铝合金环保型无烟化学抛光工艺的研究
铝合金环保型无烟化学抛光工艺的研究
孙洪 波李轶 熊仕显 袁孚胜
(江西理工大学材料与化学工程学院,江西 赣州341000)
摘要:为了消除传统的三酸抛光对环境和人体健康的危害,开发了以磷酸—硫酸为基础液,并加入添加剂的无烟化学抛光工艺。首先研究了不合添加剂时各种因素对抛光质量的影响,并在此基础上选出最佳工艺参数,确定复合添加剂的质量浓度。结果表明:在H3PO4(体积分数为85%):H2SO4(体积分数为98%)=2:1,Al3+ 8~10 g/L,WYZ-1型复合添加剂10 g/L,95~110℃,1~2 min工艺条件下,可以提高抛光质量,抑制点蚀,获得较好的抛光效果,成功地解决了化学抛光中的黄烟污染问题,满足工业生产的需要。
前言
传统的三酸抛光铝及铝合金,由于抛光液中有大量的硝酸,在抛光时会产生大量的氮氧化物黄烟,生产中废气处理也往往达不到要求,严重地污染了环境,危害人体健康。为此,国内外近几十年来致力于研究无黄烟化学抛光工艺。
从上世纪70年代开始,日本、美国、前苏联等工业发达国家纷纷投入大批的人力物力研究不含HNO3的“两酸”抛光工艺。我国从上世纪80年代开始对铝合金无烟化学抛光技术进行研究,取得了一些成果。硝酸是强氧化剂,具有良好的抛光和表面平整作用。抛光剂中如果没有硝酸,抛光效果会明显减弱。所以必须向溶液中添加表面活性剂、润湿剂、缓蚀剂等添加剂。对于抛光产品来说,必须要满足表面平整度、光亮度、点蚀程度和失重率等抛光要求。
本文所研究铝合金无烟化学抛光工艺采用“磷酸+硫酸+添加剂”的方法(添加剂用代号WYZ-1表示),不仅在抛光过程中不产生黄烟,其抛光效果与传统的三酸抛光效果相当,甚至超过三酸抛光。
1 实验
1.1 试样与仪器
试样为冷轧5A02铝合金薄片,各化学成分的质量分数分别为:Si 0.4%,Fe 0.4%,Cu 0.1%,Mn 0.15%~0.40%,Mg 2.0%~2.8%,Ti 0.15%,其它成分≤0.15%,余量为Al。尺寸规格为50mm×50mm×l.2mm。
抛光质量评价指标主要有:镜面反射率、金属失重率和点蚀状况。
将抛光后的试片在CARY 500紫外—可见—红外分光光度计上测量反射率;用TG 3 288型分析天平测量试片抛光前后的质量变化,用公式ρ= △m/m计算金属失重率;通过目测抛光后的制品表面有无腐蚀麻点来判断点蚀状况。
1.2 实验方法
由于抛光质量受到基础液配比、抛光温度、时间、溶液中铝离子的质量浓度、添加剂等因素的影响,因此,采用正交实验方法对各种因素进行分析。首先,研究不含添加剂时各因素对抛光质量的影响,确定最佳参数,然后在此基础上调整、确定复合添加剂WYZ-1,使之达到满意的抛光效果,得到合理的无黄烟化学抛光工艺。
2 抛光工艺的研究
2.1 磷酸—硫酸基础液对抛光质量的影响
2.1.1 磷酸—硫酸的配比
