铝合金化学抛光流痕的成因及控制
铝合金化学抛光流痕的成因及控制
何宝林 强世伟 孙春桃 洪盛志
(中南民族学院化学系 武汉430074)
(中南民族学院化学系 武汉430074)
摘要:研究了铝合金化学抛光产生流痕的各种因素及流痕的主要化学成分,并认为转移时间是产生流痕的主要因素。未加入抛光添加剂A、B时,欲将流痕控制在0~1级范围内时,转移时间只允许控制在30s秒内;加入抛光添加剂A、B后,转移时间可以延长到70s,说明添加剂A、B对流痕有较好的抑制作用。
引言
迄今为止,用于铝及其合金化学抛光最广泛的体系当推硫酸—磷酸—硝酸、铜及添加剂的混合溶液(下文简称三酸体系)。这种体系以其维护容易,三酸比例、抛光温度、水含量控制范围大,抛光时间适中,产品量度高等优点而以不同的商业名称广泛地用于国内外生产线中。但铝及其合金在上述的三酸体系中抛光好后,从抛光槽转移到水洗槽所用的时间超过某一数值,就会在试样的表面上留下一道道明暗交替的横向条纹流痕(斑马纹)。若抛光温度过高,流痕会变成明暗不同的花斑,严重地影响产品的外观质量。目前国内外鲜见有关流痕成因及防止的报道。因此,进行三酸体系中铝及其合金化学抛光的流痕成因及控制的研究具有一定的理论价值和实际意义。
1 实验方法
(1)采用LD31,铝合金100cm x12cm扁管作试样。
(2)模仿大工业生产条件,化学抛光时间控制在2~5 min内,抛光温度80~90℃,将硝酸(d=1.50 g/cm3)体积比固定为3%、铜固定为0.05 g/L;改变磷酸(d=1.75 g/cm3)与硫酸(d=1.84 g/cm3)的体积比,试样抛光完后,迅速转移至水洗槽中冲洗以中止抛光反应的继续进行。将试样放在1:1硝酸中浸泡20~30 s以除去表面上沉积的少量铜,再将试样用水漂洗干净,风干。
(3)用目视法将试样表面流痕按严重程度分成0~4共5个等级,其中4级流痕最严重,整个表面呈花斑状。0级完全没有流痕,1级只有轻微可见流痕,并认为l级以下的流痕是用户可以接受的。流痕等级与目视外观见表1。
(4)对有流痕的地方采用XPS( X-ray PhotoelectronSpectroscopy)法、EXM(Energy dispersive X-rayMicro-analysis)法分析,以确定流痕的化学成分。
(5)向原有的三酸体系中加入抛光添加剂A、B,考察其对流痕的抑制作用。
表1 流痕目视外观分级
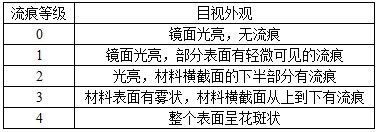
1 实验方法
(1)采用LD31,铝合金100cm x12cm扁管作试样。
(2)模仿大工业生产条件,化学抛光时间控制在2~5 min内,抛光温度80~90℃,将硝酸(d=1.50 g/cm3)体积比固定为3%、铜固定为0.05 g/L;改变磷酸(d=1.75 g/cm3)与硫酸(d=1.84 g/cm3)的体积比,试样抛光完后,迅速转移至水洗槽中冲洗以中止抛光反应的继续进行。将试样放在1:1硝酸中浸泡20~30 s以除去表面上沉积的少量铜,再将试样用水漂洗干净,风干。
(3)用目视法将试样表面流痕按严重程度分成0~4共5个等级,其中4级流痕最严重,整个表面呈花斑状。0级完全没有流痕,1级只有轻微可见流痕,并认为l级以下的流痕是用户可以接受的。流痕等级与目视外观见表1。
(4)对有流痕的地方采用XPS( X-ray PhotoelectronSpectroscopy)法、EXM(Energy dispersive X-rayMicro-analysis)法分析,以确定流痕的化学成分。
(5)向原有的三酸体系中加入抛光添加剂A、B,考察其对流痕的抑制作用。
表1 流痕目视外观分级
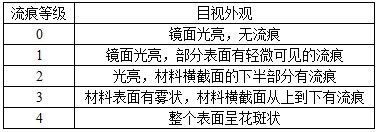
注:观察者与试样的距离为1m,入射光与试样呈45°夹角,与观察者呈120°夹角。
