硫酸铈对铝合金阳极氧化膜耐蚀性的影响
硫酸铈对铝合金阳极氧化膜耐蚀性的影响
孙衍乐 宣天鹏 许少楠 张敏
(合肥工业大学材料科学与工程学院,安徽 合肥230009)
(合肥工业大学材料科学与工程学院,安徽 合肥230009)
摘要:通过正交试验确定铝合金硼酸和硫酸电解液阳极氧化的最佳电压、时间和温度,分别在基础配方溶液中添加不同含量的硫酸铈,对所制的样品氧化膜进行盐雾和浸泡耐蚀性测试,采用测量极化曲线的方法求出了φcorr和Jcorr确定硫酸钸的最佳添加量。
引言
铝合金经硼酸和硫酸电解液阳极氧化得到的氧化膜膜层致密,孔隙率低,具有很好的耐蚀性,且氧化处理后不会降低工件的疲劳强度,可满足工件高精度和低粗糙度的要求。相比铬酸电解液阳极氧化,硼酸和硫酸电解液阳极氧化工艺还具有环境友好、不含Cr(船)、槽液成分浓度低、槽液处理方便、氧化电压低、氧化时间短等优点,氧化膜具有良好的吸附性,容易染上各种颜色,因此,铝合金的硼酸和硫酸电解液阳极氧化在航空、交通等行业中有着广阔的应用前景。
1 实验材料与方法
1.1 实验材料及设备
实验材料:2cm×2cm×1mm 6063铝合金样品,2cm×2cm不锈钢阴极。
实验仪器:分析天平、YWX/F-250E型盐雾试验箱、DF1700S(单路)10~20A直流稳压电源、CHI600B型电化学工作站。
1.2 氧化膜制备工艺流程
工艺流程:工件→丙酮除油(室温)→去离子水洗→去氧化皮→去离子水洗→化学抛光→去离子水洗→硝酸出光→去离子水洗(无水乙醇中保存)→阳极氧化→沸水封闭。
化学抛光是阳极氧化前预处理阶段中最为关键的一步,抛光液由V(磷酸):V(硫酸):V(销酸)=5:4:1配成混合酸溶液,处理过程中温度、时间要严格控制,温度过低或时间太短会导致样品表面不够光亮,温度过高样品局部表面容易烧伤,时间太长则会使样品表面出现一些平行条纹,导致样品表面不平滑,影响阳极氧化的质量。
1.3 基础电解液
经正交试验得基础电解液成分:0.8%硼酸,4.5%硫酸,p(添加剂)为4g/L,p(硫酸镍)为8g/L。膜的厚度、质量影响主要的是硫酸的含量,硼酸主要是影响膜的阻挡层和多孔层的结构,使膜更加致密,耐蚀性更高,对膜层重量无重大影响。
1.4 腐蚀试验
电解液中分别添加0.2、0.4、0.6、0.8及1.0 g/L硫酸铈,试片经阳极氧化后分别经沸水封闭和不封闭。
将沸水封闭及不封闭的试片连续喷雾(5% NaCl溶液)336、408、480、528、576及624h,每次达到设定时间,将试样表面腐蚀产物清洗干净,吹干称量,得出质量损失曲线;室温下,将试样在3%的NaCl溶液中浸泡72、144、216、288、360、384、408及432h,同样方法得到质量损失曲线。
1.5 电化学测试
阳极氧化的试片:基础电解液中分别添加0.2、0.4、0.6、0.8及1.Og/L的硫酸铈,阳极氧化的试片经封闭处理后,用指甲油绝缘,暴露出2mm×2mm的氧化膜为工作电极。辅助电极为铂电极,参比电极为甘汞电极,在3%
NaCl溶液中测量极化曲线。
测定极化曲线的υ扫描为2mV/s。
2 结果与讨论
2.1 腐蚀试验
2.1.1 盐雾试验
氧化膜喷雾时间与质量损失之间的关系如图1、图2。其中曲线1~6分别为p(硫酸铈)0.2、0.4、0.6、0.8、1.0g/L及基础电解液的试验结果。