图1和图2为不同磷酸-硫酸的配比对抛光反射率和金属失重率的影响。实验温度为100℃,时间为1 min。从图1,2中可以看出:在不含任何添加剂时,铝合金的抛光反射率,随磷酸比例的增大,光亮度增加,抛光时间也逐渐缩短,在2:1时达到最大值。随着磷酸比例的逐渐增大,光亮度下降,所需要的时间也逐渐增加。在增加光亮度方面,磷酸起主要作用。这是因为磷酸的黏稠度大,在凹处磷酸多,而在凸处的磷酸相对较少,黏液膜薄,而凹处黏液膜较厚,不易于扩散,从而实现整平抛光。但随磷酸比例的增大,很容易出现过腐蚀。这是因为硫酸在抛光过程中起到氧化-钝化作用,因此,硫酸的体积浓度的增加可以减轻铝的局部腐蚀,提高整平效果,进而提高反射率。而当硫酸的比例大于磷酸的比例时,抛光时间加长,光亮度下降得比较迅速。这是因为此时溶液黏度降低,凹处和凸处的黏液膜都非常薄,在高温下容易产生全面腐蚀和“转移腐蚀”,反而降低反射率。
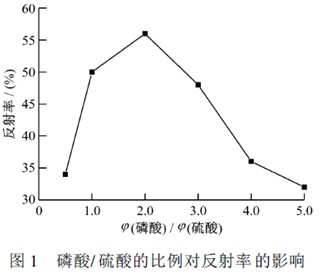
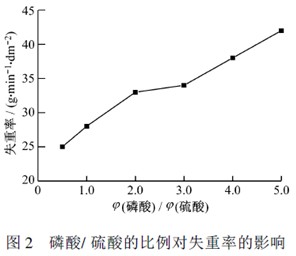
2.1.2 抛光时间和温度
温度、时间对光亮度的影响很大。特别是温度的影响更为明显。在一定范围内随着温度上升,抛光亮度明显提高。在低温时,随着抛光时间的延长,光亮度呈上升趋势。高温时,抛光的光亮度很高,但是随着温度的上升,时间的延长,抛光件容易产生过腐蚀,而且过腐蚀严重时不仅使抛光亮度急剧下降,还会导致工件报废,所以在温度高时,必须控制好时间。总的说来,抛光效果随着温度上升而提高,温度低,抛光时间就要延长,但抛光效果提高不大;温度高,抛光时间就可缩短,其抛光效果也有明显提高。
2.1.3 铝离子的质量浓度
图3和图4为铝离子的质量浓度对腐蚀率和反射率的影响。
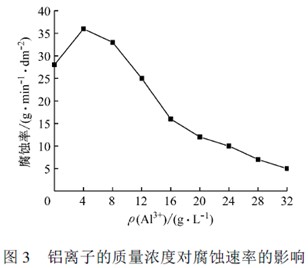
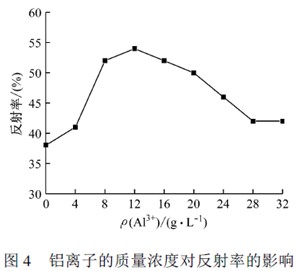
从上世纪70年代开始,日本、美国、前苏联等工业发达国家纷纷投入大批的人力物力研究不含HNO3的“两酸”抛光工艺。我国从上世纪80年代开始对铝合金无烟化学抛光技术进行研究,取得了一些成果。硝酸是强氧化剂,具有良好的抛光和表面平整作用。抛光剂中如果没有硝酸,抛光效果会明显减弱。所以必须向溶液中添加表面活性剂、润湿剂、缓蚀剂等添加剂。对于抛光产品来说,必须要满足表面平整度、光亮度、点蚀程度和失重率等抛光要求。
本文所研究铝合金无烟化学抛光工艺采用“磷酸+硫酸+添加剂”的方法(添加剂用代号WYZ-1表示),不仅在抛光过程中不产生黄烟,其抛光效果与传统的三酸抛光效果相当,甚至超过三酸抛光。
1 实验
1.1 试样与仪器
试样为冷轧5A02铝合金薄片,各化学成分的质量分数分别为:Si 0.4%,Fe 0.4%,Cu 0.1%,Mn 0.15%~0.40%,Mg 2.0%~2.8%,Ti 0.15%,其它成分≤0.15%,余量为Al。尺寸规格为50mm×50mm×l.2mm。
抛光质量评价指标主要有:镜面反射率、金属失重率和点蚀状况。
将抛光后的试片在CARY 500紫外—可见—红外分光光度计上测量反射率;用TG 3 288型分析天平测量试片抛光前后的质量变化,用公式ρ= △m/m计算金属失重率;通过目测抛光后的制品表面有无腐蚀麻点来判断点蚀状况。
