铝阳极氧化碱蚀槽的维护
铝阳极氧化碱蚀槽的维护
许旋,罗帆,林国辉
(1.华南师范大学化学系,广东广州 510631;2.中山大学北校区化学教研室,广东广州 510089;3.华南师范大学测试中心,广东广州 5106311)
摘要:在铝合金阳极氧化生产工艺中,测定碱蚀槽液苛性钠、铝离子、添加剂的浓度。根据铝合金碱蚀工艺条件和铝材碱蚀后的表面状况。对碱蚀槽的槽液进行维护,提出了碱蚀常见故障和排除方法。本文还探讨了碱蚀机理。
1 前言
碱蚀是预处理中的重要工序,是获得均匀色调和表面光泽的重要因素之一。无论是挤压型材、板材,在挤压或轧制成型、搬运时,都会出现缺陷,通过抛光研磨虽可除去这些缺陷,但较好的方法是采取碱蚀来腐蚀表面。碱蚀是建筑铝型材表面处理的关键步骤,碱蚀的目的是去除铝材表面的自然氧化膜,活化表面以利于阳极氧化。碱蚀不但能除去表面挤压粗纹等缺陷,获得平整光滑的表面,还能进一步除油净化表面。要达到较好的碱蚀效果,一般的碱蚀槽都要配合使用几种有机物络合剂作为添加剂,添加剂的作用为允许槽液中高浓度的铝离子存在时不会使铝材局部过腐蚀和产生蚀斑而影响产品外观,也不会生成氢氧化铝聚集结成硬块覆盖在槽壁、槽底和加热管上,形成一层白色坚硬的结垢。否则这些结垢的形成,必须停产清槽,导致碱的消耗和铝材损耗的增加。
因此必须对碱蚀槽中的碱蚀液进行维护,对苛性钠、铝离子、添加剂的浓度和槽液的温度进行控制。通常情况下,对碱蚀液的控制不当则会出现碱蚀不均匀的质量问题,若添加剂用量不足或用错添加剂,槽液会产生大量的沉淀而形成积垢,需要清除:若添加剂用量过多,则会限制碱蚀,甚至产生疵病。为此本文通过正确检测苛性钠、铝离子、添加剂的浓度来维护碱蚀槽的正常运作,并对碱蚀中出现的问题进行了探讨。
2 实验
2.1 试验工艺
工业上一般采用下面的生产工艺流程,文中的试验和分析均按此工艺进行:常温脱脂_→水洗→碱蚀-→水洗→水洗→出光→水洗→水洗→阳极氧化→二次水洗→封孔→二次水洗
2.2 碱蚀试验工艺条件
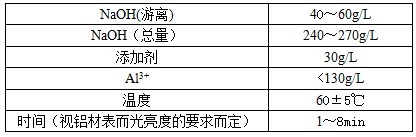
碱蚀是预处理中的重要工序,是获得均匀色调和表面光泽的重要因素之一。无论是挤压型材、板材,在挤压或轧制成型、搬运时,都会出现缺陷,通过抛光研磨虽可除去这些缺陷,但较好的方法是采取碱蚀来腐蚀表面。碱蚀是建筑铝型材表面处理的关键步骤,碱蚀的目的是去除铝材表面的自然氧化膜,活化表面以利于阳极氧化。碱蚀不但能除去表面挤压粗纹等缺陷,获得平整光滑的表面,还能进一步除油净化表面。要达到较好的碱蚀效果,一般的碱蚀槽都要配合使用几种有机物络合剂作为添加剂,添加剂的作用为允许槽液中高浓度的铝离子存在时不会使铝材局部过腐蚀和产生蚀斑而影响产品外观,也不会生成氢氧化铝聚集结成硬块覆盖在槽壁、槽底和加热管上,形成一层白色坚硬的结垢。否则这些结垢的形成,必须停产清槽,导致碱的消耗和铝材损耗的增加。
