铝合金碱性抛光液及其工艺条件
铝合金碱性抛光液及其工艺条件
诸荣孙
(安徽工业大学化工系,安徽 马鞍山243002)
摘要:由于铝合金在碱性溶液中腐蚀速度极大,致使抛光时间不能过长;此外,由于碱性溶液抛光后表面的光亮度不大,所以降低铝的腐蚀速度、提高抛光光亮度是碱性化学抛光的关键。作者对铝合金的几种新型碱性化学抛光液
及其工艺条件进行了研究。试验结果表明:添加由硫脲(或钼酸铵或六次甲基四胺)、硅酸钠、十二烷基硫酸钠构成的复合缓蚀剂能大大提高铝合金抛光质量,同时可抑制碱雾的产生。铝合金碱性抛光液的较佳配方与工艺条件为:NaOH 300 g/L,NaNO3 250 g/L,硫脲20 g/L,硅酸钠10 g/L,十二烷基硫酸钠1.5~1.8 g/L,温度60~70℃,抛光时间80~100 s。
及其工艺条件进行了研究。试验结果表明:添加由硫脲(或钼酸铵或六次甲基四胺)、硅酸钠、十二烷基硫酸钠构成的复合缓蚀剂能大大提高铝合金抛光质量,同时可抑制碱雾的产生。铝合金碱性抛光液的较佳配方与工艺条件为:NaOH 300 g/L,NaNO3 250 g/L,硫脲20 g/L,硅酸钠10 g/L,十二烷基硫酸钠1.5~1.8 g/L,温度60~70℃,抛光时间80~100 s。
前言
铝材酸性抛光光亮度大,腐蚀速度较慢,抛光效果好,但成本高,且在抛光过程中有大量的黄烟逸出,污染环境.因此,人们试图开发研究铝及铝合金的无污染化学抛光工艺,其中碱性抛光有其独特优点:抛光液成本低,对槽体设备的腐蚀小,设备造价低,特别是废水处理简单。但由于铝型材在碱性溶液中腐蚀速度极大,致使抛光时间不能过长(往往只有几十秒),否则产生麻点或严重失重,不适合大型铝型材的工业抛光生产;其次,碱性溶液抛光后表面的光亮度不大,抛光质量亦低于酸性抛光后的质量,因而其应用受到限制。所以,降低铝的腐蚀速度,提高抛光光亮度是碱性化学抛光的关键。为了找出抛光质量较好、腐蚀不太严重、适应多种材料的碱性抛光液及其较佳工艺条件,作者对此进行了研究。
1 试验部分
试样为6063铝片,尺寸规格为60 mm×25 mm×1 mm,试验药品为NaOH,NaNO2,NaNO3,Na3PO4,NaF,SnC12和硫脲、硅酸钠、六次甲基四胺、钼酸铵、十二烷基硫酸钠(均为分析纯)。实验仪器为KGZ-IA型光泽仪、GT2A分析天平及可调恒温水浴箱。
试样抛光的光泽度采用光泽仪测定。金属在抛光液中的溶解量(失重率)以试样在抛光前后的质量差除以表面积计算。
1 试验部分
试样为6063铝片,尺寸规格为60 mm×25 mm×1 mm,试验药品为NaOH,NaNO2,NaNO3,Na3PO4,NaF,SnC12和硫脲、硅酸钠、六次甲基四胺、钼酸铵、十二烷基硫酸钠(均为分析纯)。实验仪器为KGZ-IA型光泽仪、GT2A分析天平及可调恒温水浴箱。
