铝合金阳极氧化膜的勃姆石溶胶封闭
铝合金阳极氧化膜的勃姆石溶胶封闭
周琦 贺春林 才庆魁 邵忠宝 朱学松
(1.东北大学材料与冶金学院,沈阳 110004;2.沈阳理工大学环境与化学工程学院,沈阳 110168;3.沈阳大学表面工程研究所,沈阳 110044)
(1.东北大学材料与冶金学院,沈阳 110004;2.沈阳理工大学环境与化学工程学院,沈阳 110168;3.沈阳大学表面工程研究所,沈阳 110044)
摘要:将铝合金阳极氧化膜浸入勃姆石(AlOOH)溶胶中进行封闭。以溶胶封闭膜表面密度、磷—铬酸质量损失、酸性点滴实验、染色实验为评价标准,对溶胶封闭进行了正交实验,然后研究溶胶的pH值、试片浸入溶胶时间对封闭膜表面密度和磷—铬酸质量损失的影响,获得如下的较优工艺条件:溶胶pH值为4.5~5.5,试片浸入溶胶时间为30 min,烘干封闭膜的温度为80℃,烘干时间为6h。溶胶法封闭后膜的点滴试液变色时间可达33 min,磷—铬酸质量损失低于3 g·m-2。极化曲线显示溶胶封闭膜的腐蚀电流密度比重铬酸盐封闭膜的降低2个数量级,其原因是溶胶不仅封闭了氧化膜的孔隙,而且在氧化膜的表面形成溶胶凝胶涂层。
溶胶—凝胶法可以用来制备耐蚀涂层,该类涂层对提高基材的化学耐久性、防止氧化、控制腐蚀有显著的效果,有可能完全替代传统表面处理使用的毒性物质铬酸盐处理工艺。
Voevodin等在铝合金表面制备了乙烯基硅酸盐和环氧硅酸盐溶胶凝胶膜,测试膜在3%~5%NaCl,0.5mol/L Na2SO4及0.1 mol/L HCI溶液中的点蚀性能,并进行铜加速醋酸盐雾实验(Copperaccelerated salt spray,CASS),结果表明,裸铝表面发生严重的腐蚀,而涂敷溶胶—凝胶膜的铝合金表面没有出现点蚀。Furukawa等将聚硅氮烷溶液用于阳极氧化的铝材表面,干燥后烘烤,发现铝材表面的阳极氧化膜上存在硅酸盐膜。Shi等在60℃将多孔的氧化铝膜放入锌丁醇盐水溶液中,取出后在200℃下烘烤4h,研究了有序的氧化铝孔隙中ZnO纳米颗粒的光致发光谱。Kamada等在SiO2溶胶水溶液采中用溶胶—凝胶电泳沉积技术在铝基阳极氧化膜的纳米孔隙中沉积了SiO2纳米颗粒。研究发现,无需施加电场,悬浮液中的SiO2颗粒也能进入膜孔,这是因为颗粒所带电荷与阳极氧化膜的表面电荷不同。李澄等将SiO2溶胶用于铝阳极氧化膜的封闭,发现当SiO2溶胶颗粒与氧化膜骨架尺寸匹配时可获得优良的封闭效果,并指出SiO2溶胶是通过填充膜孔来实现封闭的。而用勃姆石(AlOOH)溶胶对阳极氧化膜进行封闭的研究尚未见报道。铝及铝合金的阳极氧化膜由定向排列的水合氧化铝凝胶微骨架构成,与制备纳米氧化铝的前驱体AlOOH溶胶的主要化学成分相同,二者有很好的相容性。因此,本文作者尝试将铝阳极氧化膜浸入勃姆石溶胶来封闭氧化膜的孔隙,以实现对铝及铝合金阳极氧化膜的无铬高耐蚀性封闭。