因此必须对碱蚀槽中的碱蚀液进行维护,对苛性钠、铝离子、添加剂的浓度和槽液的温度进行控制。通常情况下,对碱蚀液的控制不当则会出现碱蚀不均匀的质量问题,若添加剂用量不足或用错添加剂,槽液会产生大量的沉淀而形成积垢,需要清除:若添加剂用量过多,则会限制碱蚀,甚至产生疵病。为此本文通过正确检测苛性钠、铝离子、添加剂的浓度来维护碱蚀槽的正常运作,并对碱蚀中出现的问题进行了探讨。
2 实验
2.1 试验工艺
工业上一般采用下面的生产工艺流程,文中的试验和分析均按此工艺进行:常温脱脂_→水洗→碱蚀-→水洗→水洗→出光→水洗→水洗→阳极氧化→二次水洗→封孔→二次水洗
2.2 碱蚀试验工艺条件
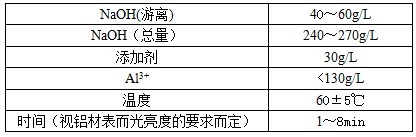
2.3 苛性钠、铝离子、添加剂分析测定
2.3.1 碱蚀槽液中总碱、铝、游离碱的测定
在酒石酸钾钠过量存在下,用盐酸滴定总碱,然后加入氟化钾,氢氧化铝与氟离子结合释放出氢氧根离子,再用盐酸滴定这些氢氧根离子,可计算出铝离子的量。反应过程为:
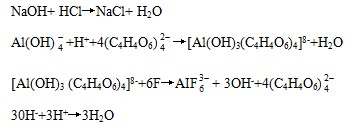
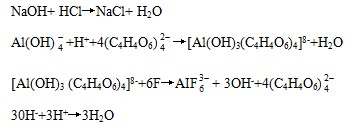
实验步骤为:准确吸取碱蚀液5. 00 mL于250 mL锥形瓶中。加入30 mL酒石酸钾钠溶液和50 mL蒸馏水,加入2滴酚酞指示剂,用盐酸标准溶液(浓度记为c(HCl))滴定至红色消失为终点,记下滴定读数为V1然后加入20 mL氟化钾溶液(此时溶液再显红色),继续用盐酸标准溶液滴定至红色消失为终点,记下滴定读数为V2。计算:
总碱 c(NaOH),g/L=40 c(HCl) V1/5.00
铝 c(Al),g/L= 27 c(HCl)V2/( 3×5.00)
游离碱 c( NaOH),g/L= 40 c(HCl)( V1-V2)/5.00
2.3.2 碱蚀槽液中添加剂的测定
碱蚀槽中的添加剂通常为葡萄糖酸钠、酒石酸钠、柠檬酸钠等与铝离子产生络合的络合剂,这些添加剂的多少对碱蚀槽液的性能有很大的影响,但要对这些添加剂进行一一检测却是十分困难且没有必要的,因此我们采用下面的方法来检测添加剂的含量。
用移液管移取25.00 mL槽液,放入250 mL的三角锥瓶中,加入蒸馏水100 mL,然后加入2 mL冰醋酸,再加入2 mL l%(质量分数)的淀粉溶液,用约0.1 mol/L碘溶液c(I2)滴定至蓝色半分钟不退为终点,记下读数V。计算:
添加剂用量,g/L= 17.2 c(l2)V
3 碱蚀槽的维护
3.1 成分的维护
根据铝合金阳极氧化生产工艺,在生产一定量的铝材后,要对碱蚀槽液进行分析。碱蚀溶液的铝离子高达120~130 g/L,NaOH则维持在40~60 g/L之间。由于碱蚀槽内加入由多种物质组成的添加剂,致使溶液中NaAlO2的含量达350~400g/L,碱蚀溶液的碱性很强,铝离子的含量非常高,这些都属于正常范围。然而生产过程中我们必须每天检测槽液成分的浓度,一旦不在正常范围内,即使生产正常也要及时补充添加剂或苛性钠,否则当形成Al( OH)3晶核时,就很容易生成Al(OH)3,沉淀,致使产品出现质量问题,槽液寿命缩短。当槽液中铝离子超过130 g/L时,只能采取排放部分槽液,补充一部分水,用氢氧化钠和添加剂调整至适合的浓度。