1.2 实验方法
由于抛光质量受到基础液配比、抛光温度、时间、溶液中铝离子的质量浓度、添加剂等因素的影响,因此,采用正交实验方法对各种因素进行分析。首先,研究不含添加剂时各因素对抛光质量的影响,确定最佳参数,然后在此基础上调整、确定复合添加剂WYZ-1,使之达到满意的抛光效果,得到合理的无黄烟化学抛光工艺。
2 抛光工艺的研究
2.1 磷酸—硫酸基础液对抛光质量的影响
2.1.1 磷酸—硫酸的配比
图1和图2为不同磷酸-硫酸的配比对抛光反射率和金属失重率的影响。实验温度为100℃,时间为1 min。从图1,2中可以看出:在不含任何添加剂时,铝合金的抛光反射率,随磷酸比例的增大,光亮度增加,抛光时间也逐渐缩短,在2:1时达到最大值。随着磷酸比例的逐渐增大,光亮度下降,所需要的时间也逐渐增加。在增加光亮度方面,磷酸起主要作用。这是因为磷酸的黏稠度大,在凹处磷酸多,而在凸处的磷酸相对较少,黏液膜薄,而凹处黏液膜较厚,不易于扩散,从而实现整平抛光。但随磷酸比例的增大,很容易出现过腐蚀。这是因为硫酸在抛光过程中起到氧化-钝化作用,因此,硫酸的体积浓度的增加可以减轻铝的局部腐蚀,提高整平效果,进而提高反射率。而当硫酸的比例大于磷酸的比例时,抛光时间加长,光亮度下降得比较迅速。这是因为此时溶液黏度降低,凹处和凸处的黏液膜都非常薄,在高温下容易产生全面腐蚀和“转移腐蚀”,反而降低反射率。
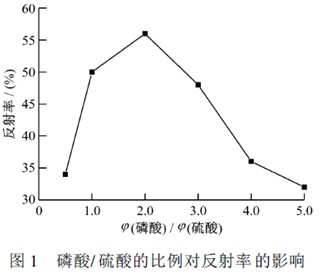
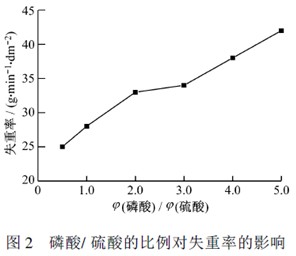
2.1.2 抛光时间和温度
温度、时间对光亮度的影响很大。特别是温度的影响更为明显。在一定范围内随着温度上升,抛光亮度明显提高。在低温时,随着抛光时间的延长,光亮度呈上升趋势。高温时,抛光的光亮度很高,但是随着温度的上升,时间的延长,抛光件容易产生过腐蚀,而且过腐蚀严重时不仅使抛光亮度急剧下降,还会导致工件报废,所以在温度高时,必须控制好时间。总的说来,抛光效果随着温度上升而提高,温度低,抛光时间就要延长,但抛光效果提高不大;温度高,抛光时间就可缩短,其抛光效果也有明显提高。
2.1.3 铝离子的质量浓度
图3和图4为铝离子的质量浓度对腐蚀率和反射率的影响。
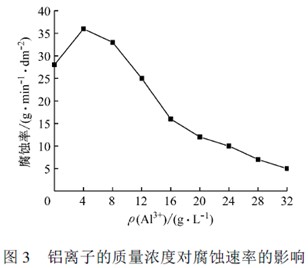
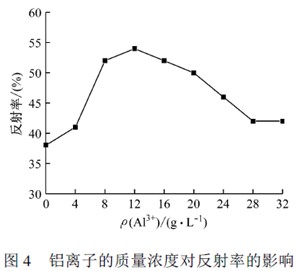
由图3,4可知:当刚加入铝离子时,随着铝离子的加大,腐蚀速率加大。因为此时铝离子的质量浓度比较低,溶液黏度还较低,还不能真正起到抑制铝的腐蚀,抛光效果变化不大。当铝离子的质量浓度达到6 g/L时,随着铝离子质量浓度逐渐增大,腐蚀速率逐渐下降,抛光效果也越来越好。铝离子的质量浓度在8~24 g/L时,抛光效果最好。当铝离子的质量浓度达到25~28 g/L时,腐蚀速率还是下降的,但抛光的光泽性也下降了。这是因为一定质量浓度的铝离子能抑制铝的均匀腐蚀和局部腐蚀,提高反射率;超过一定的范围,此时抛光液随铝离子的质量浓度加大,黏稠度升高,离子之间的运动和交换就非常困难,降低了反应速率,所以不利于整平。在实际生产中,当铝离子达到一定的质量浓度后,工件带出的铝量和铝的溶解量接近,但工件取出时必然带出槽液,液面会降低,所以必须补充新槽液。另外,磷酸和铝离子反应生成磷酸铝,当铝离子的质量浓度大时,达到了溶解饱和,必然结晶析出,沉积于槽底或悬浮于槽液中,黏附在工件上,使工件产生白色的麻点,严重时使工件报废。如果出现这种情况,必须打捞出磷酸铝结晶体,补充新溶液。
