铝碱蚀废液再生及铝的回收
铝碱蚀废液再生及铝的回收
朱静 裴秀中
(安徽工业大学化学工程系,安徽马鞍山243002)
(安徽工业大学化学工程系,安徽马鞍山243002)
摘要:铝型材表面处理工艺产生的碱蚀废液可采用晶种分解法回收氢氧化铝,实现再生碱液的循环使用。
引言
我国建筑用铝型材业自70年代引进以来至今已有了长足发展,铝型材氧化着色工厂应运而生。这些生产线约有一半从国外引进或国内正规设计制造,其大多有较为完备的环保措施。但还有不少中小型厂尚未对表面处理工序产生的废液采取有效的回收工艺,废液只能排放,不仅造成大量资源浪费,而且严重污染环境,亟需治理。
铝型材阳极氧化工艺中碱洗工序铝溶损量最大,可占全部生产过程中铝损耗量的90%以上。一座年产万吨的氧化着色铝型材厂碱洗工序约有35 kg/h溶铝损失。照此推算,全国铝型材行业仅计氧化着色工艺的碱洗工序,平均每年溶铝损失可达3万t以上,年耗烧碱可达5万t。可见,对碱洗废液再生处理可获较大的经济效益,且具有环保价值。
本文通过实验探讨了铝碱蚀液晶种分解回收工艺的主要影响因素,优化了回收工艺参数,并设计了铝碱蚀液闭路循环的回收工艺,从而达到节能降耗、防治污染的目的。
1 回收原理
铝材在碱蚀过程中发生如下反应:2Al+ 2NaOH+2H2O→2NaAlO2+3H2↑
当溶铝量达50 g/L时碱蚀液严重老化失效。若采用适当条件使NaAlO2水解成氢氧化铝结晶析出,则碱蚀液可循环使用。分析Na2O-Al2O3-H2O三元相图,可知Na2O:Al2O3摩尔比必大于1。回收过程发生如下反应:NaAlO2+2H2O→Al(OH)3↓+NaOH
为了保证铝回收率,节水降碱耗并防止环境污染,可采用图1所示工艺流程实现铝碱蚀液再生闭路循环工艺。本工艺具有采用双效并流升膜蒸发器浓缩原液和空气搅拌自然冷却结晶器,并采用二次沉降分离粗颗粒(产品)与细颗粒(晶种);产品加热软水搅拌洗涤过滤以保证纯度等特点。
铝型材阳极氧化工艺中碱洗工序铝溶损量最大,可占全部生产过程中铝损耗量的90%以上。一座年产万吨的氧化着色铝型材厂碱洗工序约有35 kg/h溶铝损失。照此推算,全国铝型材行业仅计氧化着色工艺的碱洗工序,平均每年溶铝损失可达3万t以上,年耗烧碱可达5万t。可见,对碱洗废液再生处理可获较大的经济效益,且具有环保价值。
本文通过实验探讨了铝碱蚀液晶种分解回收工艺的主要影响因素,优化了回收工艺参数,并设计了铝碱蚀液闭路循环的回收工艺,从而达到节能降耗、防治污染的目的。
1 回收原理
铝材在碱蚀过程中发生如下反应:2Al+ 2NaOH+2H2O→2NaAlO2+3H2↑
当溶铝量达50 g/L时碱蚀液严重老化失效。若采用适当条件使NaAlO2水解成氢氧化铝结晶析出,则碱蚀液可循环使用。分析Na2O-Al2O3-H2O三元相图,可知Na2O:Al2O3摩尔比必大于1。回收过程发生如下反应:NaAlO2+2H2O→Al(OH)3↓+NaOH
