋势。随着研究方法的增多,研究手段的加强,一定会有更多高效、价格低廉、且更适合工业化生产的新型绿色封闭技术出现。
上一篇: 铝及铝合金阳极氧化膜的封孔工艺研究进展
下一篇: 铝阳极氧化膜不同封孔方法的耐腐蚀性能研究