2.1.4 转移时间
通过实验观察,试样从抛光槽转移至水洗槽所花的时间越长,流痕就越严重。表1为转移时间与流痕的关系。从表1可以看出:15 s以前,基本没有流痕;15~30 s之间,有轻微的流痕,在这区间流痕清晰度随时间的增加也增大,只不过增加的幅度小;超过70 s后,流痕剧烈地增加;转移时间大于90 s后,流痕一般可以超过3级;转移时间超过120 s后流痕一般为4级,最严重的整个表面有花斑;并且温度越高,转移时间应该越短,因为温度高,残留在试样上的溶液反应就越强烈,时间越长,流痕就越严重,所以在生产中应减少转移时间。
表1 转移时间与流痕等级
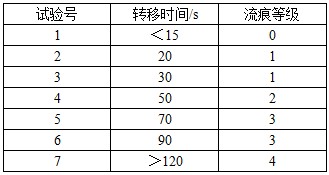
2.1.4 转移时间
通过实验观察,试样从抛光槽转移至水洗槽所花的时间越长,流痕就越严重。表1为转移时间与流痕的关系。从表1可以看出:15 s以前,基本没有流痕;15~30 s之间,有轻微的流痕,在这区间流痕清晰度随时间的增加也增大,只不过增加的幅度小;超过70 s后,流痕剧烈地增加;转移时间大于90 s后,流痕一般可以超过3级;转移时间超过120 s后流痕一般为4级,最严重的整个表面有花斑;并且温度越高,转移时间应该越短,因为温度高,残留在试样上的溶液反应就越强烈,时间越长,流痕就越严重,所以在生产中应减少转移时间。
表1 转移时间与流痕等级
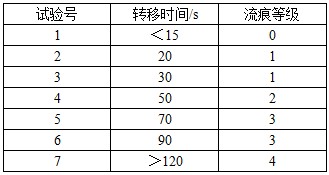
2.2 添加剂
2.2.1 WYZ-1复合添加剂的最佳组成
通过分析磷酸—硫酸基础液对抛光亮度的影响,初步确定适合的抛光液为磷酸(体积分数为85%):硫酸(体积分数为98%)=2:1,铝离子的质量浓度为10 g/L。在此基础上进行添加物成分的实验,并进一步研究、分析各因素对抛光质量的影响。实验条件:抛光温度100℃,抛光时间60 s。
添加剂的质量浓度是一个比较敏感的因素,其质量浓度的改变对抛光反射率、失重率和过腐蚀的抑制作用都非常明显。添加剂由缓蚀剂、氧化剂、重金属盐、铝离子配位剂、表面活性剂等复合而成,具有缓冲、润湿、整平、增光等作用。增加光亮的作用主要表现在添加剂具有吸附作用,吸附在凹处,降低了凹处的溶解速率;同时添加剂中的重金属离子在凹处还原,使凸处溶解速率加快,从而起到光亮整平作用。由于添加剂中表面活性剂起润湿表面,促进气泡快速析出的作用,消除了表面斑点的产生。
经正交实验后获得WYZ-1型复合添加剂的最佳组成:二苯胺磺酸钠0.4 g/L,己酸0.4 g/L,丁基硫醇0.2 g/L,双氧水15 g/L,硫酸铜0.6 g/L,N-烷基硫脲0.4 g/L,多聚磷酸钠0.8 g/L。
