铝及铝合金非铬电化学抛光工艺的研究
铝及铝合金非铬电化学抛光工艺的研究
安成强 郝建军
(沈阳工业学院,辽宁沈阳110045)
(沈阳工业学院,辽宁沈阳110045)
摘要:对铝及铝合金的电化学抛光进行了研究,针对传统方法,研制出了一种组合添加剂(AH-1)代替铬酸。经过实验测定,采用此方法,加入少量组合添加剂获得的抛光表面状态、光亮度等性能指标均达到或优于铬酸抛光,并且此方法消除了铬的污染,具有很好的应用前景。
1 前 言
传统的铝件电化学抛光是采用磷酸—硫酸—铬酸法。此法抛光效果好,但含有毒性很大的铬酸,后续存在含铬污水问题,给实际生产应用带来一定的困难。从工艺上去除铬酸,消除污染,是铝及铝合金电化学抛光的发展方向。
近年来,国内外提出了一些非铬电化学抛光工艺,主要是以磷酸和硫酸为基液,加入甘油、乙二醇或聚合物等缓蚀剂,据称质量能达到传统铬酸抛光效果。但在这些配方中,甘油、乙二醇等含量偏高,有的达到20%~40%。抛光液粘度大,水洗性不好,并需要较高的电流密度,成本高,使其在生产应用中受到限制。因此,针对国内外铝合金无铬电化学抛光的研究现状和工业应用的工艺要求,有必要对非铬电化学抛光工艺进行更深入的研究和探讨,使其应用更加广泛。通过实验研究,我们成功的研制出了一种非铬电化学抛光液,其性能达到和超过了含铬电化学抛光液的性能,具有较好的应用前景。
2 试验条件及试验方法
2.1 材料及试样制备
试件材料:L2; LFl;LF21; LYl2。试件尺寸:60mm×25mm×1mm。
2.2 腐蚀失重试验
1 前 言
传统的铝件电化学抛光是采用磷酸—硫酸—铬酸法。此法抛光效果好,但含有毒性很大的铬酸,后续存在含铬污水问题,给实际生产应用带来一定的困难。从工艺上去除铬酸,消除污染,是铝及铝合金电化学抛光的发展方向。
近年来,国内外提出了一些非铬电化学抛光工艺,主要是以磷酸和硫酸为基液,加入甘油、乙二醇或聚合物等缓蚀剂,据称质量能达到传统铬酸抛光效果。但在这些配方中,甘油、乙二醇等含量偏高,有的达到20%~40%。抛光液粘度大,水洗性不好,并需要较高的电流密度,成本高,使其在生产应用中受到限制。因此,针对国内外铝合金无铬电化学抛光的研究现状和工业应用的工艺要求,有必要对非铬电化学抛光工艺进行更深入的研究和探讨,使其应用更加广泛。通过实验研究,我们成功的研制出了一种非铬电化学抛光液,其性能达到和超过了含铬电化学抛光液的性能,具有较好的应用前景。
2 试验条件及试验方法
2.1 材料及试样制备
试件材料:L2; LFl;LF21; LYl2。试件尺寸:60mm×25mm×1mm。
2.2 腐蚀失重试验
将试样在抛光前后用分析天平称其质量,然后按照抛光前后试样的质量差除以试样面积和抛光时间计算出腐蚀速度。
2.3 抛光表面光亮度测定
为评定抛光液的抛光效果,测定了抛光件的镜面反射比。在试验中将含铬电抛光液中抛光试样作为标准试样,其光亮度定为100%,用目测法将其他电抛光抛出的试样与之比较,光亮度优于标准试样的光亮度> 100%,反之则<100%。
