铝件无硝酸化学抛光工艺试验总结
铝件无硝酸化学抛光工艺试验总结
罗耀宗 巴烽翔(上海自动化仪表一厂)
一、前 言
铝和铝合金在氧化前往往要经过化学除油和抛光等工序,为了取得表面光亮的铝和铝合金,除了进行机械抛光外,对光亮度要求较高的零件还需进行化学抛光或电化学抛光。而化学抛光的特点是设备简单,节省能源,效率高和成本低,而且不受零件形状和尺寸的限制,对小、薄和形状复杂的零件都可加工,对盲孔或深槽的内腔也均可加工。因此,化学抛光已广泛地在铝及铝合金的表面处理工艺中得到应用。然而长期来,铝及锅合金的化学抛光配方中,硝酸是必不可少的原料之一,因此产生了大量的氮氧化物气体,影响操作工人的身体健康和周围环境。
我厂有部分铝制零件在氧化前须进行化学抛光工序,以前采用的是以H3PO4,H2SO4和HNO3为主体的化学抛光溶液,由于没有较好废气治理措施,因此产生的大量NOx气体直接影响到操作工人身体健康和仪表装配大楼的仪表质量。为了消除该工序上产生的NOx污染,主要可以通过以下二个途径。
1.安装一套NOx:废气净化塔。
2.进行工艺改革,不用HNO3。
根据目前我厂情况。用第二种方法,简单有效,同时投资,仅为第一种方法的1/20以下,这样可以彻底消除NOx危害,不会带来二次污染。同时还可以节约对废气净化塔维护保养的人力和化工原料消耗。
二、化学抛光工艺探讨
从我们目前掌握的情况来看,国内外在铝件化学抛光工艺上,还大多采用HNO3成份,只有少数单位报导选用了无硝酸化学抛光工艺。但选择的工艺配方相差较大,效率也当然不同。所以为了能满足我厂的情况,我们做了大量的筛选工作。
1.磷酸、硫酸型抛光液
①抛光时间试验:
这种工艺配方主要是原来的硝酸配方中,革掉硝酸,调整配比而成。我们将H3PO4和H2SO4分别配成3:7;5:5和7:3;几种配比,温度在110℃情况下,样板在溶液中的腐蚀速度变化如表一;

我厂有部分铝制零件在氧化前须进行化学抛光工序,以前采用的是以H3PO4,H2SO4和HNO3为主体的化学抛光溶液,由于没有较好废气治理措施,因此产生的大量NOx气体直接影响到操作工人身体健康和仪表装配大楼的仪表质量。为了消除该工序上产生的NOx污染,主要可以通过以下二个途径。
1.安装一套NOx:废气净化塔。
2.进行工艺改革,不用HNO3。
根据目前我厂情况。用第二种方法,简单有效,同时投资,仅为第一种方法的1/20以下,这样可以彻底消除NOx危害,不会带来二次污染。同时还可以节约对废气净化塔维护保养的人力和化工原料消耗。
二、化学抛光工艺探讨
从我们目前掌握的情况来看,国内外在铝件化学抛光工艺上,还大多采用HNO3成份,只有少数单位报导选用了无硝酸化学抛光工艺。但选择的工艺配方相差较大,效率也当然不同。所以为了能满足我厂的情况,我们做了大量的筛选工作。