2.2.2 WYZ-1型复合添加剂抑制酸雾的效果
在实验中观察发现:在磷酸—硫酸基础液中加入WYZ-1型复合添加剂后,抛光反应比较平稳,铝表面有大量气泡生成,但是溶液不呈沸腾状态,气泡逸出抛光液的过程较快。因为气泡体积比较密集细小,随着溶液的搅拌,气泡破裂逸出溶液表面,此时不会形成飞溅的液滴溅射到周围的大气中,防止形成严重的酸雾;同时细小密集的气泡在抛光液表面形成约2~3 cm厚的泡沫层,泡沫层阻碍了气体的逸出,所以搅拌速率要加快。气泡体积的减小以及气泡层的形成很好地抑制了酸雾,在离抛光槽很近的位置也几乎感觉不到酸雾。
2.2.3 不同温度下复合添加剂对反射率的影响
图5为不同温度条件下WYZ-1型添加剂的质量浓度对反射率的影响。从图5可以看出:添加剂的质量浓度的增加有利于提高反射率,尤其是在较高温度时(100℃和110℃),反射率随添加剂的质量浓度的增加明显升高。这主要是在温度较高时,酸液对铝的腐蚀比较剧烈,对微凸起处的溶解比较快,此时添加剂的质量浓度越高,越能很好地抑制微凸起部位以外的过腐蚀,提高整平效果:而温度较低时(90℃),酸液对铝的溶解腐蚀相对平缓,添加剂的质量浓度为5 g/L时,己可充分发挥作用,所以再增加添加剂的质量浓度意义不大。
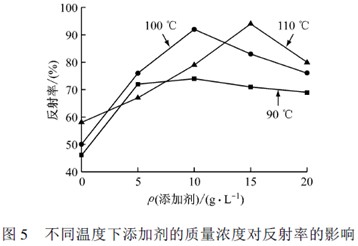
2.2.1 WYZ-1复合添加剂的最佳组成
通过分析磷酸—硫酸基础液对抛光亮度的影响,初步确定适合的抛光液为磷酸(体积分数为85%):硫酸(体积分数为98%)=2:1,铝离子的质量浓度为10 g/L。在此基础上进行添加物成分的实验,并进一步研究、分析各因素对抛光质量的影响。实验条件:抛光温度100℃,抛光时间60 s。
添加剂的质量浓度是一个比较敏感的因素,其质量浓度的改变对抛光反射率、失重率和过腐蚀的抑制作用都非常明显。添加剂由缓蚀剂、氧化剂、重金属盐、铝离子配位剂、表面活性剂等复合而成,具有缓冲、润湿、整平、增光等作用。增加光亮的作用主要表现在添加剂具有吸附作用,吸附在凹处,降低了凹处的溶解速率;同时添加剂中的重金属离子在凹处还原,使凸处溶解速率加快,从而起到光亮整平作用。由于添加剂中表面活性剂起润湿表面,促进气泡快速析出的作用,消除了表面斑点的产生。
经正交实验后获得WYZ-1型复合添加剂的最佳组成:二苯胺磺酸钠0.4 g/L,己酸0.4 g/L,丁基硫醇0.2 g/L,双氧水15 g/L,硫酸铜0.6 g/L,N-烷基硫脲0.4 g/L,多聚磷酸钠0.8 g/L。
2.2.2 WYZ-1型复合添加剂抑制酸雾的效果
在实验中观察发现:在磷酸—硫酸基础液中加入WYZ-1型复合添加剂后,抛光反应比较平稳,铝表面有大量气泡生成,但是溶液不呈沸腾状态,气泡逸出抛光液的过程较快。因为气泡体积比较密集细小,随着溶液的搅拌,气泡破裂逸出溶液表面,此时不会形成飞溅的液滴溅射到周围的大气中,防止形成严重的酸雾;同时细小密集的气泡在抛光液表面形成约2~3 cm厚的泡沫层,泡沫层阻碍了气体的逸出,所以搅拌速率要加快。气泡体积的减小以及气泡层的形成很好地抑制了酸雾,在离抛光槽很近的位置也几乎感觉不到酸雾。