3 结果与讨论
3.1 基液的选择
实验材料为LF2,将含铬电化学抛光液中的铬酸除去后,磷酸和硫酸按3种不同配比7:3;6:4;5:5;进行实验,温度为85℃,时间为3 min,电流密度为22 A/ dm2。
通过实验得出磷酸和硫酸为7:3时抛光整平性、光亮度较好。基液中一定比例的硫酸存在,能提高抛光液的导电性和降低槽电压,但硫酸过多会增强溶液的腐蚀性,对抛光不利。根据试验确定基液成分比例为磷酸:硫酸=7:3,然后在此基础上筛选添加剂。
3.2 添加剂的筛选及对抛光质量的影响
试验中发现,只使用基液进行抛光时抛光质量不如含铬抛光液,因此必须寻找与铬酸作用相同而又无毒的药品来代替铬酸。经大量试验,确定了铝及铝合金电化学抛光使用的组合添加剂为AH-1,此添加剂对铝有良好的缓蚀作用和光亮作用。其抛光的光亮度和整平性均达到甚至超过含铬电抛光,消除了铬的污染。与目前提出的含有甘油或乙二醇的无铬电化学抛光相比,本研究中的添加剂用量少,而且抛光时电流密度小,溶液的导电性也好,有利于降低成本。
3种配方的比较见表1(试验条件:材料为LF2,温度为85℃,电流密度为22 A/dm2,时间3min)。添加剂对抛光质量的影响很大(试验条件:材料为LF2,温度为85℃,电流密度为22 A/dm2,时间3 min),见表2。
表1 不同抛光溶液抛光效果对比
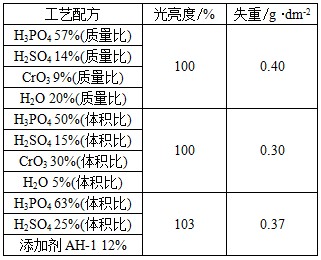
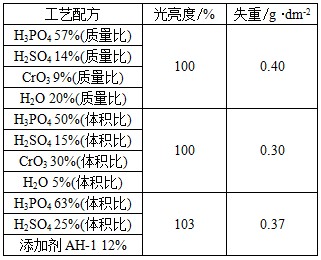
表2 添加剂含量与抛光效果的关系
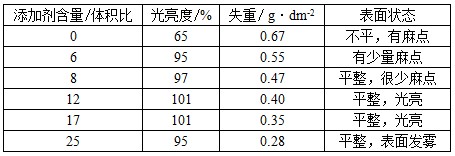
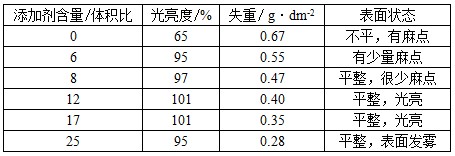
从实验结果看出,只有当添加剂含量达到一定时,才能得到较好的抛光效果。添加剂过多或过少均影响抛光质量。当添加剂含量较少时,虽然也能得到光亮的表面,但断电后腐蚀严重,抛光后要立即清洗干净,否则表面易出现腐蚀花斑,故影响抛光质量。随着添加剂含量增加,抛光性能随之提高,腐蚀速度下降。但添加剂含量过高,会影响抛光效果,降低溶液的导电性,使抛光速度降低。添加剂含量一般控制在体积比为10%~18%为宜,最佳含量为12%。
3.3 工艺条件对抛光质量的影响
(1)电流密度的影响
控制抛光的工艺条件为:温度80~85℃,时间为3min,在不同的电流密度下,观察电流密度对LF2抛光质量的影响(见表3)。从试验结果得出,在一定条件下,随着电流密度的增加,腐蚀速度增大和抛光质量提高。电流密度过低,抛光质量下降。如果提高电流密度,有利于节省时间和提高抛光质量。若电流密度过高,在阳极上析出氧气,且产生大量的热量来不及扩散,使电极表面的温度迅速升高,导致金属表面产生麻点,影响表面光亮度。适宜的电流密度为12~25 A/dm2。
表3 电流密度与抛光质量的关系
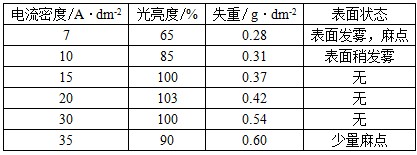
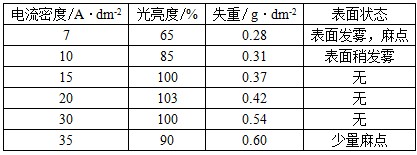
