铝合金电化学抛光工艺
铝合金电化学抛光工艺
胡拥军 秦毅红 熊文高
(湖南城市学院化学与环境工程系,湖南益阳413049 中南大学冶金物化研究所,湖南长沙410000)
(湖南城市学院化学与环境工程系,湖南益阳413049 中南大学冶金物化研究所,湖南长沙410000)
摘要:采用综合评价方法研究了铝合金电化学抛光添加剂,结果发现,在碱性溶液中加入PEG作光亮剂可明显改善抛光效果,加入酒石酸钠等作稳定剂可延长溶液使用周期,并在此基础上优化了抛光工艺条件。试验表明,采用此工艺来抛光铝材获得的综合效果优于酸性电化学抛光和传统碱性电化学抛光,是一项有应用前景的新工艺。
引言
铝和铝合金性能优良、应用广泛,为提高其综合性能,须进行抛光处理。在各种抛光方法中,电化学抛光效果最佳。国内目前运用最多的电化学抛光法为磷酸、硫酸和铬酸法。由于其溶液毒性重、生产成本高,欧美等发达国家己基本采用无铬法替代。近年来,国内有少数企业也研制了类似工艺,但该法所用溶液主要成分仍为昂贵的磷酸,应用有限。
通过寻找合适添加剂,研究开发了用碱性溶液进行铝材抛光的工艺。
1 试验
将纯度为99.2%的工业纯铝裁成片,经机械抛光和化学除油后,以不锈钢为辅助电极控制各工艺参数进行抛光,然后水洗、干燥、检测质量。
根据生产需要,从以下方面评价抛光效果:①铝材表面整平度:以银镜对光反射率为100%作参比,用光电管测量抛光后铝材表面对光反射率表示整平程度,反射率越高则整平越好;(2)铝材单位面积溶解量:达到相同整平度时,单位面积溶解金属量小则整平快、效率高;(3)抛光溶液使用周期:以抛光效果明显下降时溶液中铝离子浓度表示,铝离子浓度高时该溶液仍能进行抛光说明其使用周期长;(4)抛光成本:包括溶液成本、能耗和废水处理成本等;(5)操作环境。
2 结果与讨论
2.1 添加剂的选择
在碱性溶液中不加光亮剂进行抛光时,铝表面明显浸蚀,呈灰色,且无整平效果。在NaOH溶液中尝试了多类物质后发现,在酸性电抛光时起作用的缓蚀剂、氧化剂及能增加溶液粘度的物质在碱性电化学抛光时并不能明显改善抛光效果,见表1(其中CMC为羧甲基纤维素;PEG为聚乙二醇)。从表中可知,能作光亮剂的物质有一共同点,即分子中含多个能在金属表面强烈吸附的基团,如羟基。根据钝化膜理论,这些物质在电压达阳极钝化电位时,可在阳极表面产生一层吸附膜,从而促使阳极钝化膜完整,抑制腐蚀,产生光泽。同时,由于该吸附膜在阳极凹陷处比凸起处厚,因而凸起处电流大、溶解快;凹陷处电流小、溶解慢。从而可提高整平效果。铝材在碱性溶液中溶解快,若不加光亮剂则阳极表面钝化膜不完整,从而使铝材浸蚀严重,无抛光效果。
表1 不同物质对抛光效果的影响

试验还发现,这些物质的加入还能将操作温度从传统碱性Brytal法的80℃降低到50℃。这可能是因为在抛光时,铝的溶解使扩散层中铝离子浓度达到饱和,从而析出Al(OH)3细小颗粒。只有提高温度才能减少Al(OH)3的析出,提高抛光效果。而PEG能在铝表面产生一层有机吸附膜,阻止Al(OH)3在铝表面的附着,从而在较低操作温度时仍能产生好的抛光效果。经过比较,选用效果最佳的PEG作光亮剂。
但采用上述溶液抛光时,溶液使用周期较短。当铝离子浓度达15~20 g/L时,铝材表面开始产生毛刺。为此选择酒石酸钠和葡萄糖酸钠作稳定剂进行试验,结果见表2。
表2 稳定剂对溶液使用周期的影响
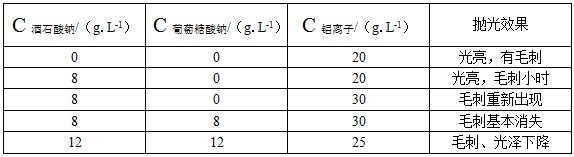
由表可见,酒石酸钠和葡萄糖酸钠能一定程度地延长溶液使用周期。原因可能是其具有较强的络合作用,同时含有仲醇羟基,能抑制Al(OH)3晶核的出现,从而消除毛刺,改善抛光效果。
