铝及铝合金酸性脱脂工艺研究
铝及铝合金酸性脱脂工艺研究
武汉材料保护研究所(430030) 毕艳 谢蕴丹 李捷 李鑫庆
摘要:研究了铝及铝合金在室温条件下的脱脂工艺,槽液以15%的硫酸为主,加入少量的高价金属离子、氧化剂、表面活性剂等,脱脂效率高,槽液成本低,寿命长,对不锈钢设备腐蚀小。
1前言
铝及铝合金的除油。早期是延用钢铁的除油工艺。即槽液为Na2CO3、Na2SiO3、Na3PO4溶液,操作温度40~70℃,时间5~15 min,这种工艺性能稳定,寿命长,但槽液成本高,不易洗净,现己基本不用。60年代,人们采用NaOH或Na2CO3添加Na3PO4、络合剂、非离子表面活性剂、阴离子表面活性剂在室温下脱脂,时间3~5 min,除油效率高,成本低,节能,但槽液易产生絮状沉淀,络合剂、表面活性剂易带入后续槽形成污染,目前仅有少数厂仍在使用。从80年代开始,酸性脱脂逐步普及,槽液为H2SO4或H3PO4加入HF、Fe3+、H2O2、NO2-和非离子表面活性剂,室温下操作,时间为3~5 min。这种工艺效率高,不污染后续槽,是较好的脱脂工艺。现在应用越来越广泛。
本研究以硫酸为基液,加特制的脱脂剂,在室温条件下,勿需机械搅拌等辅助,即可获得良好的脱脂效果。该脱脂剂含氧化剂、表面活性剂、高价金属离子等成分,对铝金属有弱浸蚀能力,可长期使用,脱脂性能稳定可靠。本工艺特别适用于铝型材的阳极氧化处理,槽液可以取自阳极氧化废酸,成本较低,并可以防止油污量大时油污布满液面、将油污带入后序槽的危险。
本文研究了脱脂剂含量、温度、时间及游离酸浓度对铝合金表面清洗效果的影响。
2实验材料制备
(1)试片的规格及预处理选用工业纯铝作标准试片,其规格为50 mm×50 mm×(1~2)mm。将试片在30%的HNO3溶液中脱脂,水洗,4%的NaOH溶液腐蚀,水洗,30% HNO3中和、出光。热风吹干。经此处理后。试片表面原有的油污和自然氧化皮被除净。从而使每个试片的表面状态均匀一致。
(2)人造工业油污的配制 将工业凡士林、20#、30#机油混合,加热到120℃,使固体物完全熔化,搅拌均匀,冷却到室温,加入3%食盐水和细砂,搅匀备用。
3实验方法及步骤
将准备好的铝试片浸入人造工业油污中静置1 h,取出后垂直悬挂于空气中老化24 h,再用自来水沸煮3 min,除去试片表面的浮油,吹干,油污涂覆量应控制在0. 08~0. 19g/dm2。
把上述涂覆油污的试片垂直放置于脱脂溶液中浸泡,不施加机械搅拌进行脱脂处理,水洗,热风吹干,待试片冷却至室温后,用分析天平准确称重,重量为W1。再将试片浸入三氯乙烷中,在室温下不断摇动试片,浸泡3 min,将试片上的残余油污完全洗净。吹干,准确称重,重量为W2。试片的两次重量差(W1~W2)即为残余油量,计算试片单位面积的残余油量,就可比较脱脂溶液的脱脂性能。单位面积的残余油量愈小,脱脂性能愈佳。
4实验结果与讨论