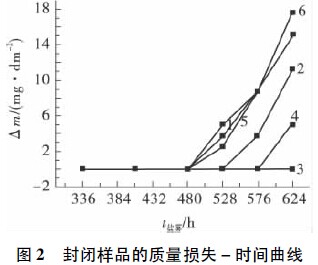
1.2 氧化膜制备工艺流程
工艺流程:工件→丙酮除油(室温)→去离子水洗→去氧化皮→去离子水洗→化学抛光→去离子水洗→硝酸出光→去离子水洗(无水乙醇中保存)→阳极氧化→沸水封闭。
化学抛光是阳极氧化前预处理阶段中最为关键的一步,抛光液由V(磷酸):V(硫酸):V(销酸)=5:4:1配成混合酸溶液,处理过程中温度、时间要严格控制,温度过低或时间太短会导致样品表面不够光亮,温度过高样品局部表面容易烧伤,时间太长则会使样品表面出现一些平行条纹,导致样品表面不平滑,影响阳极氧化的质量。
1.3 基础电解液
经正交试验得基础电解液成分:0.8%硼酸,4.5%硫酸,p(添加剂)为4g/L,p(硫酸镍)为8g/L。膜的厚度、质量影响主要的是硫酸的含量,硼酸主要是影响膜的阻挡层和多孔层的结构,使膜更加致密,耐蚀性更高,对膜层重量无重大影响。
1.4 腐蚀试验
电解液中分别添加0.2、0.4、0.6、0.8及1.0 g/L硫酸铈,试片经阳极氧化后分别经沸水封闭和不封闭。
将沸水封闭及不封闭的试片连续喷雾(5% NaCl溶液)336、408、480、528、576及624h,每次达到设定时间,将试样表面腐蚀产物清洗干净,吹干称量,得出质量损失曲线;室温下,将试样在3%的NaCl溶液中浸泡72、144、216、288、360、384、408及432h,同样方法得到质量损失曲线。
1.5 电化学测试
阳极氧化的试片:基础电解液中分别添加0.2、0.4、0.6、0.8及1.Og/L的硫酸铈,阳极氧化的试片经封闭处理后,用指甲油绝缘,暴露出2mm×2mm的氧化膜为工作电极。辅助电极为铂电极,参比电极为甘汞电极,在3%
NaCl溶液中测量极化曲线。
测定极化曲线的υ扫描为2mV/s。
2 结果与讨论
2.1 腐蚀试验
2.1.1 盐雾试验
氧化膜喷雾时间与质量损失之间的关系如图1、图2。其中曲线1~6分别为p(硫酸铈)0.2、0.4、0.6、0.8、1.0g/L及基础电解液的试验结果。
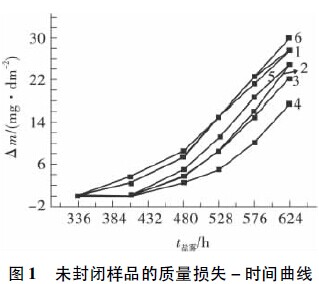
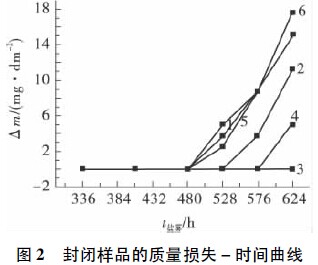
阳极氧化膜具有一定厚度,刚开始在盐雾中发生腐蚀时,氧化膜虽发生腐蚀,但并没有被腐蚀穿透,仍然对铝基体有很好的保护作用;当某处氧化膜被腐蚀穿透时,氧化膜失去对基体的保护作用,持续喷雾,测定出氧化膜被腐蚀穿透的时间可以作为对比衡量氧化膜的抗腐蚀性的一个标准。由图2可知,在528h前随盐雾时间的增加,封闭处理的各样品的质量损失均有不同程度的增加,576h后添加0.4g/L硫酸铈电解液所得样品质量损失率升高较快。一定腐蚀时间内,沸水封闭的阳极氧化膜具有很好的耐蚀性能,当超过该腐蚀极限时,由于氧化膜表面不够均匀,可能造成样品氧化膜的局部脱落,p(硫酸铈)为0.6g/L时所得氧化膜经封闭处理后的耐蚀性能最好。稀土金属离子,在阳极氧化过程中对某些中间反应起到类似于催化剂的作用,它能加快其反应速度,使成膜速度加快,使其结构发生了显著的变化:阻挡层厚度有所增加,多孔部分结构更为致密,这些结构的变化有利于阳极氧化膜耐蚀性能的提高。但稀土超过临界值后氧化膜各种性能下降的原因有待再研究。