1 实验
1.1 实验材料及实验工艺
实验材料为2024铝合金(尺寸为4.5 cm×2.5 cm×0.2 cm),工艺流程如下:前处理→硫酸阳极氧化→流动冷水清洗→封闭→蒸馏水轻轻冲洗→吹干。阳极氧化工艺规范为:电解液H2SO4 180 g/L,Al2(SO4)312g/L;温度18~22℃,电流密度10 mA/cm2,时间30 min。
溶胶制备方法如下:将含有机磺酸盐的分散剂溶液加入Al(NO3)3(分析纯)溶液中,以氨水(分析纯)滴定Al(NO3)3溶液,边滴定边搅拌,同时调节溶液的pH值得到勃姆石溶胶,反应式为Al(NO3)3+3NH3·H2O→Al(OOH)+3NH4NO3+H2O。将2024铝合金硫酸阳极氧化后的试片垂直放入上述溶胶系统中、静置、取出、用蒸馏水轻轻冲洗后、干燥。
重铬酸钠封孔工艺参数如下:二水合重铬酸钠50~65 g·L-1,pH值5~6,温度90~99℃,时间15~25 min。
1.2 阳极氧化封闭膜的性能测试
封闭膜的表面密度(p)可表示为p=(m2~m1)/A
式中m1和m2分别为封闭前后试片的质量,A为试片表面积。
按照我国国标GB/T14952.1—94标准用磷—铬酸失重法检测阳极氧化膜的封孔质量。我国国标GB/T5237.2—2000规定:磷—铬酸质量损失△m≥3 g·m-2为封闭不合格,△m<3 g·m-2为封闭合格。按照SJ1276—77标准进行酸性点滴实验。点滴实验溶液为盐酸(p=1.19 g·cm-3)25 mL、重铬酸钾3 g、蒸馏水75mL,用彩色蜡笔在试片上画一个面积为1.0 cm2的圆,在圆中滴2~4滴实验溶液,记录封闭膜上染色液由橙色开始变为绿色所需的时间(min)。取一定量的茜素红(5~10 g·L-1)及冰醋酸(18%,质量分数)配制成红色染色液,将已经封闭干燥的阳极氧化2024铝合金试片,用水冲洗后,放入温度为60~70℃的红色染色液中染色10~15 min。染色后取出试片,用水洗净、干燥,观察试片表面颜色。用PARSTAT 2273电化学测试系统测定阳极氧化封闭膜在3.5% NaCI溶液中的电化学阻抗谱和腐蚀极化曲线,参比电极为饱和甘汞电极,辅助电极为铂电极,试样面积为1 cm2。电化学测试之前试样先浸入NaCl溶液中约0.5 h,使开路电位达到稳定。极化测试时的电位扫描速度为0.333 mV/s,电化学阻抗谱测试时的外加激励信号幅值为10 mV,频率范围为100 kHz~10 mHz。