1.磷酸、硫酸型抛光液
①抛光时间试验:
这种工艺配方主要是原来的硝酸配方中,革掉硝酸,调整配比而成。我们将H3PO4和H2SO4分别配成3:7;5:5和7:3;几种配比,温度在110℃情况下,样板在溶液中的腐蚀速度变化如表一;

从以上试验结果来看,从H3PO450%,H2SO450%的配比溶液中,获得的抛光件最为均匀,但对金属溶解量比配方1、3来得慢。如图1所示。
从图2可以看出,在零件入槽后,开始时金属溶解速度较慢,在2 min时溶解速度加快,若再延长时间,溶解速度又减慢,而与H2SO4的含量变化无关。这可能是因为随着酸的消耗,溶解减慢,也有可能随着溶液里溶解的Al3+增加,溶液粘度增加,溶解速度减慢。
②溶液温度试验:
图3是溶液配比随温度变化对金属溶解速度的变化曲线,从中可知,不同硫酸含量溶液中,对金属溶解速度随温度升高而加快,但过高的温度,会引起零件发花,造成不均匀溶解,因此过高的温度对抛光效果是不利的。从多次不同温度试验结果同样证明了H3PO450%,H2SO450%的溶液对金属溶解速度最慢。而H3PO430%或70%对溶解速度影响如图3所示。
③抛光效果:
从抛光效果来看,随着H2SO4含量的增加,零件的光亮性增加。因为条件所限,没有用仪器测定,只是用直观效果评定。或用50倍显微镜下观查效果评定。从中发现,随着H2SO4的增加虽说直观效果良好,但对零件的整平抛光较差,样板表面出现划痕状金属纹路腐蚀,在显微镜下更为清楚可见。随着H3PO4含量增加,整平抛光效果提高,零件表面均匀腐蚀溶解,但直观抛光效果较差,不如H2SO4高的好。为此我们认为基础溶液选择H3PO4、H2SO4比例相等的较为合适。
2.磷酸、硫酸、盐酸型抛光液。
长期以来很多资料认为,对铝件抛光液严禁采用HCI,因为它会使铝件表面产生点状腐蚀或使零件表面发花,发雾等等。这是事实,但从大量试验证明,只要工艺配比合理,不但可以避免以上的不足,还可促使零件光亮效果,当添加了少量添加剂后,其光亮效果明显优于磷酸,硫酸溶液,同时还可降低使用温度。试验的典型配方如下:
磷酸H3PO4 45%
硫酸H2SO4 45%
盐酸HCI 10%
Al粉 0.5 g/L
组合添加剂 少量
T 110℃
时间 2 min
经以上工艺处理后的铝件,表面光亮,但因溶液中含有HCl,如零件冲洗不净,就会使表面产生雾状,严重影响光亮效果。如果溶液中HCl含量过高,使铝件出现点状腐蚀,这是用HCl要掌握的要点之一。为了防止零件产生雾状表面,除了洗净外,还可增加一道pH约等于9的溶液,使带酸的零件能得到中和后洗净烘干。这一工艺虽有较好的效果,但因溶液温度高,由于CI-的存在,对选用的容器和加热管材有特殊高的要求,否则会造成严重腐蚀损坏,即使防腐性能优良的钛材也难逃厄运,因此在一般情况下,难以使用,只有在玻璃或搪瓷容器里才能使用。