对照图1和图2中6组曲线,沸水封闭处理能大大提高阳极氧化膜的耐蚀性。经封闭处理的样品在480h前均未发生腐蚀,未经封闭处理的样品在盐雾时间进行到480h时,都已发生严重腐蚀;经封闭处理后,样品的腐蚀速率也会降低很多。未经封闭的氧化膜样品孔洞都是张开的,在腐蚀介质中,侵蚀离子很容易进入孔洞,孔壁腐蚀的同时,直接到达里面的阻挡层,由于阻挡层很薄,在较短时间内阳极氧化膜被腐蚀;硼酸和硫酸阳极氧化膜多孔层孔洞壁上无水、在沸水封闭时无定型的Al3O2与沸水结合生成含水的、结晶态γ水铝石而体积膨胀,孔隙由于氧化膜的膨胀而封闭,侵蚀离子进入到孔隙变得困难,从而增加了工件的抗蚀能力。
2.1.2 浸泡试验
图3和图4为未封闭样品和封闭样品在pH=7,3% NaCl溶液中的浸泡质量损失曲线。其中曲线1~6p(硫酸铈)分别为0.2、0.4、0.6、0.8及1.0 g/L及基础电解液的试验结果。
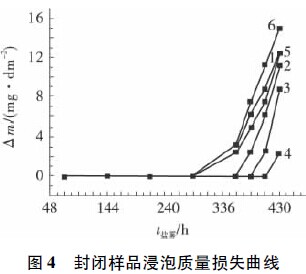
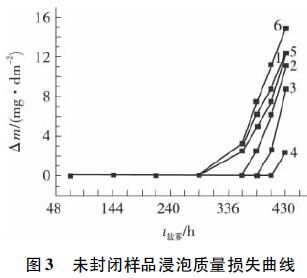
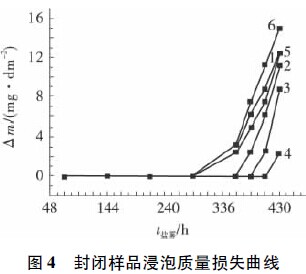
对照图3和4中6组数据可以得出,氧化膜经沸水封闭后,耐蚀性显著提高;基础电镀液中p(硫酸铈)为0.6和0.8g/L时,样品氧化膜耐蚀性最好。浸泡试验得到的结果与盐雾试验分析结果吻合。
2.2 极化曲线的测定
添加不同质量浓度硫酸铈电解液中制得的氧化膜在3% NaCl溶液的极化曲线如图5,其中曲线1~5p(硫酸铈)分别为0.2、0.4、0.6、0.8及1.0g/L时的试验结果。
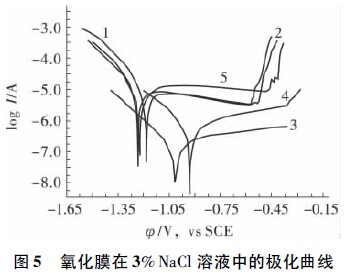
由图5可得出不同硫酸铈质量浓度镀液所得氧化膜的φcorr和Jcorr,其数据见表1。
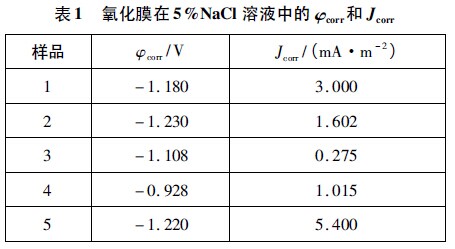
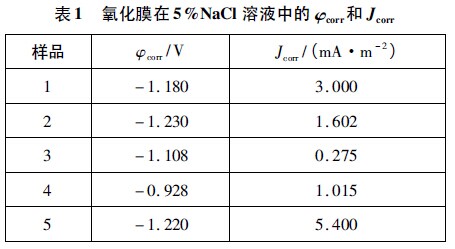
p(硫酸铈)为0.2、0.4及1.0g/L时,样品氧化膜的腐蚀电位、腐蚀电流密度相差较小,氧化膜的耐蚀性能差别不大。当p(硫酸铈)为0.6g/L时,样品的腐蚀电位明显正移,腐蚀电流密度在所有样品中最小,极化度也明显增大,耐蚀性较好。当p(硫酸铈)为0.8g/L时,腐蚀电位最正,腐蚀电流较小p(硫酸铈)为0.6及0.8g/L时,所得样品的耐蚀性最好。稀土硫酸铈添加不会对膜层的厚度产生影响,即稀土不会在氧化膜表面沉积,但会对膜层结构产生影响,使阻挡层变厚,样品耐蚀性提高;当硫酸铈添加量超过一定临界值时会使膜层的性能下降。
3 结论
硼酸和硫酸阳极氧化膜经沸水封闭处理后,多孔层上孔洞由于高温水合作用封闭,抑制了侵蚀性离子的进入,能大大提高氧化膜的耐蚀性;添加硫酸铈能够明显改善氧化膜的耐蚀性,稀土金属离子,使成膜速度加快,从而使其结构发生了显著的变化:阻挡层厚度有所增加,多孔部分结构更为致密,这些结构的变化有利于阳极氧化膜耐蚀性能的提高,当电解液中添加0.6或0. 8g/L硫酸铈时,生成氧化膜耐蚀性好。
上一篇: 几种稀土盐封闭的铝阳极氧化试样的腐蚀行为
下一篇: 铝常温镍盐封孔剂的试验研究