酸性脱脂剂主要由无机酸、氧化剂、高价金属离子及表面活性剂等成分组成。其中,无机酸可以是H2SO4、H3PO4、HF、亚磷酸、硼酸等。H2SO4对铝合金有弱浸蚀能力,能润湿整个金属表面,使自然氧化膜溶解,油污松动。高价金属离子一般选用Fe3+,一般以硫酸铁、硝酸铁等铁盐形式加入,以加速铝的腐蚀,铁离子可以在铝表面发生置换反应,形成微电池,使铝表面产生微量氢气,将油污带出铝表面;同时,铁离子还可以抑制脱脂液对不锈钢设备的腐蚀。氧化剂主要是H2O2或NO2- (如NaNO2)等,作为Fe3+的稳定剂,将还原产生的二价铁离子氧化成为三阶铁离子,并起到Fe3+类似的功能。由于亚硝酸盐在酸性溶液中容易释放出N0x有毒气体,所以最好使用H2O2作为氧化剂。加入表面活性剂可以提高铝合金表面的润湿性,降低油污的附着力,使油污乳化均匀地分散在脱脂液中,在酸性脱脂液中,选择耐酸性强的非离子或阴离子表面活性剂如长链脂肪醇聚氧乙烯醚、烷基酚聚氧乙烯醚、烷基二甲基胺氧化物为最佳。
4.1脱脂剂用量的影响
脱脂剂用量对残余油量的影响见图1。由图可见,脱脂剂的添加范围应为20~30 ml/L,最佳为25 ml/L,如果用量低于20ml/L,脱脂剂中各有效成分含量不足,在上述工艺条件下,不能有效溶解自然氧化膜,油污不能完全松动,随着脱脂剂含量的添加,残余油污迅速减少。脱脂剂含量达到25ml/L时,自然氧化膜即能完全溶解,油污绝大部分得到松动脱除,继续增加脱脂剂的含量,残余油量几乎不变,说明含量25 ml/L以后继续添加脱脂剂只会增加物料消耗,不能进一步改善脱脂效果。
铝及铝合金的除油。早期是延用钢铁的除油工艺。即槽液为Na2CO3、Na2SiO3、Na3PO4溶液,操作温度40~70℃,时间5~15 min,这种工艺性能稳定,寿命长,但槽液成本高,不易洗净,现己基本不用。60年代,人们采用NaOH或Na2CO3添加Na3PO4、络合剂、非离子表面活性剂、阴离子表面活性剂在室温下脱脂,时间3~5 min,除油效率高,成本低,节能,但槽液易产生絮状沉淀,络合剂、表面活性剂易带入后续槽形成污染,目前仅有少数厂仍在使用。从80年代开始,酸性脱脂逐步普及,槽液为H2SO4或H3PO4加入HF、Fe3+、H2O2、NO2-和非离子表面活性剂,室温下操作,时间为3~5 min。这种工艺效率高,不污染后续槽,是较好的脱脂工艺。现在应用越来越广泛。
本研究以硫酸为基液,加特制的脱脂剂,在室温条件下,勿需机械搅拌等辅助,即可获得良好的脱脂效果。该脱脂剂含氧化剂、表面活性剂、高价金属离子等成分,对铝金属有弱浸蚀能力,可长期使用,脱脂性能稳定可靠。本工艺特别适用于铝型材的阳极氧化处理,槽液可以取自阳极氧化废酸,成本较低,并可以防止油污量大时油污布满液面、将油污带入后序槽的危险。
本文研究了脱脂剂含量、温度、时间及游离酸浓度对铝合金表面清洗效果的影响。
2实验材料制备
(1)试片的规格及预处理选用工业纯铝作标准试片,其规格为50 mm×50 mm×(1~2)mm。将试片在30%的HNO3溶液中脱脂,水洗,4%的NaOH溶液腐蚀,水洗,30% HNO3中和、出光。热风吹干。经此处理后。试片表面原有的油污和自然氧化皮被除净。从而使每个试片的表面状态均匀一致。