2.2.3 不同温度下复合添加剂对反射率的影响
图5为不同温度条件下WYZ-1型添加剂的质量浓度对反射率的影响。从图5可以看出:添加剂的质量浓度的增加有利于提高反射率,尤其是在较高温度时(100℃和110℃),反射率随添加剂的质量浓度的增加明显升高。这主要是在温度较高时,酸液对铝的腐蚀比较剧烈,对微凸起处的溶解比较快,此时添加剂的质量浓度越高,越能很好地抑制微凸起部位以外的过腐蚀,提高整平效果:而温度较低时(90℃),酸液对铝的溶解腐蚀相对平缓,添加剂的质量浓度为5 g/L时,己可充分发挥作用,所以再增加添加剂的质量浓度意义不大。
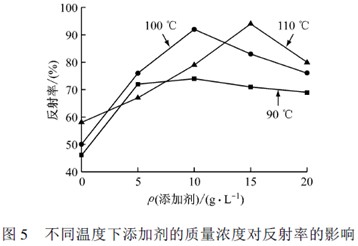
在图5中,虽然添加剂的质量浓度为15 g/L,温度为110℃时反射率最高,但是参照表2,可以发现此时对应的失重率也略高。所以如果对光亮度要求不是特别高,建议采用添加剂的质量浓度为10g/L,温度为100℃的工艺条件,这样既避免了过腐蚀也减少了抛光中的金属损失,而且此时的生产成本也有所降低。
表2 添加剂的质量浓度与点腐蚀和失重率的关系
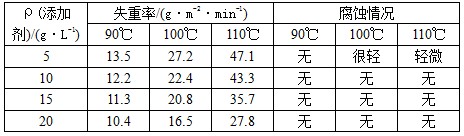
在磷酸—硫酸基础液中加入复合添加剂后,可以得到良好的镜面反射率,不出现过腐蚀麻点和“转移腐蚀”。实验药品易得到,价格低,抛光质量容易控制,操作条件完全可以满足工业生产的需要。本实验研究得到的无黄烟化学抛光技术不但实现了完全无氮氧化合物的目标,而且还很好地抑制了酸雾,是一种比较理想的环保技术。
3 结论
无黄烟化学抛光的最佳工艺条件:H3PO4(体积浓度为85%):H2SO4(体积浓度为98%)=2:1,Al3+ 10 g/L,WYZ-1型复合添加剂10 g/L,100℃,1~2 min。
该抛光技术不仅成功地解决了化学抛光中的黄烟污染问题,而且突破了以往无黄烟化学抛光制品亮度低的主要缺陷,使抛光后铝制品的镜面反射率达到甚至超过三酸化学抛光的水平,满足工业生产的需要。
表2 添加剂的质量浓度与点腐蚀和失重率的关系
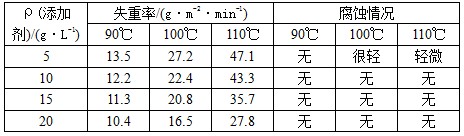
在磷酸—硫酸基础液中加入复合添加剂后,可以得到良好的镜面反射率,不出现过腐蚀麻点和“转移腐蚀”。实验药品易得到,价格低,抛光质量容易控制,操作条件完全可以满足工业生产的需要。本实验研究得到的无黄烟化学抛光技术不但实现了完全无氮氧化合物的目标,而且还很好地抑制了酸雾,是一种比较理想的环保技术。
3 结论
无黄烟化学抛光的最佳工艺条件:H3PO4(体积浓度为85%):H2SO4(体积浓度为98%)=2:1,Al3+ 10 g/L,WYZ-1型复合添加剂10 g/L,100℃,1~2 min。
该抛光技术不仅成功地解决了化学抛光中的黄烟污染问题,而且突破了以往无黄烟化学抛光制品亮度低的主要缺陷,使抛光后铝制品的镜面反射率达到甚至超过三酸化学抛光的水平,满足工业生产的需要。
上一篇: 铝合金高频窄脉冲电化学抛光的研究
下一篇: 铝合金碱性电化学抛光新工艺