为了保证铝回收率,节水降碱耗并防止环境污染,可采用图1所示工艺流程实现铝碱蚀液再生闭路循环工艺。本工艺具有采用双效并流升膜蒸发器浓缩原液和空气搅拌自然冷却结晶器,并采用二次沉降分离粗颗粒(产品)与细颗粒(晶种);产品加热软水搅拌洗涤过滤以保证纯度等特点。
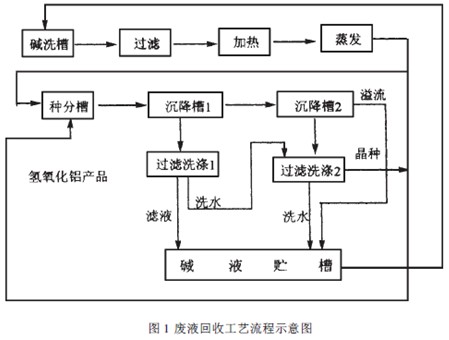
2 实验结果与讨论
2.1 溶液初始质量浓度对铝回收率的影响
当摩尔比(Na2O:Al2O3)1.7,晶体系数(添加晶种中Al2O3含量与溶液中Al2O3含量之比)1.7,分解时间12 h,实验温度控制在初温75℃,终温35℃(以下实验温度区间同),偏铝酸钠溶液初始质量浓度对回收率的影响见图2。
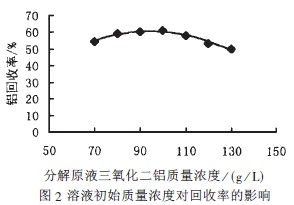
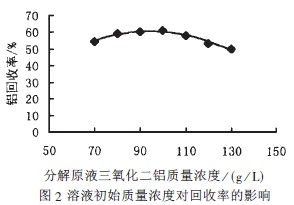
由图2可见溶液初始质量浓度在Al2O3含量近100 g/L处分解率达最大值,浓度继续增大或减小均使分解率降低。这是由于存摩尔比一定的条件下,浓度偏离最佳浓度均使溶液过饱和度下降的缘故。
2.2 晶种系数的影响
溶液Al2O3,初始质量浓度105 g/L,摩尔比1.57,分解时间 12 h,晶种系数对回收率的影响见图3。实验结果表明:随着晶 种系数的增大回收率亦上升,但晶种系数增大到一定限度后对回收率增益不大,这是因为过大的晶种量使结晶器有效容积减小。
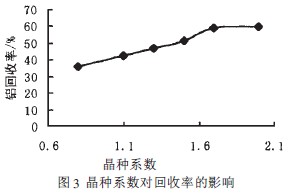
2.3 摩尔比的影响
Al2O3初始质量浓度105 g/L,晶种系数0.8,分解时间12h,改变溶液摩尔比实验结果见图4。由图4可知分子比值上升不利NaAlO2:溶液水解析出Al(OH)3。这是因为在此操作范围内NaOH质量浓度上升使Al(OH)3,溶解度增大。
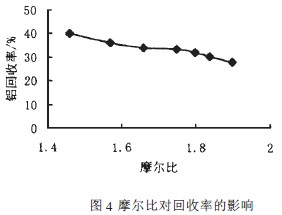
2.4 分解时间的影响
溶液初始质量浓度、晶种系数保持不变,摩尔比1. 57,晶种分解时间由6h延至70 h。由图5可见晶种系数较小时分解过程有数小时诱导期,此段时间内分解缓慢。此后随着分解时间延长分解率上升,但超过60 h曲线趋于平坦,表明过度延长结晶时间是无益的。
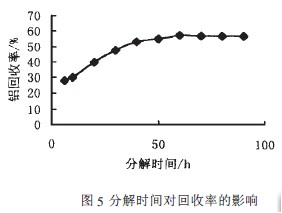
2.5 正交实验
根据以上实验结果安排A,B,C,D 4因素水平表(表1)组织正交实验以优化分解操作工艺条件,其直观图见图6。分解初温68℃,终温34℃。
由此确定最优操作参数:ρ(Al2O3)初105 g/L,摩尔比1.6,晶种系数1.3,分解时间60 h。据此参数做实验,回收率达75%。
3 结 论
(1)采用晶种分解法再生铝碱蚀液适宜的工艺操作参数为分解原液初始Al2O3浓度105 g/L,分子比1.6,晶种系数1.3,分解时间60 h,铝回收率高于70%。
(2)采用铝碱蚀废液晶种分解闭路循环工艺流程简单、设备少、操作稳定,适于在中小型铝材厂推广,有利于节能降耗保护环境。
上一篇: 铝合金低倍碱蚀槽结垢抑制方法
下一篇: 铝阳极氧化碱蚀槽的维护