2 结果与讨论
通过实验,整个化学抛光过程中的各种因素对流痕作用力的大小依次是(从大至小):转移时间,抛光添加剂浓度,磷酸与硫酸的体积比及抛光温度。
2.1 转移时间的影响
一般说来,抛光温度85℃时试样从抛光槽提出后其表面上仍在进行剧烈反应,并伴有黄烟和白色的泡沫产生。泡沫由于重力的作用向下滑落,有些地方滑落得相对快些,有些地方滑落得相对慢些。水洗后发现:泡沫滑落快的地方光亮些,滑落慢的地方暗些,这样就形成了明暗交替的横向条纹流痕。将有流痕的试样放在1:1或更浓的硝酸溶液中浸泡也不能使之溶解。
实验表明:试样抛光好后,从抛光槽转移至水洗槽所花的时间越长流痕就越严重,转移时间大于90 s后,流痕一般可以超过3级,转移时间超过120 s后流痕一般为4级(见表2),整个表面有花斑。
表2 转移时间与流痕等级
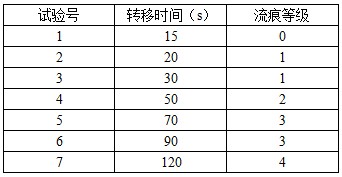
注:三酸比例(1%)磷酸:硫酸:硝酸=73:24:3;铜0.05 g/L;抛光温度85℃,抛光时间2.5min;维嘉抛光添加剂。
如果抛光温度大于100℃,转移时间大于90 s,流痕就变成了花斑。对流痕处进行XPS和EXM分析,结果见表3和图。两种不同分析方法的结果均表明流痕的主要化学成分是硫酸铝。笔者认为这是由于试样从抛光槽中提出时,粘附在试样表面的三酸液膜在铜离子的作用下继续同铝反应,并可见棕红色的二氧化氮气体从试样表面上释放出来,说明硝酸的浓度随着转移时间的增长而不断下降,试样表面沉积下来的铜越来越多,从试样表面溶解下来的铝离子也越来越多,而硫酸的浓度几乎未变,此时又没有可补充的硝酸和水分,于是从试样表面溶解下来的铝离子就同硫酸作用变成硫酸铝,随着转移时间的延长,试样表面的水分不断挥发,硫酸铝达到了其溶解度的极限就在试样的表面沉积下来形成流痕。
2.2 抛光添加剂浓度的影响
由表3和图1的分析结果可知流痕的化学成分是硫酸铝,为了避免其在转移过程中析出,笔者设计了—强酸缓冲体系,即在一定的范围内,添加剂A、B在硝酸浓度的较低时可以提供质子,减少铜在试样表面上的沉积和铝的溶解,从而达到避免硫酸铝的沉积和流痕产生的目的。
2 结果与讨论
通过实验,整个化学抛光过程中的各种因素对流痕作用力的大小依次是(从大至小):转移时间,抛光添加剂浓度,磷酸与硫酸的体积比及抛光温度。
2.1 转移时间的影响
一般说来,抛光温度85℃时试样从抛光槽提出后其表面上仍在进行剧烈反应,并伴有黄烟和白色的泡沫产生。泡沫由于重力的作用向下滑落,有些地方滑落得相对快些,有些地方滑落得相对慢些。水洗后发现:泡沫滑落快的地方光亮些,滑落慢的地方暗些,这样就形成了明暗交替的横向条纹流痕。将有流痕的试样放在1:1或更浓的硝酸溶液中浸泡也不能使之溶解。
实验表明:试样抛光好后,从抛光槽转移至水洗槽所花的时间越长流痕就越严重,转移时间大于90 s后,流痕一般可以超过3级,转移时间超过120 s后流痕一般为4级(见表2),整个表面有花斑。
表2 转移时间与流痕等级
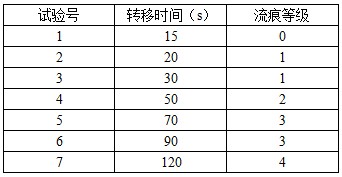
注:三酸比例(1%)磷酸:硫酸:硝酸=73:24:3;铜0.05 g/L;抛光温度85℃,抛光时间2.5min;维嘉抛光添加剂。
如果抛光温度大于100℃,转移时间大于90 s,流痕就变成了花斑。对流痕处进行XPS和EXM分析,结果见表3和图。两种不同分析方法的结果均表明流痕的主要化学成分是硫酸铝。笔者认为这是由于试样从抛光槽中提出时,粘附在试样表面的三酸液膜在铜离子的作用下继续同铝反应,并可见棕红色的二氧化氮气体从试样表面上释放出来,说明硝酸的浓度随着转移时间的增长而不断下降,试样表面沉积下来的铜越来越多,从试样表面溶解下来的铝离子也越来越多,而硫酸的浓度几乎未变,此时又没有可补充的硝酸和水分,于是从试样表面溶解下来的铝离子就同硫酸作用变成硫酸铝,随着转移时间的延长,试样表面的水分不断挥发,硫酸铝达到了其溶解度的极限就在试样的表面沉积下来形成流痕。