2 结果与讨论
2.1 溶胶封闭法的正交实验
对2024Al表面阳极氧化膜勃姆石溶胶封闭工艺进行正交实验,浸入溶胶时间的三水平为:10、20和30 min;溶胶pH值的三水平为:4.5~5.5、6.5~7.5和8.5~9.5;封闭膜的烘干温度三水平为:60、80和100℃;烘干时间的三水平为:2、6和10 h。
表1所列为磷—铬酸质量损失、表面密度、酸性点滴实验、染色实验的正交实验的结果,综合4种性能的分析结果,对封闭膜性能的影响由强到弱的顺序为:烘干温度>烘干时间>pH值>封闭时间。
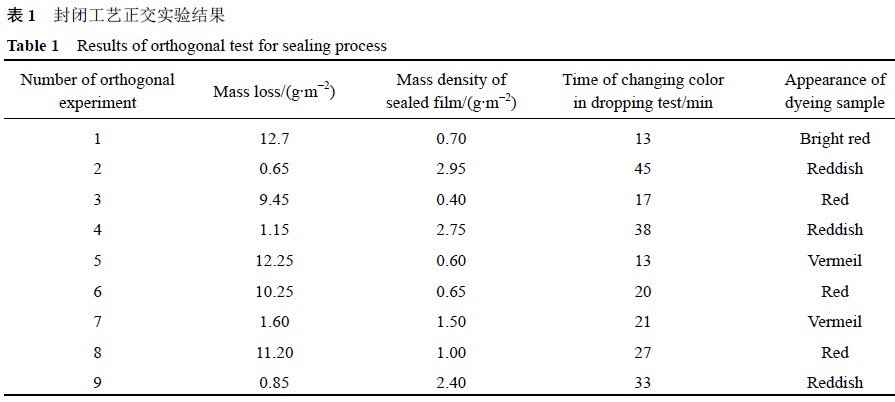
溶胶—凝胶法可以用来制备耐蚀涂层,该类涂层对提高基材的化学耐久性、防止氧化、控制腐蚀有显著的效果,有可能完全替代传统表面处理使用的毒性物质铬酸盐处理工艺。
Voevodin等在铝合金表面制备了乙烯基硅酸盐和环氧硅酸盐溶胶凝胶膜,测试膜在3%~5%NaCl,0.5mol/L Na2SO4及0.1 mol/L HCI溶液中的点蚀性能,并进行铜加速醋酸盐雾实验(Copperaccelerated salt spray,CASS),结果表明,裸铝表面发生严重的腐蚀,而涂敷溶胶—凝胶膜的铝合金表面没有出现点蚀。Furukawa等将聚硅氮烷溶液用于阳极氧化的铝材表面,干燥后烘烤,发现铝材表面的阳极氧化膜上存在硅酸盐膜。Shi等在60℃将多孔的氧化铝膜放入锌丁醇盐水溶液中,取出后在200℃下烘烤4h,研究了有序的氧化铝孔隙中ZnO纳米颗粒的光致发光谱。Kamada等在SiO2溶胶水溶液采中用溶胶—凝胶电泳沉积技术在铝基阳极氧化膜的纳米孔隙中沉积了SiO2纳米颗粒。研究发现,无需施加电场,悬浮液中的SiO2颗粒也能进入膜孔,这是因为颗粒所带电荷与阳极氧化膜的表面电荷不同。李澄等将SiO2溶胶用于铝阳极氧化膜的封闭,发现当SiO2溶胶颗粒与氧化膜骨架尺寸匹配时可获得优良的封闭效果,并指出SiO2溶胶是通过填充膜孔来实现封闭的。而用勃姆石(AlOOH)溶胶对阳极氧化膜进行封闭的研究尚未见报道。铝及铝合金的阳极氧化膜由定向排列的水合氧化铝凝胶微骨架构成,与制备纳米氧化铝的前驱体AlOOH溶胶的主要化学成分相同,二者有很好的相容性。因此,本文作者尝试将铝阳极氧化膜浸入勃姆石溶胶来封闭氧化膜的孔隙,以实现对铝及铝合金阳极氧化膜的无铬高耐蚀性封闭。