试样抛光的光泽度采用光泽仪测定。金属在抛光液中的溶解量(失重率)以试样在抛光前后的质量差除以表面积计算。
通过对比前人的工作,采用单一或复合缓蚀剂来降低铝合金在碱性化学抛光液中的腐蚀速度,并通过添加表面活性剂在抛光液表面形成泡沫来抑制碱雾的逸出。这种由缓蚀剂、表面活性剂组成的复合添加剂还具有润湿、整平增光的作用。试验采用的骨干配方与工艺条件见表1,在其他成分配比与工艺条件不变的条件下。将硅酸钠质量浓度保持在10 g/L,添加其他缓蚀剂进行试验。
表1 实验配方与操作条件


2 试验结果与讨论
2.1 缓蚀剂类型的影响
研究几种不同类型的缓蚀剂的碱性抛光液对铝合金抛光效果的影响,其结果见表2和表3。
表2 几种缓蚀剂抛光液所抛光出的铝片光亮度
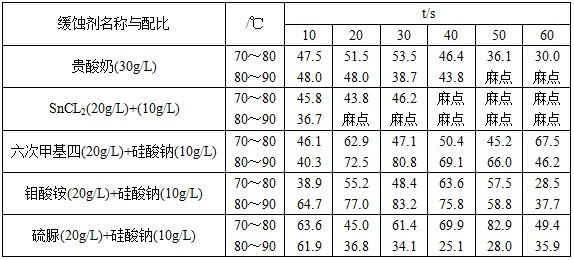
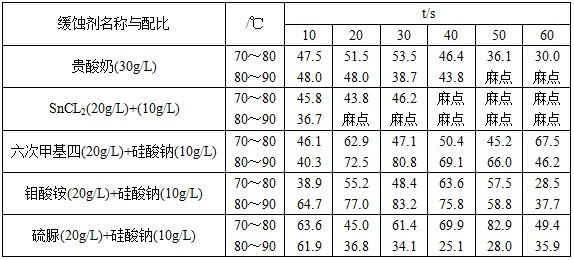
表3 铝片在3种缓蚀剂抛光液中的失重
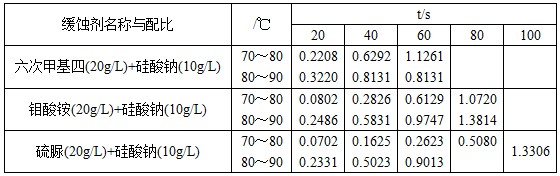
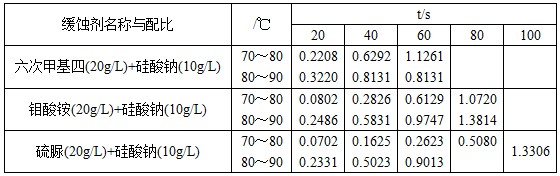
由表2和表3可见,以硅酸钠( 30g/L)为缓蚀剂的抛光液对铝片抛光的光泽度随着时间延长而减弱,当时间超过40 s时,腐蚀严重;其次,温度升高,硅酸钠的抛光效果变得较差,时间延长,效果更差,产生较多的麻点。
以SnCl2( 20 g/L)和硅酸钠(10 g/L)为复合缓蚀剂的抛光液对铝片抛光光泽度较小。当温度为70-90℃,抛光时间超过40 s时,发生严重的点腐蚀,在表面形成大量的小凹斑。温度越高产生凹斑的速度越快。其原因可能是试样表面的凹处没有钝化膜,即没有稠性膜形成,铝很快溶解,因而产生了大量的麻点。
以六次甲基四胺( 20 g/L)和硅酸钠(10 g/L)为缓蚀剂的抛光液对铝片抛光的光泽度较大,但抛光时间不能过长,否则发生过腐蚀;六次甲基四胺缓蚀剂抛光的最佳温度范围是80~90℃,在该温度下最适宜的抛光时间是20~50 s。从表3可以看出,以六次甲基四胺为缓蚀剂的抛光液对铝合金的抛光的失重,在70~80℃及80~90℃时,其失重率都很大,致使铝大量损耗。
以钼酸铵(20 g/L)和硅酸钠(10 g/L)为缓蚀剂的抛光液在温度70~80℃时对铝片抛光的光泽度,当抛光时间为20~50 s时较大,此后腐蚀加重;在温度为80~90℃范围抛光效果比在70~80℃的要好,说明温度升高,有利于铝材的化学抛光。从表3可知,该抛光液抛光的铝材,在70~80℃时失重较小;而在80~90℃时失重大。因此,用该抛光液抛光铝材时,宜采用工作温度为80~90℃,时间为20~50 s。