(2)人造工业油污的配制 将工业凡士林、20#、30#机油混合,加热到120℃,使固体物完全熔化,搅拌均匀,冷却到室温,加入3%食盐水和细砂,搅匀备用。
3实验方法及步骤
将准备好的铝试片浸入人造工业油污中静置1 h,取出后垂直悬挂于空气中老化24 h,再用自来水沸煮3 min,除去试片表面的浮油,吹干,油污涂覆量应控制在0. 08~0. 19g/dm2。
把上述涂覆油污的试片垂直放置于脱脂溶液中浸泡,不施加机械搅拌进行脱脂处理,水洗,热风吹干,待试片冷却至室温后,用分析天平准确称重,重量为W1。再将试片浸入三氯乙烷中,在室温下不断摇动试片,浸泡3 min,将试片上的残余油污完全洗净。吹干,准确称重,重量为W2。试片的两次重量差(W1~W2)即为残余油量,计算试片单位面积的残余油量,就可比较脱脂溶液的脱脂性能。单位面积的残余油量愈小,脱脂性能愈佳。
4实验结果与讨论
酸性脱脂剂主要由无机酸、氧化剂、高价金属离子及表面活性剂等成分组成。其中,无机酸可以是H2SO4、H3PO4、HF、亚磷酸、硼酸等。H2SO4对铝合金有弱浸蚀能力,能润湿整个金属表面,使自然氧化膜溶解,油污松动。高价金属离子一般选用Fe3+,一般以硫酸铁、硝酸铁等铁盐形式加入,以加速铝的腐蚀,铁离子可以在铝表面发生置换反应,形成微电池,使铝表面产生微量氢气,将油污带出铝表面;同时,铁离子还可以抑制脱脂液对不锈钢设备的腐蚀。氧化剂主要是H2O2或NO2- (如NaNO2)等,作为Fe3+的稳定剂,将还原产生的二价铁离子氧化成为三阶铁离子,并起到Fe3+类似的功能。由于亚硝酸盐在酸性溶液中容易释放出N0x有毒气体,所以最好使用H2O2作为氧化剂。加入表面活性剂可以提高铝合金表面的润湿性,降低油污的附着力,使油污乳化均匀地分散在脱脂液中,在酸性脱脂液中,选择耐酸性强的非离子或阴离子表面活性剂如长链脂肪醇聚氧乙烯醚、烷基酚聚氧乙烯醚、烷基二甲基胺氧化物为最佳。
4.1脱脂剂用量的影响
脱脂剂用量对残余油量的影响见图1。由图可见,脱脂剂的添加范围应为20~30 ml/L,最佳为25 ml/L,如果用量低于20ml/L,脱脂剂中各有效成分含量不足,在上述工艺条件下,不能有效溶解自然氧化膜,油污不能完全松动,随着脱脂剂含量的添加,残余油污迅速减少。脱脂剂含量达到25ml/L时,自然氧化膜即能完全溶解,油污绝大部分得到松动脱除,继续增加脱脂剂的含量,残余油量几乎不变,说明含量25 ml/L以后继续添加脱脂剂只会增加物料消耗,不能进一步改善脱脂效果。
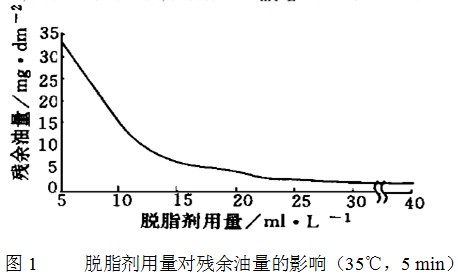
4.2温度的影响
铝及铝合金能在相当宽的温度范围内进行脱脂,使用适当的温度有利于保证脱脂性能的稳定和脱脂效果的可靠性。温度过低时,脱脂液对金属氧化物的溶解能力相对较弱,提高脱脂剂浓度并不能显著提高其清洗能力,而使脱脂时间拖得过长,通常温度每提高10℃,化学反应速度增加1倍,所以提高温度,有助于提高脱脂液对铝的浸蚀能力和表面活性剂的乳化能力,并降低油污的粘度,使油污迅速离开金属表面。一般来说,温度愈高,脱脂效果愈佳。