1 实验
1.1 实验材料及实验工艺
实验材料为2024铝合金(尺寸为4.5 cm×2.5 cm×0.2 cm),工艺流程如下:前处理→硫酸阳极氧化→流动冷水清洗→封闭→蒸馏水轻轻冲洗→吹干。阳极氧化工艺规范为:电解液H2SO4 180 g/L,Al2(SO4)312g/L;温度18~22℃,电流密度10 mA/cm2,时间30 min。
溶胶制备方法如下:将含有机磺酸盐的分散剂溶液加入Al(NO3)3(分析纯)溶液中,以氨水(分析纯)滴定Al(NO3)3溶液,边滴定边搅拌,同时调节溶液的pH值得到勃姆石溶胶,反应式为Al(NO3)3+3NH3·H2O→Al(OOH)+3NH4NO3+H2O。将2024铝合金硫酸阳极氧化后的试片垂直放入上述溶胶系统中、静置、取出、用蒸馏水轻轻冲洗后、干燥。
重铬酸钠封孔工艺参数如下:二水合重铬酸钠50~65 g·L-1,pH值5~6,温度90~99℃,时间15~25 min。
1.2 阳极氧化封闭膜的性能测试
封闭膜的表面密度(p)可表示为p=(m2~m1)/A
式中m1和m2分别为封闭前后试片的质量,A为试片表面积。
按照我国国标GB/T14952.1—94标准用磷—铬酸失重法检测阳极氧化膜的封孔质量。我国国标GB/T5237.2—2000规定:磷—铬酸质量损失△m≥3 g·m-2为封闭不合格,△m<3 g·m-2为封闭合格。按照SJ1276—77标准进行酸性点滴实验。点滴实验溶液为盐酸(p=1.19 g·cm-3)25 mL、重铬酸钾3 g、蒸馏水75mL,用彩色蜡笔在试片上画一个面积为1.0 cm2的圆,在圆中滴2~4滴实验溶液,记录封闭膜上染色液由橙色开始变为绿色所需的时间(min)。取一定量的茜素红(5~10 g·L-1)及冰醋酸(18%,质量分数)配制成红色染色液,将已经封闭干燥的阳极氧化2024铝合金试片,用水冲洗后,放入温度为60~70℃的红色染色液中染色10~15 min。染色后取出试片,用水洗净、干燥,观察试片表面颜色。用PARSTAT 2273电化学测试系统测定阳极氧化封闭膜在3.5% NaCI溶液中的电化学阻抗谱和腐蚀极化曲线,参比电极为饱和甘汞电极,辅助电极为铂电极,试样面积为1 cm2。电化学测试之前试样先浸入NaCl溶液中约0.5 h,使开路电位达到稳定。极化测试时的电位扫描速度为0.333 mV/s,电化学阻抗谱测试时的外加激励信号幅值为10 mV,频率范围为100 kHz~10 mHz。