由试验可知,稳定剂浓度过高会使抛光铝材表面光泽下降,且溶液中铝离子浓度达到35 g/L以上时,通过添加稳定剂也无法解决问题。因此,酒石酸钠和葡萄糖酸钠的含量均控制为8 g/L。
2.2 工艺条件
先通过正交试验确定效果较好时的抛光工艺条件:NaOH 18 g/L、Na2CO3 30 g/L、PEG 25 mL/L、酒石酸钠和葡萄糖酸钠各8 g/L,电压6.5V,电流20 A/dm2,温度50℃,然后固定其他条件而改变某一条件进行试验(主要因素为PEG浓度、电压和电流密度)。
(1)PEG含量PEG对抛光的影响见图1。当PEG浓度低于5 mL/L时,抛光效果较差;浓度超过35mL/L,抛光表面又易“烧焦”。原因可能是PEG浓度小,阳极表面的氧化膜不完整,铝表面易产生腐蚀斑点,抛光效果差;浓度过大,反应放出热量难以散发,故表面被烧焦。试验表明,PEG浓度控制为28 mL/L时效果最佳。
(2)操作电压改变操作电压所得试验结果见图2。电压低于5.5 V时,抛光效果急剧下降,铝表面无金属光泽。这是因为电压太低,阳极未达到钝化电位,同时阳极对光亮剂吸附能力弱,导致铝表面钝化膜不完整,出现浸蚀。但电压高于8V,抛光表面又由光亮向灰色转变,因此,抛光电压范围6.5~7.0V。
(3)电流密度 电流对抛光的影响见图3。由试验可知,电流密度小,整平速度慢、工作效率低,且阳极表面呈灰色;电流密度过高,可能阳极表面氧化膜因溶解过快而不完整,铝表面又出现浸蚀。因此,适宜的电流密度范围为20~30 A/dm2。
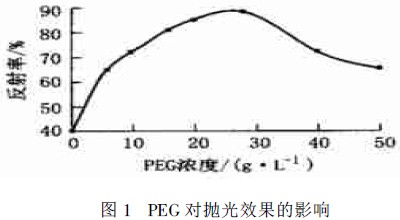
通过寻找合适添加剂,研究开发了用碱性溶液进行铝材抛光的工艺。
1 试验
将纯度为99.2%的工业纯铝裁成片,经机械抛光和化学除油后,以不锈钢为辅助电极控制各工艺参数进行抛光,然后水洗、干燥、检测质量。
根据生产需要,从以下方面评价抛光效果:①铝材表面整平度:以银镜对光反射率为100%作参比,用光电管测量抛光后铝材表面对光反射率表示整平程度,反射率越高则整平越好;(2)铝材单位面积溶解量:达到相同整平度时,单位面积溶解金属量小则整平快、效率高;(3)抛光溶液使用周期:以抛光效果明显下降时溶液中铝离子浓度表示,铝离子浓度高时该溶液仍能进行抛光说明其使用周期长;(4)抛光成本:包括溶液成本、能耗和废水处理成本等;(5)操作环境。
2 结果与讨论
2.1 添加剂的选择
在碱性溶液中不加光亮剂进行抛光时,铝表面明显浸蚀,呈灰色,且无整平效果。在NaOH溶液中尝试了多类物质后发现,在酸性电抛光时起作用的缓蚀剂、氧化剂及能增加溶液粘度的物质在碱性电化学抛光时并不能明显改善抛光效果,见表1(其中CMC为羧甲基纤维素;PEG为聚乙二醇)。从表中可知,能作光亮剂的物质有一共同点,即分子中含多个能在金属表面强烈吸附的基团,如羟基。根据钝化膜理论,这些物质在电压达阳极钝化电位时,可在阳极表面产生一层吸附膜,从而促使阳极钝化膜完整,抑制腐蚀,产生光泽。同时,由于该吸附膜在阳极凹陷处比凸起处厚,因而凸起处电流大、溶解快;凹陷处电流小、溶解慢。从而可提高整平效果。铝材在碱性溶液中溶解快,若不加光亮剂则阳极表面钝化膜不完整,从而使铝材浸蚀严重,无抛光效果。
表1 不同物质对抛光效果的影响

试验还发现,这些物质的加入还能将操作温度从传统碱性Brytal法的80℃降低到50℃。这可能是因为在抛光时,铝的溶解使扩散层中铝离子浓度达到饱和,从而析出Al(OH)3细小颗粒。只有提高温度才能减少Al(OH)3的析出,提高抛光效果。而PEG能在铝表面产生一层有机吸附膜,阻止Al(OH)3在铝表面的附着,从而在较低操作温度时仍能产生好的抛光效果。经过比较,选用效果最佳的PEG作光亮剂。