但是,温度太高会增加能量消耗,使脱脂剂对金属的腐蚀太强,产生局部过腐蚀,如变色、雪花斑、点蚀等。如果温度超过表面活性剂的浊点,脱脂剂的乳化能力显著下降,脱脂效果反而变差。同时,温度太高槽液会产生酸雾,腐蚀车间设备,并促使脱脂液中的Fe3+水解和沉淀,污染槽液,增加物料消耗。因此,脱脂槽液的温度必须适当,应从除油效果、基体腐蚀、能量消耗、操作条件等多方面因素考虑。
图2显示了脱脂温度对残余油量的影响,脱脂剂用量25ml/L.处理时间5 min。结果表明,脱脂温度控制在35℃为最佳。
铝及铝合金能在相当宽的温度范围内进行脱脂,使用适当的温度有利于保证脱脂性能的稳定和脱脂效果的可靠性。温度过低时,脱脂液对金属氧化物的溶解能力相对较弱,提高脱脂剂浓度并不能显著提高其清洗能力,而使脱脂时间拖得过长,通常温度每提高10℃,化学反应速度增加1倍,所以提高温度,有助于提高脱脂液对铝的浸蚀能力和表面活性剂的乳化能力,并降低油污的粘度,使油污迅速离开金属表面。一般来说,温度愈高,脱脂效果愈佳。
但是,温度太高会增加能量消耗,使脱脂剂对金属的腐蚀太强,产生局部过腐蚀,如变色、雪花斑、点蚀等。如果温度超过表面活性剂的浊点,脱脂剂的乳化能力显著下降,脱脂效果反而变差。同时,温度太高槽液会产生酸雾,腐蚀车间设备,并促使脱脂液中的Fe3+水解和沉淀,污染槽液,增加物料消耗。因此,脱脂槽液的温度必须适当,应从除油效果、基体腐蚀、能量消耗、操作条件等多方面因素考虑。
图2显示了脱脂温度对残余油量的影响,脱脂剂用量25ml/L.处理时间5 min。结果表明,脱脂温度控制在35℃为最佳。
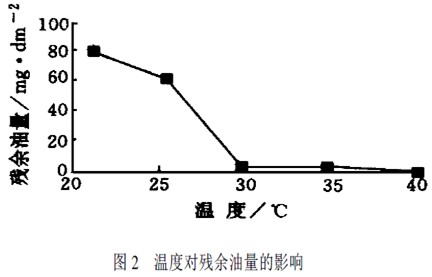
4.3处理时间的影响
铝及铝合金表面有一层自然氧化膜,附有油污,铝屑泥沙汗水等杂质。氧化膜的溶解速度取决于Al2O3和酸反应的速度及铝离子的扩散速度,并与酸的浓度和操作温度有关,增加脱脂处理的时间,有利于提高脱脂效果。但是,处理时间太长,会使整个生产工艺过程过长,降低生产效率。图3显示了处理时间对残余油量的影响。结果表明,在35℃时,适宜的脱脂时间为5~7 min。
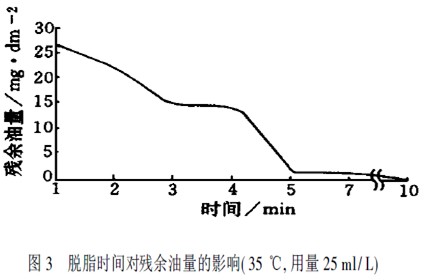
铝及铝合金表面有一层自然氧化膜,附有油污,铝屑泥沙汗水等杂质。氧化膜的溶解速度取决于Al2O3和酸反应的速度及铝离子的扩散速度,并与酸的浓度和操作温度有关,增加脱脂处理的时间,有利于提高脱脂效果。但是,处理时间太长,会使整个生产工艺过程过长,降低生产效率。图3显示了处理时间对残余油量的影响。结果表明,在35℃时,适宜的脱脂时间为5~7 min。
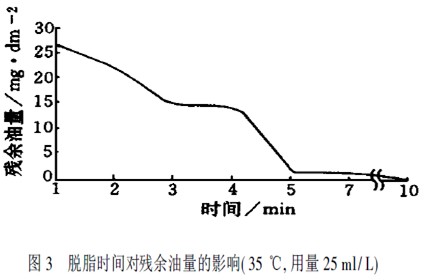
4.4游离酸浓度的影响
为了提高脱脂效率,在酸性脱脂工艺中常采用混合酸如H2SO4+H3PO4,H2SO4+ HF等,所以一般不用某种酸的每升克数来表示酸的浓度,而是取一定量的脱脂液,用1 mol/L的NaOH溶液中和滴定,用滴定至中性时NaOH溶液的消耗量来表示脱脂剂中游离酸的浓度。NaOH溶液的消耗量愈大,游离酸的浓度愈高,其关系符合当量定律。