2 结果与讨论
2.1 溶胶封闭法的正交实验
对2024Al表面阳极氧化膜勃姆石溶胶封闭工艺进行正交实验,浸入溶胶时间的三水平为:10、20和30 min;溶胶pH值的三水平为:4.5~5.5、6.5~7.5和8.5~9.5;封闭膜的烘干温度三水平为:60、80和100℃;烘干时间的三水平为:2、6和10 h。
表1所列为磷—铬酸质量损失、表面密度、酸性点滴实验、染色实验的正交实验的结果,综合4种性能的分析结果,对封闭膜性能的影响由强到弱的顺序为:烘干温度>烘干时间>pH值>封闭时间。
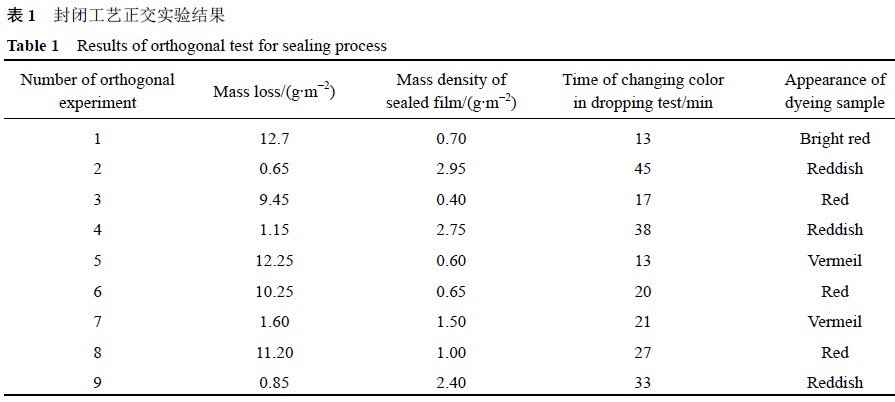
烘干温度为80℃的正交实验为2、4和9号,2、4和9号实验的试片做染色实验、酸性点滴实验的效果都很好,磷—铬酸质量损失满足国家标准要求,封闭膜的表面密度较大,进一步说明烘干温度这个因素对封闭膜的影响最大。酸性点滴实验变色时间为33~45min,满足2024Al合金的实际生产要求。
综合阳极氧化膜的酸浸质量损失量、表面密度、酸性点滴实验和染色实验的正交实验分析结果,得到溶胶封闭氧化膜的较佳工艺条件如下:氧化膜浸入溶胶的时间为30 min,溶胶封孔液的pH值为4.5-5.5,封闭后膜的烘干温度为80℃,烘干时间为6h。
2.2 浸入溶胶时间对封闭膜性能的影响
图1所示为在溶胶pH值为4~5,烘干温度为80℃,烘干时间为6h的条件下,研究试片浸入时间对封闭膜的表面密度和酸浸质量损失量的影响。
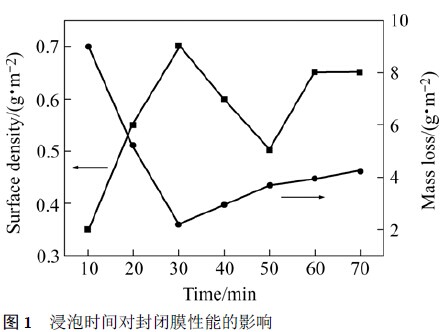
综合阳极氧化膜的酸浸质量损失量、表面密度、酸性点滴实验和染色实验的正交实验分析结果,得到溶胶封闭氧化膜的较佳工艺条件如下:氧化膜浸入溶胶的时间为30 min,溶胶封孔液的pH值为4.5-5.5,封闭后膜的烘干温度为80℃,烘干时间为6h。
2.2 浸入溶胶时间对封闭膜性能的影响
图1所示为在溶胶pH值为4~5,烘干温度为80℃,烘干时间为6h的条件下,研究试片浸入时间对封闭膜的表面密度和酸浸质量损失量的影响。
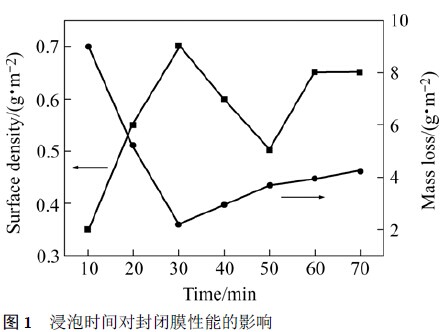
从图1可以看出,浸泡时间由10 min延长到30min后,封闭膜的表面密度明显增加,酸浸质量损失量明显降低,说明勃姆石胶粒渗入铝阳极氧化膜多孔层中的速度高于氧化膜溶解的速度。浸泡时间由30min延长到70 min后,封闭膜的表面密度开始下降,酸浸质量损失量略微升高,这是由于试片浸泡到30min时,溶胶往阳极氧化膜的微孔中渗透达到饱和,充满多孔层的孔隙,此时继续延长浸泡时间,由于溶液呈弱酸性会溶解阳极氧化膜,所以膜开始变得疏松,导致封闭膜的表面密度下降。因此应在浸泡30 min时取出氧化膜。