(2)温度的影响
在电流密度为15 A/dm2,抛光时间为3 min的条件下,温度对抛光质量的影响见表4。
表4 温度对抛光质量的影响
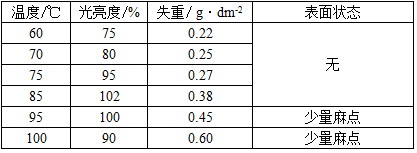
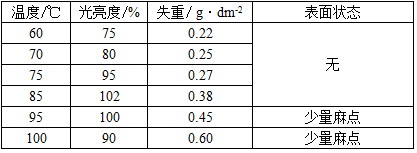
从表4可以看出,温度低时,电解液的粘度较高,铝的溶解慢,抛光效果不好;电解液温度升高,则其粘度降低,金属溶解速度加快,生产效率提高。但若温度过高,易使金属表面产生腐蚀麻点,而降低抛光质量。所以应将温度控制在75~90℃时,才能得到良好的抛光质量。
(3)抛光时间的影响
抛光时间的长短取决于铝的纯度、表面状态、抛光液的成分、温度、阳极电流密度及表面要求的光亮度等因素。在80~85℃时电流密度为15A/ dm2条件下,对LF2材料进行电化学抛光,其抛光时间与抛光质量的关系见表5。
表5 时间对抛光质量的影响
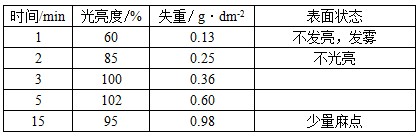
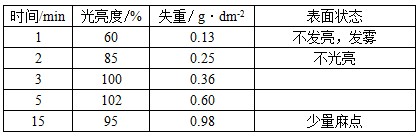
从表5中可看出,抛光时间短时,铝溶解量少,抛光质量差。在适宜的时间范围内,抛光质量与其成正比。一般抛光时间与温度和电流密度均成反比关系,当抛光温度或阳极电流密度较高时,则抛光时间应短,反之则长。
(4)搅拌的影响
搅拌可使聚集在铝表面的离子及时扩散到溶液中去,同时又保证了新的电解液连续不断地供应到阳极表面;搅拌可使电解液的温差减小,保持温度均匀,又可以防止阳极过热:同时搅拌可使阳极表面上的气泡加速脱离出来,避免试样表面生成斑点或条纹现象,从而保证了抛光质量。
综上所述,溶液温度、电流密度、时间及搅拌等条件对抛光质量均有很大的影响,适宜的工艺条件可以取得较好的抛光效果。实验中采用的工艺条件为:电流密度15~25 A/dm2;温度75~90℃;时间3~12 min。
3.4 材料的适应性及溶液寿命测定
对不同材料的铝件进行平行实验表明,此抛光液对纯铝、LF2、LF21、LY12均可取得较好的抛光效果,对材料的适应性较强。
在温度80~85℃,电流密度15~25 A/dm2,抛光时间3~12 min的条件下,测定该溶液的抛光寿命。结果表明,在此条件下抛光液抛光270m2/L的试样后,抛光质量开始下降,此前调整溶液可保持良好的抛光效果。
4 结论
通过实验研究,得到的铝及铝合金的非铬酸电化学抛光的工艺规范为:
磷酸(p=1.71) 62%(体积比)
硫酸(p=1.84) 26%(体积比)
组合添加剂(AH-1) 12%(体积比)
温度 75~90℃
时间 3~12 min
该工艺与含铬电化学抛光工艺相比,消除了铬的污染,得到的抛光效果达到甚至超过含铬电化学抛光。与国内现行的非铬电化学抛光工艺相比,添加剂用量少,电流密度低,导电性能好,成本低,对材料适应性好,溶液稳定,该工艺是具有良好的推广价值。
上一篇: 铝及铝合金的表面抛光
下一篇: 铝及铝合金高亮度无黄烟化学抛光工艺