本研究取5 ml脱脂液,用0.967 1 m ol/L的NaOH溶液滴定,脱脂剂25ml/L,温度35℃。处理时间5 min。消耗NaOH溶液的毫升数与残余油量的关系见表。
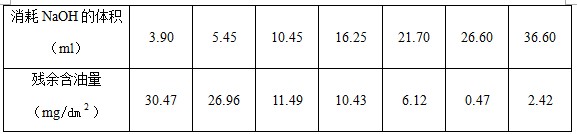
为了提高脱脂效率,在酸性脱脂工艺中常采用混合酸如H2SO4+H3PO4,H2SO4+ HF等,所以一般不用某种酸的每升克数来表示酸的浓度,而是取一定量的脱脂液,用1 mol/L的NaOH溶液中和滴定,用滴定至中性时NaOH溶液的消耗量来表示脱脂剂中游离酸的浓度。NaOH溶液的消耗量愈大,游离酸的浓度愈高,其关系符合当量定律。
本研究取5 ml脱脂液,用0.967 1 m ol/L的NaOH溶液滴定,脱脂剂25ml/L,温度35℃。处理时间5 min。消耗NaOH溶液的毫升数与残余油量的关系见表。
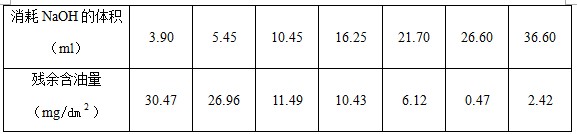
从表可以看出。游离酸大于26.6点时,残余油量极少,向且变化趋于平缓,这时酸的浓度与15%的H2SO4相当,而常用硫酸阳极氧化槽液即为l5%的H2SO4,所以酸性脱脂液可以采用废旧的阳极氧化槽液配制,从而大大降低酸性脱脂的成本。
5结论
本文研究的酸性脱脂剂在含油污的铝及铝合金制品表面清洗工艺中具有特别的优点,在常温下能保持其浸蚀能力,对各种铝制品都有极好的清洗效果。脱脂液能允许铝离子有极高的含量,去污能力有良好的耐久性。本脱脂剂能抑制酸对不锈钢设备的腐蚀,保证清洗设备的使用寿命。
本脱脂工艺适用于铝及铝合金的阳极氧化、化学氧化、电镀、涂漆等工艺的前处理,特别是铝型材的阳极氧化处理,可以缩短碱腐蚀时间,使基体在碱腐蚀后保持较高的金属光泽。对后续槽液不会产生不良影响。脱脂槽液采用阳极氧化废硫酸配制,减少了废酸的环保处理和排放,降低了生产成本。
本文研究的酸性脱脂工艺规范如下:
H2SO4 100~180 g/L
脱脂剂 20~30 ml/L
温 度 20~40℃
时 间 3~7 min
5结论
本文研究的酸性脱脂剂在含油污的铝及铝合金制品表面清洗工艺中具有特别的优点,在常温下能保持其浸蚀能力,对各种铝制品都有极好的清洗效果。脱脂液能允许铝离子有极高的含量,去污能力有良好的耐久性。本脱脂剂能抑制酸对不锈钢设备的腐蚀,保证清洗设备的使用寿命。
本脱脂工艺适用于铝及铝合金的阳极氧化、化学氧化、电镀、涂漆等工艺的前处理,特别是铝型材的阳极氧化处理,可以缩短碱腐蚀时间,使基体在碱腐蚀后保持较高的金属光泽。对后续槽液不会产生不良影响。脱脂槽液采用阳极氧化废硫酸配制,减少了废酸的环保处理和排放,降低了生产成本。
本文研究的酸性脱脂工艺规范如下:
H2SO4 100~180 g/L
脱脂剂 20~30 ml/L
温 度 20~40℃
时 间 3~7 min
上一篇: 铝合金阳极氧化前处理工艺的改进
下一篇: 涂装工艺的选择和前处理的重要性