2.3 溶胶pH值对封闭膜性能的影响
图2所示为在试片浸入溶胶时间为30 min、膜烘干温度为80℃、烘干时间为6h的条件下,溶胶的pH值对封闭膜的表面密度和酸浸质量损失量的影响。
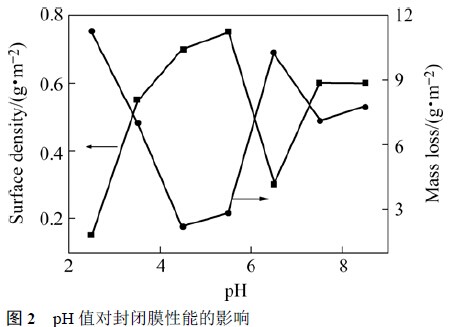
2.3 溶胶pH值对封闭膜性能的影响
图2所示为在试片浸入溶胶时间为30 min、膜烘干温度为80℃、烘干时间为6h的条件下,溶胶的pH值对封闭膜的表面密度和酸浸质量损失量的影响。
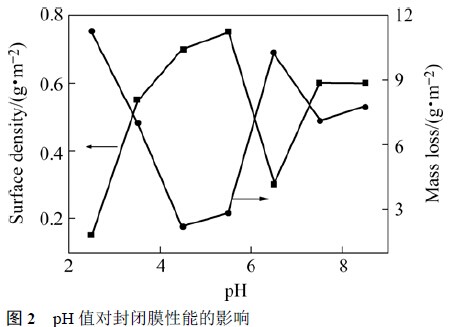
由图2可知,pH值在4.5~5.5之间封闭膜的表面密度最大,酸浸质量损失量最小。当溶胶pH在2.5~4.5范围时,随pH降低,酸度变大,则溶胶对氧化膜的溶解作用增强,导致膜的表面密度下降,酸浸质量损失量升高。pH值在6.5时,封闭膜的表面密度急剧降低,膜的质量损失急剧升高,这是由于pH值在4.5~5.5之间形成的溶胶具有流动性,当pH值在6.5时溶胶转变成不能流动的凝胶,凝胶状的胶体粒子不容易往阳极氧化膜的微孔里渗透。pH值高于6.5以后,凝胶开始变稀,随pH值升高逐渐变为溶胶,胶体粒子的渗入速度又开始加快,所以封闭膜的表面密度开始上升,膜的质量损失下降。由图2可见,封闭氧化膜多孔层时溶胶的pH值应保持在4.5~5.5的范围。
2.4 封闭膜的极化曲线和电化学阻抗谱
图3(a)所示为溶胶封闭和传统重铬酸钠封闭的2024Al阳极氧化膜腐蚀极化曲线,以阴极极化曲线的塔菲尔区外推到与自腐蚀电位的水平线相交,该交点对应的电流密度为金属的腐蚀电流密度。按照上述方法计算得到重铬酸钠封闭膜的腐蚀电流密度为5.0×10-7 A/cm2,腐蚀电位为–0.57 V;溶胶封闭膜的腐蚀电流密度为3.7×10-9 A/cm2,腐蚀电位为–0.52 V。溶胶封闭膜的腐蚀电位较重铬酸钠封闭膜的腐蚀电位稍有提高,但其腐蚀电流密度却比重铬酸钠封闭膜的大约降低2个数量级。这表明溶胶封闭膜的耐蚀性显著高于重铬酸钠封闭膜的。图3(b)所示为上述封闭膜的电化学阻抗谱。由图可见,在整个频率范围内,溶胶封闭膜的阻抗值均明显高于重铬酸盐封闭膜的;在最低频处,重铬酸盐封闭膜的阻抗已达到极大值,而溶胶封闭膜的阻抗值仍在继续增加;如在0.01 Hz处,重铬酸钠封闭膜的∣Z∣=8.4×104Ω,溶胶封闭膜的∣Z∣=6.9×106 Ω;阻抗测试结果进一步表明溶胶封闭膜的耐蚀性远高于重铬酸钠封闭膜的。