三、添加剂的效果
为了使化学抛光零件更光亮,可在溶液中少量加入些能促使抛光性能改善的添加剂,有些资料报导了在H3PO4、H2SO4体系的抛光液中加入少量多硫化合物、铜离子等添加物能改善化学抛光效果。为此我们进行了一些试验。试验中发现,铜离子的加入能提高铝件的抛光效果,但零件表面容易产生一层黑色挂灰,而且这层挂灰随着含量增加而增多,这也许是置换铜造成的,虽然用手一擦能擦去,但大批生产,或复杂零件就比较麻烦,丽用化学去膜又会用到有害物铬酸或硝酸,给废水或废气处理带来新的内容,所以我们认为不宜多用。含硫化合物虽然很多,但具体效果怎样也很难说,某些含硫有机物对光亮有一定作用,但易在高温下分解,寿命较短。而无机含硫物质大多没有明显效果,从有限的试验结果认为少量添加硫化钠是最有希望的无机含硫添加剂。
从多种金属离子添加剂试验中,多次证明添加镍离子是有一定光亮效果的,甚至比铜更好,同时又不象铜离子的加入会使零件表面产生挂灰的现象。然而从我们判断光亮效果的方法来看,很难看出铜和镍同时加入的光亮叠加效果。所以我们认为为了减少挂灰现象添加镍比铜好。
从试验结果看,少量水的加入,对提高光亮度可能是有利的。一般在5~15%较好,而过多的水往往会造成零件过快腐蚀,或不均匀点状腐蚀。水的加入还可使操作温度降低5~10℃。此外加入少量表面活性剂和醋酸,对改善零件化抛效果也有一定好处。
四、处理工艺及流程
1.工艺配方:
在以上的一系列试验中,我们拟定了如下的工艺配方:
磷酸H3PO4 47%
硫酸H2SO4 48%
水H2O 5%
铝粉A1 0.5 g/L
组合添加剂 10 ml/L
温度 105~120℃
③抛光效果:
从抛光效果来看,随着H2SO4含量的增加,零件的光亮性增加。因为条件所限,没有用仪器测定,只是用直观效果评定。或用50倍显微镜下观查效果评定。从中发现,随着H2SO4的增加虽说直观效果良好,但对零件的整平抛光较差,样板表面出现划痕状金属纹路腐蚀,在显微镜下更为清楚可见。随着H3PO4含量增加,整平抛光效果提高,零件表面均匀腐蚀溶解,但直观抛光效果较差,不如H2SO4高的好。为此我们认为基础溶液选择H3PO4、H2SO4比例相等的较为合适。
2.磷酸、硫酸、盐酸型抛光液。
长期以来很多资料认为,对铝件抛光液严禁采用HCI,因为它会使铝件表面产生点状腐蚀或使零件表面发花,发雾等等。这是事实,但从大量试验证明,只要工艺配比合理,不但可以避免以上的不足,还可促使零件光亮效果,当添加了少量添加剂后,其光亮效果明显优于磷酸,硫酸溶液,同时还可降低使用温度。试验的典型配方如下:
磷酸H3PO4 45%
硫酸H2SO4 45%
盐酸HCI 10%
Al粉 0.5 g/L
组合添加剂 少量
T 110℃
时间 2 min
经以上工艺处理后的铝件,表面光亮,但因溶液中含有HCl,如零件冲洗不净,就会使表面产生雾状,严重影响光亮效果。如果溶液中HCl含量过高,使铝件出现点状腐蚀,这是用HCl要掌握的要点之一。为了防止零件产生雾状表面,除了洗净外,还可增加一道pH约等于9的溶液,使带酸的零件能得到中和后洗净烘干。这一工艺虽有较好的效果,但因溶液温度高,由于CI-的存在,对选用的容器和加热管材有特殊高的要求,否则会造成严重腐蚀损坏,即使防腐性能优良的钛材也难逃厄运,因此在一般情况下,难以使用,只有在玻璃或搪瓷容器里才能使用。
三、添加剂的效果
为了使化学抛光零件更光亮,可在溶液中少量加入些能促使抛光性能改善的添加剂,有些资料报导了在H3PO4、H2SO4体系的抛光液中加入少量多硫化合物、铜离子等添加物能改善化学抛光效果。为此我们进行了一些试验。试验中发现,铜离子的加入能提高铝件的抛光效果,但零件表面容易产生一层黑色挂灰,而且这层挂灰随着含量增加而增多,这也许是置换铜造成的,虽然用手一擦能擦去,但大批生产,或复杂零件就比较麻烦,丽用化学去膜又会用到有害物铬酸或硝酸,给废水或废气处理带来新的内容,所以我们认为不宜多用。含硫化合物虽然很多,但具体效果怎样也很难说,某些含硫有机物对光亮有一定作用,但易在高温下分解,寿命较短。而无机含硫物质大多没有明显效果,从有限的试验结果认为少量添加硫化钠是最有希望的无机含硫添加剂。
从多种金属离子添加剂试验中,多次证明添加镍离子是有一定光亮效果的,甚至比铜更好,同时又不象铜离子的加入会使零件表面产生挂灰的现象。然而从我们判断光亮效果的方法来看,很难看出铜和镍同时加入的光亮叠加效果。所以我们认为为了减少挂灰现象添加镍比铜好。
从试验结果看,少量水的加入,对提高光亮度可能是有利的。一般在5~15%较好,而过多的水往往会造成零件过快腐蚀,或不均匀点状腐蚀。水的加入还可使操作温度降低5~10℃。此外加入少量表面活性剂和醋酸,对改善零件化抛效果也有一定好处。
四、处理工艺及流程
1.工艺配方:
在以上的一系列试验中,我们拟定了如下的工艺配方:
磷酸H3PO4 47%
硫酸H2SO4 48%
水H2O 5%
铝粉A1 0.5 g/L
组合添加剂 10 ml/L
温度 105~120℃
时间 1~3min
2.工艺流程:
无硝酸化学抛光的工艺并不比硝酸化学抛光复杂,其操作工序和方法基本—样,现采用的工艺流程如下:
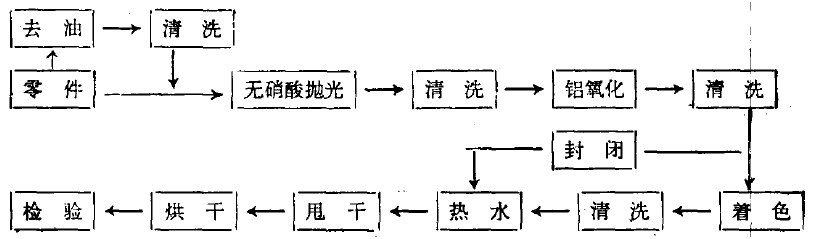
3.工作原理及主要成份作用
根据粘膜机理认为,由于在被抛光试片表面上生成了—层薄膜,这层薄膜在凹洼部份和棱角上较在凸起部分上更为厚些,因为抛光溶液在凸起部分上溶解作用更为剧烈些,所以凸起部分被除去,表面就整平了。当薄膜具有一定粘度时,就能完成这种作用。其溶液中各主要成份和条件作用如下:
①H3PO4:由于有较高浓度的H3PO4溶液对金属具有较低的溶解速度,比金属在碱性中损耗量小,并具有—定的光亮作用和整平作用;
②H2SO4:可以加快抛光速度,但整平效果不佳;
③铝粉:增加溶液粘性,改善光亮效果(一次性添加);
④H2O:降低溶液工作温度,提高零件光亮度(一次性添加);
⑤添加剂:降低溶液表面张力,提高零件抛光亮度;
⑥温度:温度过低,反应速度慢,零件无光。温度大于130℃,零件过蚀速度加快,不均匀,光亮度显著降低,易造成过蚀现象。一般在110~120℃较好;
⑦时间:主要根据零件达到光亮要求而又不影响零件几何尺寸、螺孔精度而定。
4.注意事项
从试验结果认为,溶液中添加水,对光亮有—定作用,有资料认为其含量可达15%,乃至更多。我们认为在新配槽时,可少量加入5%左右的水,以后就不必添加。因为溶液有强烈的吸湿性,把空气中的水份吸入溶液使之冲淡。我们曾做了如下的试验,在体积100 mL的烧杯里,各配50 mL不同浓度H2SO4溶液,溶液与空气接触面积约20 cm2,图2是不同浓度H2SO4吸湿情况。
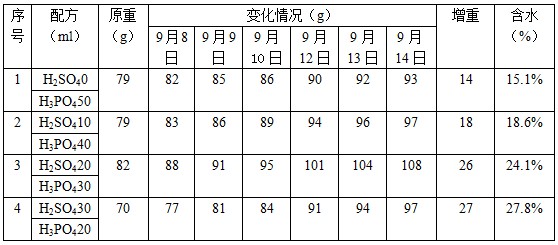
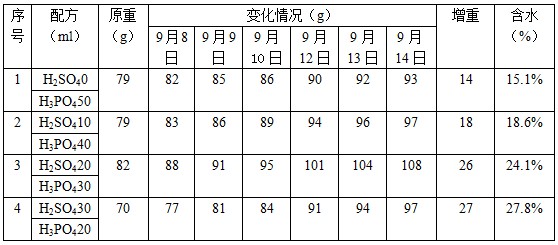
从以上图表能说明以下3个问题:
(1)H2SO4和H3PO4都有吸湿性,溶液逐步变淡。
(2)随着H2SO4含量增加,吸湿量增加。
(3)随着时间延长,不同浓度H2SO4的溶液吸湿量逐步增加。如图4。
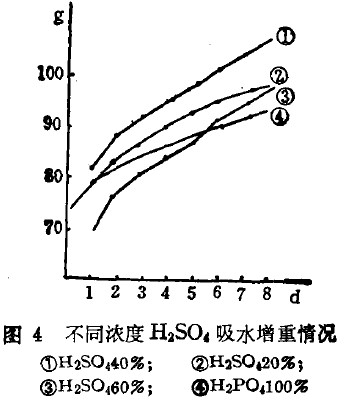
从一系列试验结果证明,溶液有较强烈的吸湿性,那么由于工作温度较高,吸收的水份是否会很快地蒸发呢?于是分别做了不同温度下,水份蒸发试验.即在约20cm2接触面的100mL烧杯中,将含有一定水量不同浓度的H2SO4溶液分别加热到110℃,130℃,150℃并在这一温度下分别保留15min后,称其溶液失重情况如图5从中可以看出:
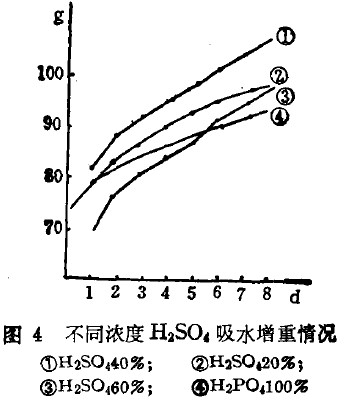