但采用上述溶液抛光时,溶液使用周期较短。当铝离子浓度达15~20 g/L时,铝材表面开始产生毛刺。为此选择酒石酸钠和葡萄糖酸钠作稳定剂进行试验,结果见表2。
表2 稳定剂对溶液使用周期的影响
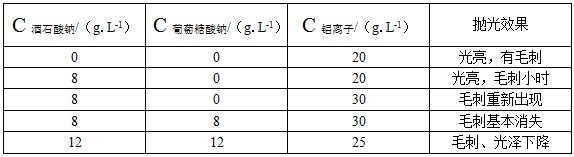
由表可见,酒石酸钠和葡萄糖酸钠能一定程度地延长溶液使用周期。原因可能是其具有较强的络合作用,同时含有仲醇羟基,能抑制Al(OH)3晶核的出现,从而消除毛刺,改善抛光效果。
由试验可知,稳定剂浓度过高会使抛光铝材表面光泽下降,且溶液中铝离子浓度达到35 g/L以上时,通过添加稳定剂也无法解决问题。因此,酒石酸钠和葡萄糖酸钠的含量均控制为8 g/L。
2.2 工艺条件
先通过正交试验确定效果较好时的抛光工艺条件:NaOH 18 g/L、Na2CO3 30 g/L、PEG 25 mL/L、酒石酸钠和葡萄糖酸钠各8 g/L,电压6.5V,电流20 A/dm2,温度50℃,然后固定其他条件而改变某一条件进行试验(主要因素为PEG浓度、电压和电流密度)。
(1)PEG含量PEG对抛光的影响见图1。当PEG浓度低于5 mL/L时,抛光效果较差;浓度超过35mL/L,抛光表面又易“烧焦”。原因可能是PEG浓度小,阳极表面的氧化膜不完整,铝表面易产生腐蚀斑点,抛光效果差;浓度过大,反应放出热量难以散发,故表面被烧焦。试验表明,PEG浓度控制为28 mL/L时效果最佳。
(2)操作电压改变操作电压所得试验结果见图2。电压低于5.5 V时,抛光效果急剧下降,铝表面无金属光泽。这是因为电压太低,阳极未达到钝化电位,同时阳极对光亮剂吸附能力弱,导致铝表面钝化膜不完整,出现浸蚀。但电压高于8V,抛光表面又由光亮向灰色转变,因此,抛光电压范围6.5~7.0V。
(3)电流密度 电流对抛光的影响见图3。由试验可知,电流密度小,整平速度慢、工作效率低,且阳极表面呈灰色;电流密度过高,可能阳极表面氧化膜因溶解过快而不完整,铝表面又出现浸蚀。因此,适宜的电流密度范围为20~30 A/dm2。
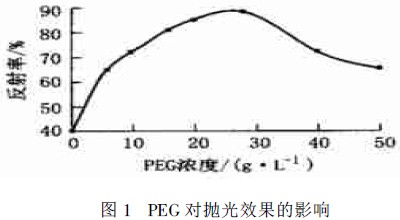
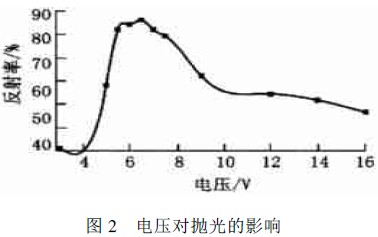

最后在此基础上作了综合试验,工艺条件为:NaOH 16 g/L。PEG 28 mL/L,Na2CO3 30 g/L,酒石酸钠8 g/L,葡萄糖酸钠8 g/L,电流密度25 A/dm2,操作电压6.5 V,温度50℃,抛光时间15 min。抛光后铝材表面反射率为87%、铝材损耗为0.0174 g/cm2、溶液中A13+浓度为30 g/L时,抛光后铝表面反射率仍可达81%。综合比较抛光效果、操作环境、能耗、溶液使用寿命、铝材损耗和生产成本等,此方法与酸性电化学抛光法和经典碱性电化学抛光法(Brytal法)相比都有较大的优点(采用Brytal法时,操作温度为82℃,电压10~12V,抛光时间30 min,获得的反射率88%,铝材损耗为0. 0216 g/cm2,且A13+达到20 g/L就不能进行抛光)。
3 结论
(1)选用PEG作光亮剂可以明显改善整平效果,加快抛光速度;
(2)加入合适稳定剂可以延长抛光溶液使用周期;
(3)试验获得了最佳工艺条件,其溶液组成为:PEG 28 mL/L、Na2CO3 30 g/L、酒石酸钠8 g/L、葡萄糖酸钠8 g/L,操作电压6.5V。电流密度25 A/dm2;
(4)采用上述工艺对铝材抛光获得的表面反射率高、操作温度低、工作环境好、铝材损耗小、生产成本低,综合效果优于酸性电化学抛光和碱性Brytal抛光。
上一篇: 铝的低成本化学抛光液
下一篇: 铝合金电化学抛光工艺现状