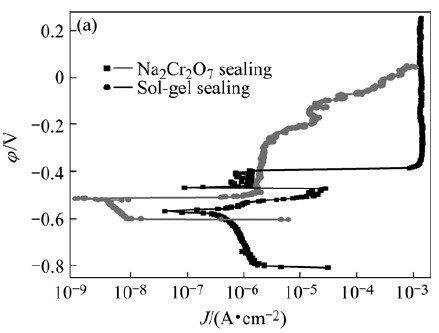
2.4 封闭膜的极化曲线和电化学阻抗谱
图3(a)所示为溶胶封闭和传统重铬酸钠封闭的2024Al阳极氧化膜腐蚀极化曲线,以阴极极化曲线的塔菲尔区外推到与自腐蚀电位的水平线相交,该交点对应的电流密度为金属的腐蚀电流密度。按照上述方法计算得到重铬酸钠封闭膜的腐蚀电流密度为5.0×10-7 A/cm2,腐蚀电位为–0.57 V;溶胶封闭膜的腐蚀电流密度为3.7×10-9 A/cm2,腐蚀电位为–0.52 V。溶胶封闭膜的腐蚀电位较重铬酸钠封闭膜的腐蚀电位稍有提高,但其腐蚀电流密度却比重铬酸钠封闭膜的大约降低2个数量级。这表明溶胶封闭膜的耐蚀性显著高于重铬酸钠封闭膜的。图3(b)所示为上述封闭膜的电化学阻抗谱。由图可见,在整个频率范围内,溶胶封闭膜的阻抗值均明显高于重铬酸盐封闭膜的;在最低频处,重铬酸盐封闭膜的阻抗已达到极大值,而溶胶封闭膜的阻抗值仍在继续增加;如在0.01 Hz处,重铬酸钠封闭膜的∣Z∣=8.4×104Ω,溶胶封闭膜的∣Z∣=6.9×106 Ω;阻抗测试结果进一步表明溶胶封闭膜的耐蚀性远高于重铬酸钠封闭膜的。
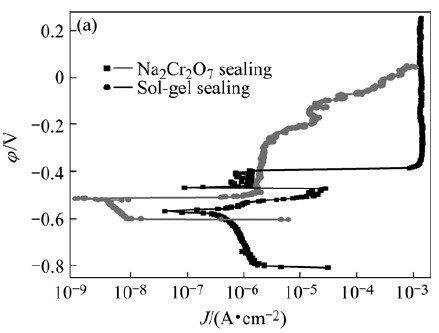
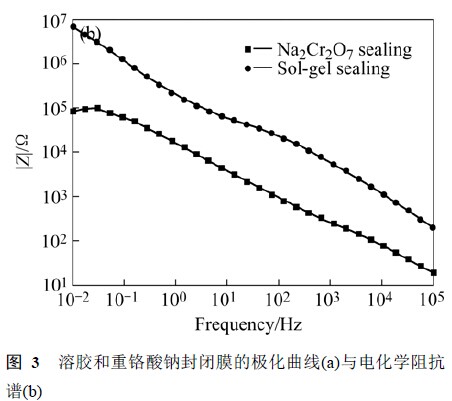
2.5 溶胶封闭膜的耐蚀机理
图4(a)和(b)所示分别为未封孔和溶胶封闭铝阳极氧化膜的表面形貌。铝的阳极氧化膜由定向排列的水合氧化铝凝胶微骨架构成。微胞直径约为300 nm,微胞间存在垂直于表面的孔隙,2024铝合金氧化膜的孔隙近似为圆形,直径约为10~30nm。采用勃姆石溶胶封闭氧化膜时,主要是利用勃姆石溶胶渗入铝阳极氧化膜的孔隙中,其中的胶粒填塞孔洞和覆盖孔口来实现的,封闭后的氧化膜经过烘干能达到较好的耐蚀效果。溶胶中的较小颗粒可进入膜孔层内部,而由小颗粒聚集而成的大颗粒则覆盖于氧化膜表面上,形成耐蚀性较强的溶胶—凝胶涂层(见图4(b))。小颗粒形成的凝胶层较薄,大颗粒形成的凝胶层较厚,由于溶胶中液体量大,干燥时产生收缩,所以溶胶凝胶涂层表面呈现龟裂状。铝阳极氧化膜表面上的溶胶—凝胶涂层能谱分析表明,涂层的组成如下(质量分数):C12.890%,N 10.495%,0 46.841%, Al 26.439%和S3.335%。这说明涂层中有溶胶中AlOOH、NH4NO3和起分散剂作用的有机磺酸盐表面活性剂R-S03Na化合物中的元素存在,证实溶胶在氧化膜表面形成凝胶涂层。