从一系列试验结果证明,溶液有较强烈的吸湿性,那么由于工作温度较高,吸收的水份是否会很快地蒸发呢?于是分别做了不同温度下,水份蒸发试验.即在约20cm2接触面的100mL烧杯中,将含有一定水量不同浓度的H2SO4溶液分别加热到110℃,130℃,150℃并在这一温度下分别保留15min后,称其溶液失重情况如图5从中可以看出:
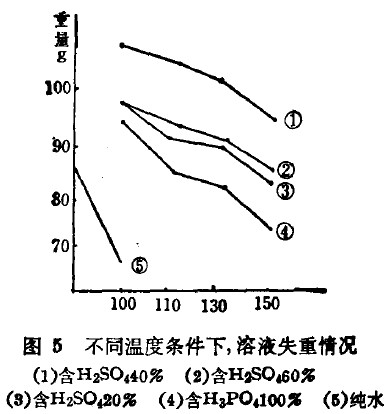
(1)随温度升高,水份蒸发加快,当温度达150℃时,蒸发的幅度更大;
(2)从蒸发具体数值来看,随着H2SO4含量增加蒸发速度减慢;
(3)纯H3PO4的蒸发速度比含H2SO4溶液蒸发速度快;
(4)水的蒸发温度低,速度比含酸的快得多。
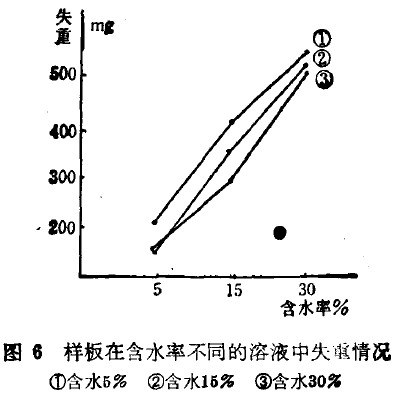
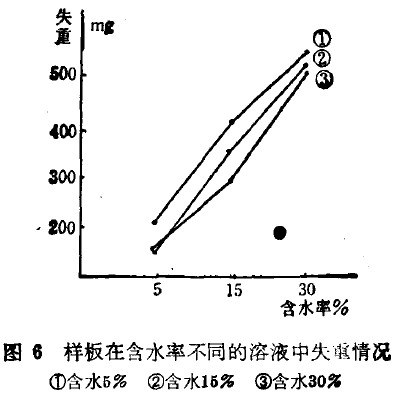
从表2可以看出随着H2SO4含量增加,吸湿性增加,从图5可以看出随H2SO4含量增加水份蒸发速度减慢。这就提醒我们在日常操作过程中,要注意尽量防止溶液的大量吸湿。图6可以看出从大量的试验证明,随着水份的增加,零件腐蚀速度明显加快,腐蚀不均匀,化抛时,气泡大量增加,使零件易出现雾状或点状腐蚀。为此认为过量的水份对抛光效果不利。然而为了保持一定的含水率,新配槽时,水份少加,以5%左右为佳,平时停工时,槽上加盖密闭,使溶液与空气隔离吸湿性明显降低。表3是含水和不含水的二组H2SO4溶液与空气接触和隔离后的吸湿变化情况。
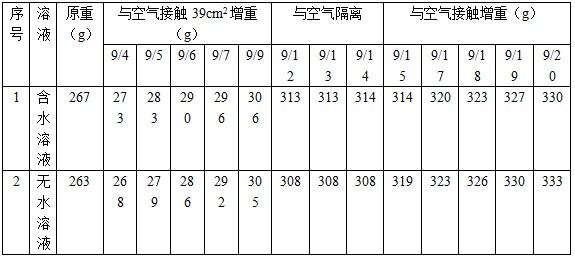
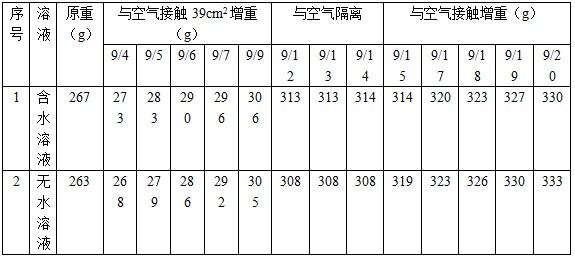
从中可以明显看出与空气接触,溶液增重,与空气隔离,溶液增重停止,再与空气接触,溶液又增重。所以为防止溶液中水份大量增加,加盖隔离空气是有效的,虽然很难做到密封,但吸湿性会大为降低。否则将会使溶液很快稀释而报废。
五、结束语
铝件无硝酸化学抛光工艺投产后,解决了用老工艺产生黄龙气体的危害,由于直接从工艺改革着手,从而根本解决了NOx的污染,该工艺有以下特点:
①不产生NOx有害气体。省去了用硝酸抛光所需的NOx治理设备;
②排出废水容易治理,同时给其它金属离子废水处理带来方便,有利于沉淀分离;
③投资省,上马快,工艺简单,操作稳定;
以上是我们在铝件无硝酸抛光工艺上所做的一点工作,虽然取得了一些效果和实验数据,改善了环境。但还有很多工作要做。试验认为含锌及铜的铝合金的抛光不能令人满意,含硅铝合金在此溶液中还无法获得抛光效果。而对纯铝或铝-镁-硅系合金才可得到较好的抛光效果。因此本工艺只能对高纯铝和高纯铝镁合金或铝-镁-硅合金适用。
上一篇: WXP铝件无黄烟化学抛光
下一篇: 缓蚀剂在化学抛光液中对铝的缓蚀效果