以硫脲(20 g/L)和硅酸钠(10 g/L)为缓蚀剂的抛光液对铝片抛光效果较好。在70~80℃时的抛光效果比80~90℃的要好,在10~60 s内能得到较大的抛光光泽度;而在80~90℃内抛光效果不太好,随时间延长效果更差。造成这种反差的原因可能是,低温时铝合金的表面在抛光时,硫脲、硅酸钠、表面活性剂在试样表面形成了一薄层稠性的粘膜,以保护凹处,避免溶解过快;而在温度升高时,薄层稠性的粘膜溶解,所以,在80~90℃时抛光效果普遍不好,从表3可知,在70~80℃时铝材失重很小,在80~90℃时其失重又较为严重,铝材的损耗大。因此,以硫脲为缓蚀剂的抛光液对铝材进行抛光时温度应控制在80℃以下。
2.2 温度与碱浓度的影响
2.2.1 温度的影响
确定了硫脲作为抛光较佳的缓蚀剂后,进一步考察温度对其抛光效果的影响,结果见表4。
表4 不同温度时试样在硫脲(20g/L)+硅酸钠(10g/L)的抛光液中的抛光效果(光泽单位/l0)


由表4可以看出,硫脲在60~70℃时,抛光效果很好,且抛光效果稳定,能达到较长的抛光时间80~100 s。这说明温度降低,抛光速度(即铝的溶解速度)减慢;另外低温条件下铝合金的表面在抛光时,形成了一薄层稠性的粘膜或钝化膜,保护凹处,避免溶解过快,而表面微观凸处的溶解速度显著大于凹处的溶解速度,降低了表面的粗糙度,使铝合金表面趋于平整而光亮。
2.2.2 碱浓度的影响
表5列出了不同碱度下试样在硫脲( 20 g/L)+硅酸钠(10 g/L)抛光液中的抛光效果(反应温度为60~70℃)。
表5 不同碱度下试样在硫脲(20g/L)+硅酸钠(10g/L)的抛光液中的抛光效果(光泽单位/l0)


从表5可知,NaOH的质量浓度为300 g/L比较合适,若过小则达不到所要求的抛光效果,若过大则容易发生过腐蚀,造成失重严重,铝片局部产生麻点,而当质量浓度控制在300 g/L时抛光效果最佳,抛光时间足够长。因此,选择NaOH的质量浓度为300 g/L。
2.2.3 较佳的抛光工艺条件
实验表明,较佳的碱性抛光溶液组成及工艺条件为:ρ(NaOH) 300g/L;ρ(NaNO3) 250g/L;ρ(硫脲)20g/L;ρ(硅酸钠) 10 g/L;ρ(十二烷基硫酸钠)1.5~1.8 g/L;温度60~70 ℃;时间80~100 s。
3 结 语
以10 g/L硅酸钠、20 g/L硫脲、1.5~1.8 g/L十二烷基硫酸钠为复合缓蚀剂的碱性配方简单,成本低,它在抛光50 s时还能使抛光光泽度达到80光泽单位以上,在70 s以前的失重最小;同时,废水处理简单,适宜于小型铝合金工件抛光。但其抛光速度仍然太快,只需1 min左右就完成整个抛光过程,这给大型铝型材的抛光带来操作上的难度,因而还需进一步寻找更合适的复合缓蚀剂来降低抛光速度。
上一篇: 铝合金化学抛光流痕的成因及控制
下一篇: 铝合金无铬电化学抛光研究