图4(a)和(b)所示分别为未封孔和溶胶封闭铝阳极氧化膜的表面形貌。铝的阳极氧化膜由定向排列的水合氧化铝凝胶微骨架构成。微胞直径约为300 nm,微胞间存在垂直于表面的孔隙,2024铝合金氧化膜的孔隙近似为圆形,直径约为10~30nm。采用勃姆石溶胶封闭氧化膜时,主要是利用勃姆石溶胶渗入铝阳极氧化膜的孔隙中,其中的胶粒填塞孔洞和覆盖孔口来实现的,封闭后的氧化膜经过烘干能达到较好的耐蚀效果。溶胶中的较小颗粒可进入膜孔层内部,而由小颗粒聚集而成的大颗粒则覆盖于氧化膜表面上,形成耐蚀性较强的溶胶—凝胶涂层(见图4(b))。小颗粒形成的凝胶层较薄,大颗粒形成的凝胶层较厚,由于溶胶中液体量大,干燥时产生收缩,所以溶胶凝胶涂层表面呈现龟裂状。铝阳极氧化膜表面上的溶胶—凝胶涂层能谱分析表明,涂层的组成如下(质量分数):C12.890%,N 10.495%,0 46.841%, Al 26.439%和S3.335%。这说明涂层中有溶胶中AlOOH、NH4NO3和起分散剂作用的有机磺酸盐表面活性剂R-S03Na化合物中的元素存在,证实溶胶在氧化膜表面形成凝胶涂层。
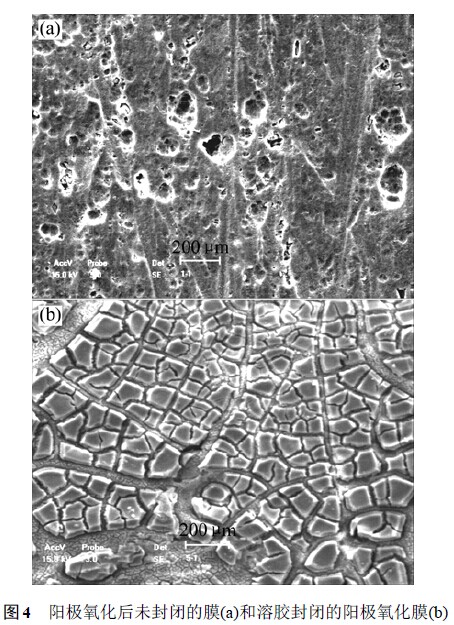
由于氧化膜的成分和溶胶的主要成分相同,所以二者相容性好,很容易融为一个整体,牢固地结合在一起,经过烘干固化后可进一步提高膜层的耐蚀性,并且铝氧化膜和溶胶烘干后的干凝胶的热膨胀系数基本相似,封孔物质不会发生脱落。阳极氧化膜的多孔层不仅被溶胶封闭而且在氧化膜的表面覆盖有溶胶凝胶涂层,这两种效果极大地促进了溶胶封孔膜的耐蚀性。
3 结论
1)正交实验得出溶胶封闭2024铝合金氧化膜的较优工艺条件为:试片浸入溶胶时间30 min,溶胶pH值4.5~5.5,封闭膜烘干温度80℃,烘干时间6h。
2)勃姆石溶胶在渗入阳极氧化膜多孔层中的同时,膜层也发生化学溶解。当试片浸入时间为30 min时膜表面密度最高,磷—铬酸质量损失最小。
3)勃姆石溶胶在pH值4.5~5.5之间时封闭膜的表面密度较大,封闭质量达到合格。若pH值提高到6.5时,溶胶发生凝胶化,封闭质量下降。
4)溶胶法封闭膜的耐蚀性高于传统的重铬酸钠封闭膜的耐蚀性。耐蚀性的提高是由于勃姆石溶胶不仅封闭了多孔层的孔隙,而且在氧化膜上形成溶胶凝胶涂层。
上一篇: 铝常温镍盐封孔剂的试验研究
下一篇: 铝合金阳极氧化膜的封闭方法