2.2 抛光添加剂浓度的影响
由表3和图1的分析结果可知流痕的化学成分是硫酸铝,为了避免其在转移过程中析出,笔者设计了—强酸缓冲体系,即在一定的范围内,添加剂A、B在硝酸浓度的较低时可以提供质子,减少铜在试样表面上的沉积和铝的溶解,从而达到避免硫酸铝的沉积和流痕产生的目的。
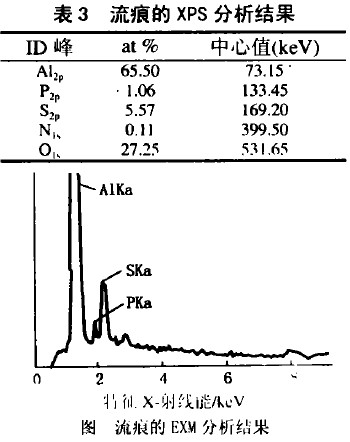
将三酸比例、铜的浓度、抛光时间和温度固定不变,改变添加剂A、B的比例,见表4,转移时间在70 s内,添加剂的比例A:B控制在1.0~2.5的范围内,试样表面可以达到镜面光亮,流痕在1级以内,可见抛光添加剂对流痕有较强的抑制作用。
表4 添加剂浓度对流痕的影响
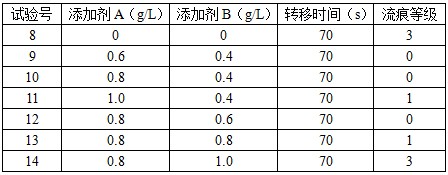
注:三酸比例(V%)磷酸:硫酸:硝酸=73:24:3;铜0.05g/L;抛光温度85℃,抛光时间2.5min。
2.3 磷酸与硫酸体积的影响
将硝酸的体积比控制在3%,转移时间及其他条件不变,只改变磷酸与硫酸的体积比所得到的流痕结果见表5。
表5 磷酸与硫酸不同体积比时的流痕情况
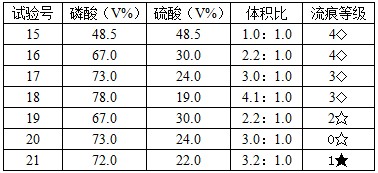
注:抛光温度85℃;时间2.5min;转移时间70s;◇未加抛光剂;☆加入抛光剂A:0.6g/L,B:0.4g/L;★加入2%体积的水。
由表可见,抛光槽中硫酸的比例越高,同等条件下产生的流痕越严重,因为硫酸浓度越大,生成硫酸铝沉积所需要的铝离子的浓度越小,转移时间在实际生产中不可能少于70 s(因为:一是行吊的速度限制:二是转移时间太短,带出的抛光液太多造成成本上升。)因而在含硫酸比例较高的三酸体系中很容易产生流痕,即使加入了抛光添加剂(见19号实验),其流痕等级也很难被用户接收。磷酸:硫酸=3:1时加入了抛光剂可以有效地防止流痕的产生(见20号实验),21号实验只收入了2%体积的水,其他条件不变流痕基本消失也进一步说明了流痕是由于硫酸铝的沉积而造成的。
2.4 抛光温度的影响
相同的三酸配比、转移时间、抛光添加剂浓度,抛光温度不同时试样上所产生的流痕等级也不同。抛光温度越高,流痕的等级也越高。这是因为抛光温度越高,试样从抛光槽·提出时其温度也越高(见表6),转移期间所进行的抛光反应也越剧烈,即硝酸消耗得更快,水分挥发也更严重,生成硫酸铝沉淀的机会更大,所以流痕等级越高。
表6 不同抛光温度时的流痕等级
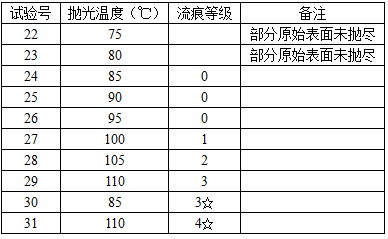
注:磷酸:硫酸:硝酸(V%)=73:24:3;铜0.05g/L;抛光时间3.5min;转移时间70s;抛光添加剂A 0.6g/L;抛光添加剂B 0.4g/L;☆未加抛光添加剂。
3 结论
铝合金化学抛光好后,从抛光槽提出转移到水洗槽的时间超过某一数值,由于硫酸铝的沉积而产生了流痕,流痕主要发生在泡沫滑落较慢的地方,因为试样从抛光槽中提出时粘附在试样表面的三酸液膜在铜离子的作用下继续同铝反应,硝酸的浓度随着转移时间的增长而不断下降,硫酸浓度几乎不变,此时又没有可补充的硝酸和水分,于是从试样表面溶解下来的铝离子就变成硫酸铝,随着转移时间的延长,水分不断挥发,硫酸铝达到了其溶解度的极限后就沉淀在试样的表面,形成了流痕。
加入抛光添加剂可以延长转移时间。如没有加入抛光添加剂,要想将流痕控制在0~1级范围内转移时间必须小于30s,这在实际生产中是难以办到的。加入抛光添加剂后,如果添加剂浓度为A 0.6 g/L,B 0.4 g/L,转移时间可以延长到70 s,流痕等级都能控制在0-1级范围内。
抛光添加剂A、B对流痕有很好的抑制作用,其详细的作用机理有待进一步的探讨。
上一篇: 铝合金碱性电化学抛光新工艺
下一篇: 铝合金碱性抛光液及其工艺条件