只有将槽液成分的浓度长期维持在正常的范围内进行生产,才能维护好槽液的寿命,生产出质量优良的铝材产品。
3.2 槽液温度的控制
碱蚀过程就是要减少铝表面的粗糙度,净化铝表面。必须在一定的温度下铝与碱才能迅速反应,因此当温度低时,要设置加热管来加热,然而铝与碱的反应也会产生热能,可能会导致温度过高,所以也要设置冷却管,必要的时候进行冷却,采用这些设备才能较好地维护槽液的温度。另外碱蚀后水洗的温度应维持在50±5℃,如碱蚀后水清洗不彻底,会引起铝表面凹凸不平,光泽也不均匀,清洗时间过长又会引起腐蚀斑纹,因此最好在槽上安装喷水头,以喷刷表面带出的碱液。
3.3 碱蚀的常见故障与排除方法
3. 3.1 过腐蚀故障
产生过腐蚀现象的原因如果是碱的浓度过大,则要采取稀释槽液的办法来解决:如果是因为温度太高或时间太长,则可采取降温或缩短操作时间来调整。
3.3.2 腐蚀速度过慢
这种故障与前述故障刚好相反,原因有:碱的浓度过稀,温度太低或时间太短,所以可以采用与前述相反的方法来解决,即加入碱,升温或延长时间。
3.3.3 腐蚀后产品有流痕、反光点
这种现象产生的原因是槽液被锌杂质污染,要更换槽液或加入锌抑制添加剂才能消除。
3.3.4 槽液产生沉淀、槽底出现结块
这是因为铝离子的浓度过高或添加剂的量不足引起的,解决办法是排放一部分槽液,补加水和添加剂;如果不是铝离子浓度过高而是因为槽液中添加剂量不足则补加添加剂即可。
4 讨论
4.1 碱蚀机理
铝进入碱蚀槽时,发生的反应为:去除自然氧化膜的反应 Al2O3+ 2NaOH= 2NaAlO2+H2O (1);铝基体的反应 2Al+ 2NaOH+ 2H2O= 2NaAlO2+3H2↑ (2)
上面的(l)和(2)反应都生成NaAlO2,当溶液中铝离子过多时,会造成NaAlO2水解形成Al(OH)3沉淀。为避免溶液Al(OH)3沉淀就必须抑制溶液中的NaAlO2发生水解,而抑制NaAlO2水解须使溶液中游离的铝离子不能过多,因此必须加入由络合剂、缓蚀剂、增稠剂与表面活性剂等组成的添加剂,使槽液中铝离子的总量虽大但游离的铝离子不多,NaAlO2不发生水解产生Al(OH)3沉淀,延长槽液的使用寿命,而且铝材表面的腐蚀速度缓慢,均匀腐蚀,不易产生过腐蚀现象,外观平滑,光泽好。
4.2 铝材表面的评判
评判标准:能除去表面挤压粗纹等缺陷,获得平整光滑的表面,能除油净化表面。
4.3 槽液评判
评判标准:按检测方法,碱蚀槽液的工艺条件均要符合所需要求,槽液没有大量的沉淀,没有形成积垢沉淀物。
5 结束语
碱蚀槽的维护对铝材的生产质量有很重要的影响,如何更好地维护好碱蚀槽的槽液是众多生产厂家要关注的问题,所以我们认为对碱蚀槽的槽液进行维护首先要有一整套的、准确的槽液检测方法,尤其是对添加剂的检测,这是很多厂家容易忽视的问题;其次是对槽液温度的控制,还有碱蚀中出现的故障现象、原因和处理方法都要有所熟悉,这样才能维护好碱蚀槽的正常工作。
上一篇: 铝碱蚀废液再生及铝的回收